solution
IDAJのMBD・MBSEソリューション
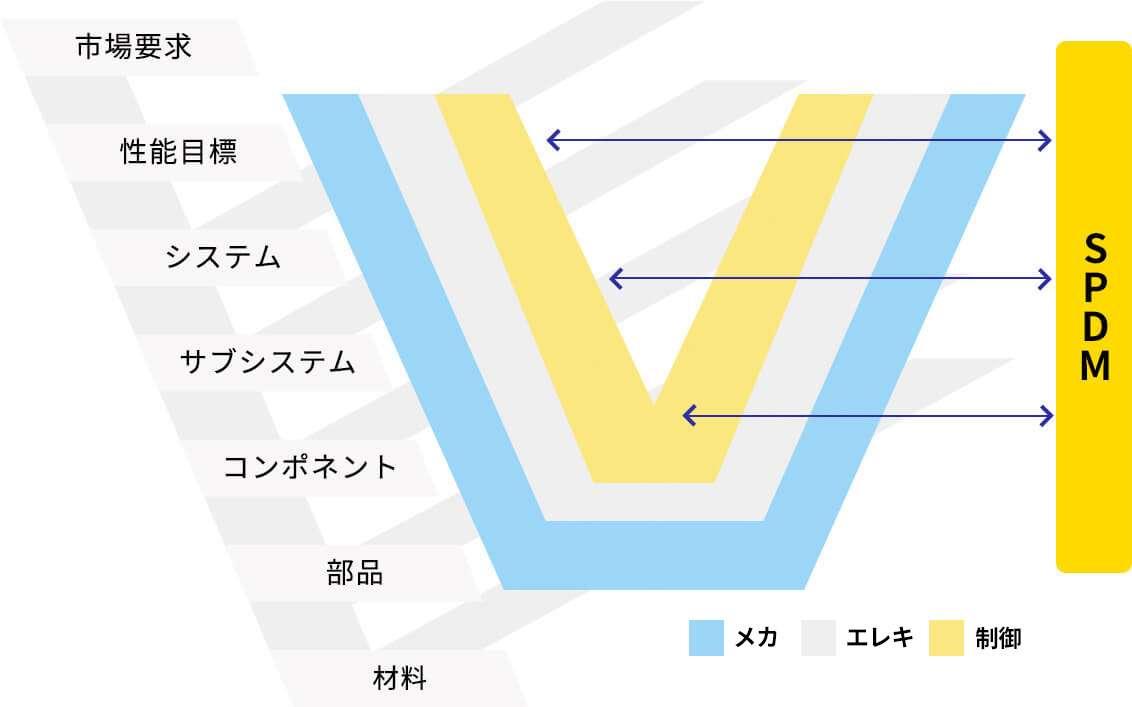
「設計プロセスに根付いた」MBD・MBSEプロセスの導入を支援します
現状の開発フローにおける様々な設計課題を解決し、高いレベルでの協調設計を実現することをMBD・MBSEの真の目的ととらえ、設計開発の”ありたき姿”の具現化をサポートします。
-
課題の分析・推進計画の策定を含むお客様のMBD推進を
全面的にサポート - 企画から製品まで開発フロー全体をカバーするソリューションを提供
- 運用・管理までを見据えたプロセスの構築と仕組み作りを支援
development
一般的なMBD開発の形
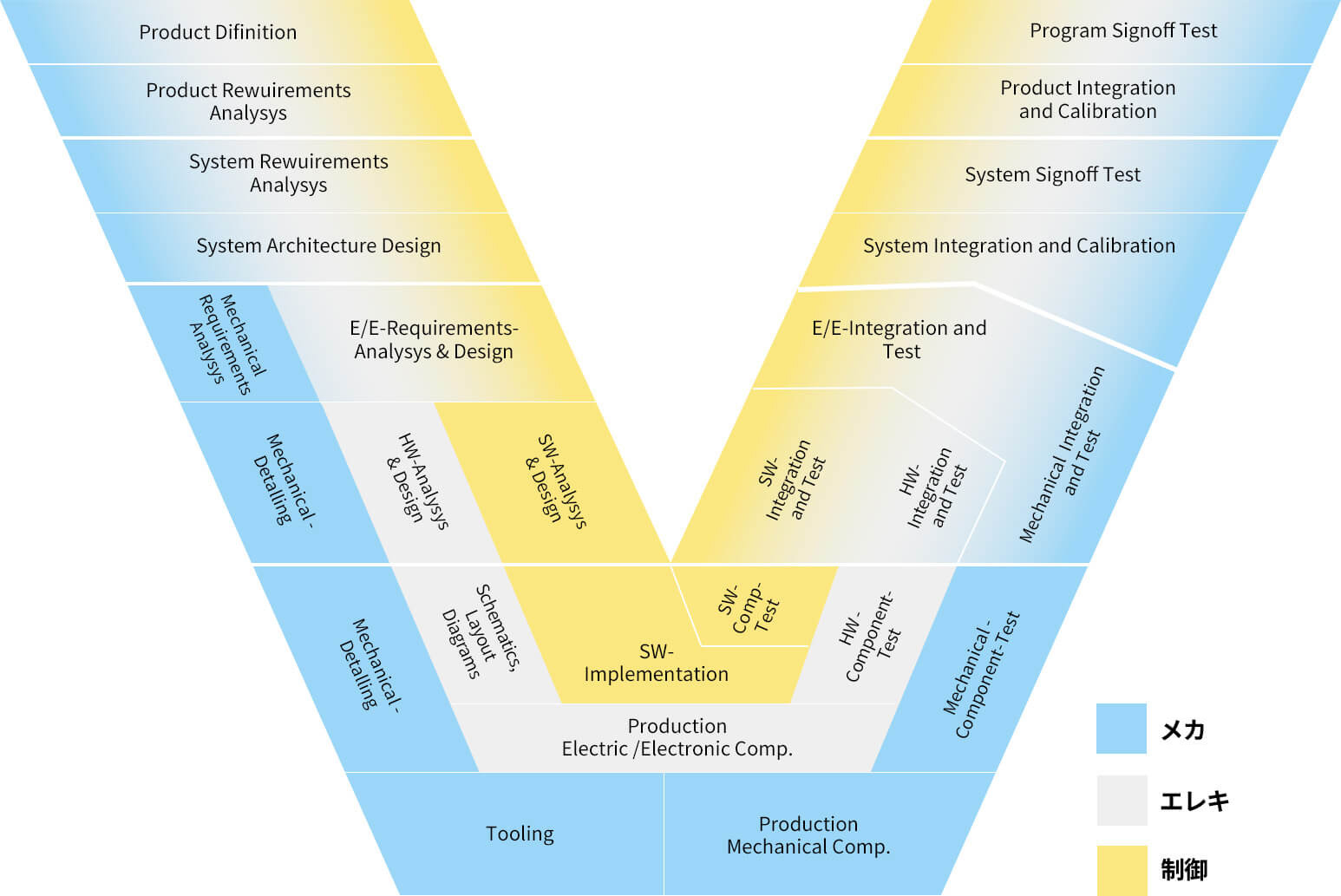
-
製品レベル
市場要求を分析し、製品のコンセプトを決定
-
システムレベル
製品コンセプトに基づいて要求を分析し、それを実現するためのシステムのアーキテクチャを設計
-
サブシステムレベル
メカ・エレキ・制御の各サブシステムへ目標を割り付け、各コンポーネントの必要スペックを決定
-
コンポーネントレベル
各コンポーネントの必要スペックを達成するための設計を検討
- 設計の上流工程において早期にシステムの成立性を検証できる
- 上位のシステム要求から各コンポーネントの目標を根拠を持って定めることができる
- 各設計ドメイン間で認識を共有しながら設計を進めることができる
expectation
MBD・MBSEに期待されること
これは、従来CAEに期待されていた試作や実験回数の削減によるコスト、工数の圧縮という狭い領域に限定されるものではありません。
