日揮触媒化成 様(IDAJ news vol.109)
modeFRONTIER®を活用した多目的最適化による触媒設計技術を確立
日揮触媒化成 株式会社
石油精製触媒研究所 様
IDAJ news vol.109お客様紹介コーナーより抜粋
発行日2022年9月
解析種別:内製シミュレーター連携、応答曲面、RBF、多目的最適化、多次元解析、マテリアルズインフォマティクス
課題等:触媒の最適設計、検討と試作時間の低減、設計のスリム化、限界性能の可視化
省略
カスタムメイドにも素早く対応するための触媒設計のスリム化を目指して
- 御社では、現在modeFRONTIERをご利用いただいておりますが、ご導入のきっかけを含めて、適用事例についてもご紹介ください。
- こちらの写真は、FCC触媒のサンプルで、サイズは50~100ミクロン程度です。この触媒一粒一粒に対して、流動性、耐摩耗性、耐水熱安定性、かさ密度などの物性と、高分解活性、高ガソリン収率、低ボトム収率、低コーク収率、耐メタル性などの性能が要求されます。また触媒は、それ自体が想定した組成であるかどうかだけでなく、装置や原料油、反応条件など、お客様によって異なる条件下で、期待する性能が発揮されるかどうかが重要です。つまり、お客様のご要望に応じて、様々な触媒の原料を配合して、カスタムメイドで製造しているわけです。
- 触媒はカスタムメイドなんですね?!また、お客様の装置で実際にご利用いただくまで、性能がわからないとは・・・存じ上げませんでした。
- はい、そうなんです。FCC触媒を製造するには、お客様の要求に応じて、ゼオライト、活性アルミナ、カオリン、バインダー、添加剤などの原料の配合比を調整して混合、その後、造粒・洗浄・乾燥の各工程を経て製造しています。お客様の装置で使用して性能が出るか否かを確認するには、出荷前にお客様が使用される油や装置の条件を用いて、弊社で同じ条件で反応させ、その結果を確認します。これを、当たり前のように長年続けてきたわけですが、この工程を仮想実験で置き換える方法がないかと検討し始めたのが2014年頃です。
出荷前の確認作業は、石油精製装置の10万分の1程度の規模で行います。実は、これでもかなり大がかりな装置を使用した作業になりますので、まずは社内で性能予測シミュレーターを作成しました。このシミュレーターのパラメータを最適化すれば良いのではないかと考えたわけです。しかし原料油の組成は非常に複雑で、正確な分子構造の特定が難しい、水熱劣化度合や金属堆積量といった使用環境が大幅に変動する、触媒ごとに温度依存項や被毒項が必要になるなど、最適化プログラムを作成するのも難しいかなと躊躇していました。そんな時に、IDAJさんからmodeFRONTIERを紹介していただき、内製のシミュレーターと連携させた最適化に取り組み始めました。触媒の組成、物性、活性など、かなりのデータ蓄積がありましたので、それに対して、圧力、温度、接触時間といった運転条件や原料油種というお客様が触媒を使用される条件を用いて、最適な触媒の組成をシミュレーションすることを目指しました。
内製のシミュレーターは、反応速度論がベースになっています。したがって、反応温度を450℃から500℃へ上げるとどうなるかはシミュレーターで簡単に算出できます。しかし、触媒の表面積を2倍にするとか細孔容積を大きくした反応結果を計算で求めることはできません。良くなるだろうというのはわかりますが、触媒物性のみで化学反応を定量的に予測することはできません。
従来の開発では、分解活性を上げたい、ガソリンの収率を上げたいといったお客様の要求に対して、まず複数のエンジニアが集まって、過去の知見をもとにゼオライトの含有量を増やす、添加剤を配合するなど目的に沿った組成を検討します。組成検討が終わると、次に、いくつかの組み合わせ候補を実験室で試作します。そして、試作触媒を評価解析し、それが開発目標や要求目標を満たしているかどうかをチェックし、ダメならまた組成の組み合わせを変更する検討に戻る。このフローを、各目標をクリアするまで繰り返していたのです。