設計フェーズ・開発ドメイン間で認識を共有しながら設計を進めることで、パッチ当ての設計から脱却して本質に基づく設計を実現し、設計品質や製品性能を極限まで向上させ、競争力を維持することが可能となります。
また、従来の設計においては暗黙知とされてきた熟練技術者のカンコツを含めた技能を見える化し、人材育成や技術伝承といった設計開発現場における喫緊の課題解決に役立てる手法としても注目されています。
さらに、これらの活動を通して生まれた余剰リソースの再配分と蓄積されたナレッジの利活用によって、事業環境や顧客ニーズの変化に対する対応力を強化し、さらなるイノベーションに繋げることこそがMBDの究極の目的と言えるでしょう。
- 設計フェーズ/開発ドメイン間の認識の共有
- コンカレントエンジニアリングの実現による開発期間の短縮
- パッチあて設計から脱却し本質に基づく設計
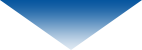
削減
向上
業務品質の改善
向上
技術伝承
事業環境や顧客ニーズの変化に対する対応力強化
compatibility
相性のよい開発領域や業界
-
車
-
建機
-
船
-
プラント
-
トラック
-
飛行機・ドローン
-
機械
-
ロケット
-
電気
-
熱
problem
MBD・MBSEを進める上での課題
- 機能ばらしやSysMLツールを導入してみたが、どう設計に活用して良いかわからない。
- 1D CAE用いた機械設計やシステム設計を開発プロセスに浸透させることができない。
- 機能設計と形状設計のプロセスが分断されてしまっている。
- 設計業務でCAEや最適化技術を定着させることができていない。
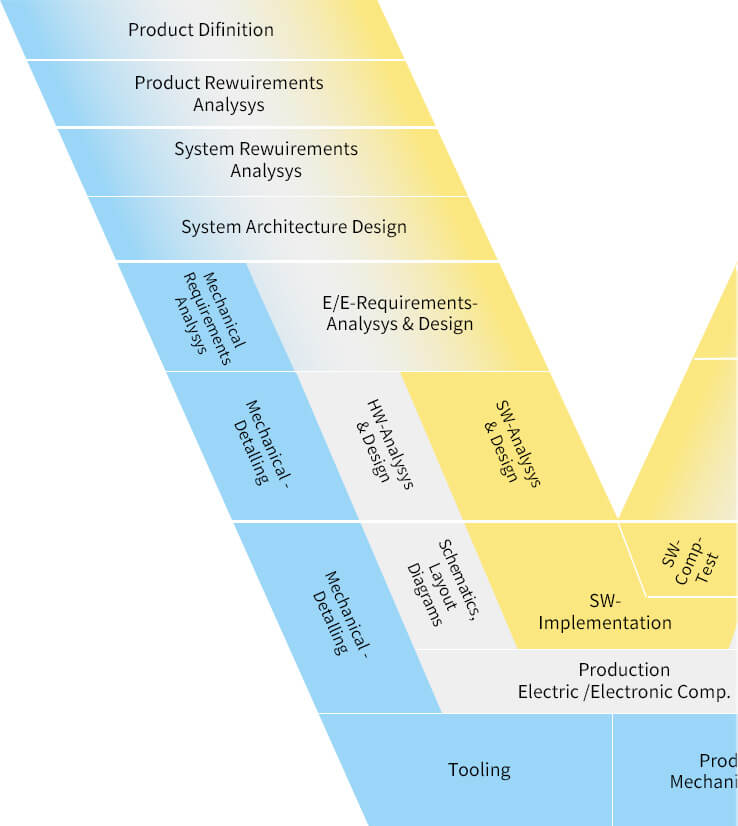
service features
IDAJのMBDサービスの特徴
設計開発に根付いたMBD・MBSEプロセスの構築
- MBSEを目的とするのではなく、「MBDを実践するための手段」として活用し、モデルに求められる要件やアーキテクチャを明確化
- IDAJが保有する各物理領域における解析技術に基づき、具体的な「モデル構築の手順まで見据えた推進計画」を立案
- 「最後まで走り切る」ための体制づくりとプロジェクトマネージメントを支援
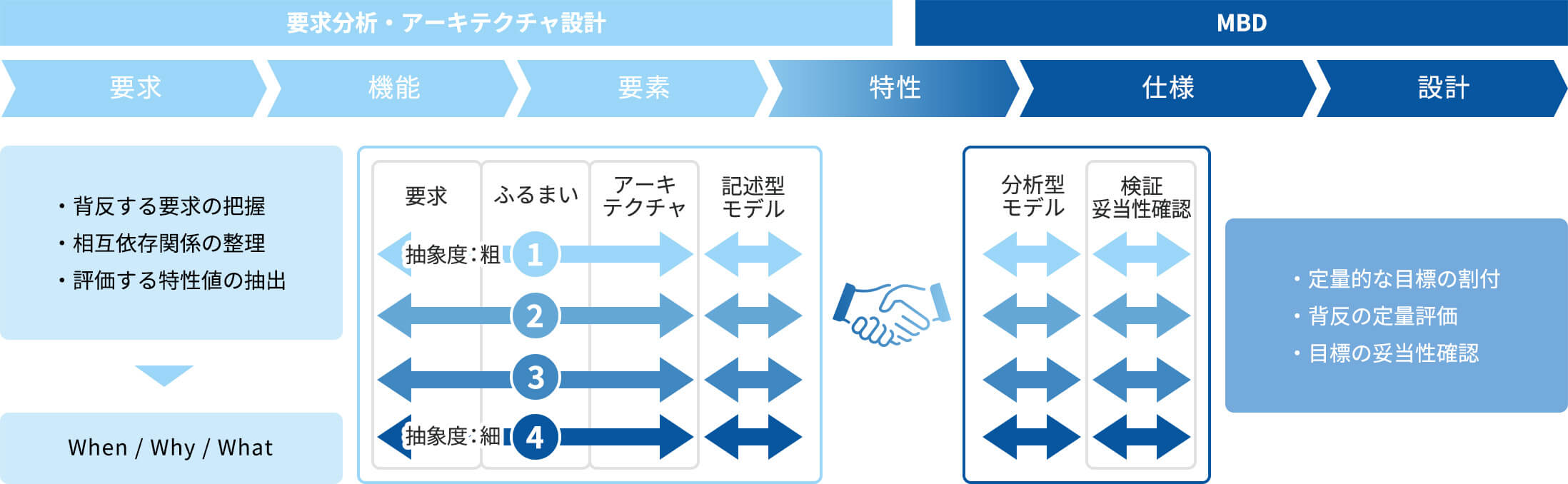
MBD・CAE領域における圧倒的な実績
- 1次元(1D)・3次元(3D)CAEおよび「各物理領域を網羅した」シミュレーション技術の提供
- 「年間700件、累計8,000件」に及ぶ豊富なCAEコンサルティング実績
- 各種トレーニング、充実したサポート、技術者派遣による「早期の技術立ち上げの実現」
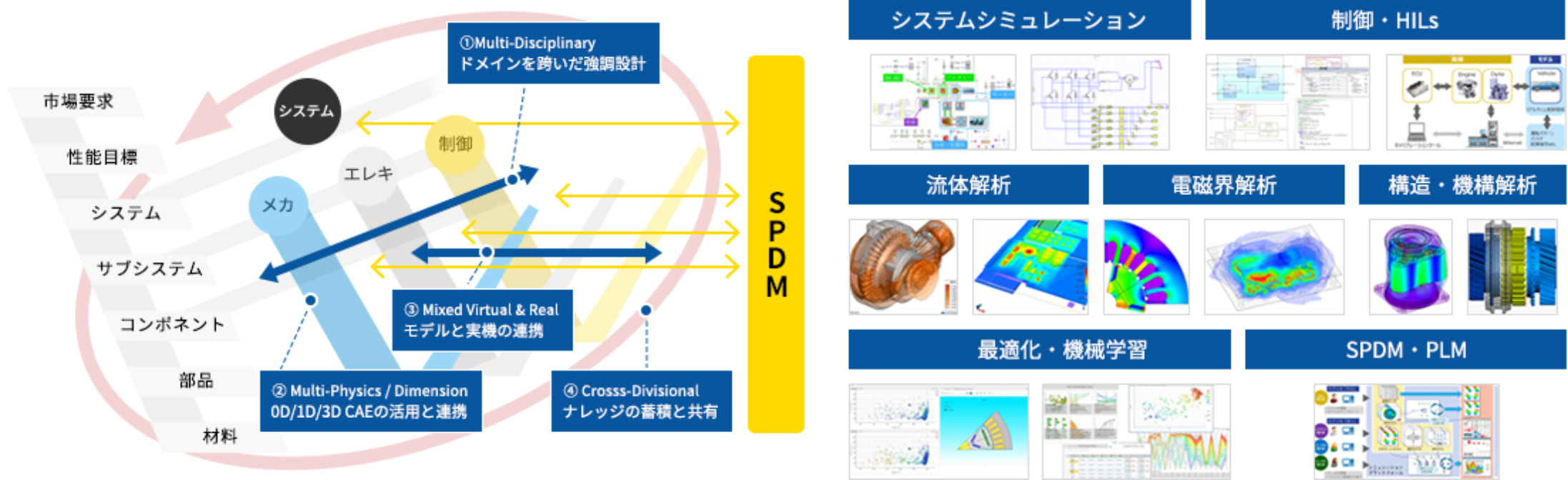
case study
ケーススタディ
flow
ご相談の流れ
-
STEP
01
初回アポ仮のTo-Be像に対し、まずどこから手をつけるのか、コンサルティングの実施テーマ、ボリューム、粒度、ゴールを決定します。 -
STEP
02
お客様のご課題の共有貴社における現状の設計プロセス、MBDのお取り組み状況や課題、ありたき姿などを可能な範囲でご共有いただき、仮のTo-Be像の具体化に向けてディスカッションを行います。 -
STEP
03
ヒアリングSTEP2でご共有いただいた内容について、より詳細なヒアリングを数回に分けて実施させていただき、仮のTo-Be像を具体化して行きます。 -
STEP
04
仮のTo-Be像の共有STEP3のヒアリング内容をもとに仮のTo-Be像を描きます。 -
STEP
05
Phase-0実施方針の決定仮のTo-Be像に対し、まずどこから手をつけるのか、コンサルティングの実施テーマ、ボリューム、粒度、ゴールを決定します。 -
STEP
06
Phase-0の実施有償のコンサルティングにて現状課題分析・計画立案を実施させていただき、As-ls/To-Beの詳細を可視化するとともに実施計画を策定します。
faq
よくいただくご質問
-
MBDプロセスを導入するとシミュレーション工数が増え、かえって工数がかかると聞きますが本当ですか?
自社シミュレーション技術をお持ちでない場合は、技術構築を行う過程で一時的に工数が増えることがあります。IDAJでは、技術構築の難易度や課題の重要性に応じて、取り組むべき技術構築テーマに優先順位を付けます。これにより、試作回数や手戻りの削減効果を比較的短期間で実感いただけるテーマに取り組みつつ、自動化・最適化技術などを複合的に取り入れ、モデルの再利用、プロセス管理、右バンク工数削減などを経て中長期的に工数削減を目指します。
-
そもそもシミュレーション技術を持つ人材が少ないのですが、どうすればよいですか?
MBDプロセスを導入するにはシミュレーション技術が必須技術となります。ただし、必ずしも高価なCAEソフトウェアが必須ということではありません。IDAJは、30年以上CAEに特化した技術をあらゆる製造業のお客様にご提供してきましたので、シミュレーション未経験者に向けた無料・有料の教育メニューが多数あります。もちろんお客様のご業務に合わせた、オリジナルのメニューでのトレーニングも可能です。
-
MBDプロセスの導入をすべてお任せしたいのですが可能ですか?
あえて”NO”と回答します。もちろんご提案とスケジューリング、教育などIDAJが担うものは多数ありますが、実際に導入し、運用されるお客様の関わりを排除することはできません。むしろ、その過程と関わりが導入後の成果や成否を分けると言っても過言ではありません。「伴走」という形でご支援させていただきます。
-
過去にMBDプロセスの導入を検討・実施してみましたが、期待以上の効果が得られませんでした。
MBDプロセスの導入は目的ではなく、あくまでも貴社の競争力を上げるための手段だと考えます。要求の見える化、機能の分解といったアプローチは、性能設計に活かされて初めて効果が得られます。しかし設計上流段階の負荷が増大するアプローチでもありますので、全体を俯瞰して課題と必要性を検討すべきです。IDAJではあるべき姿を貴社と一緒にデザインし、方法論の一つとして適切なMBDプロセスをご提案します。
-
MBDプロセスの導入のために高価なソフトウェアやシステムの導入は必須ですか?
現在では比較的安価なソフトウェアも多くありますので“NO”だと考えています。IDAJはマルチベンダーの特性を活かして、エンジニアリング視点で貴社の現状況をできるかぎりニュートラルに分析し、貴社に必要で適切な技術と環境をご提案します。
-
まずは、何から検討を始めればよいですか?
MBDプロセスやMBD開発、MBSE活用といった言葉を目にすることが増え、関連情報が多く発信されていますので混乱されることがあるかと思います。IDAJでは、しっかりとした現状分析を出発点に定め、これまで培ってきた豊富なCAE技術の視点から分析した結果を、まずは貴社と共有させていただきます。その上でコンサルティングを進めますので、まずはお気軽にIDAJまでお問い合わせいただければ幸いです。
-
NDAの締結は可能ですか?
はい、承ります。お気軽にコンサルタントにご相談ください。
contact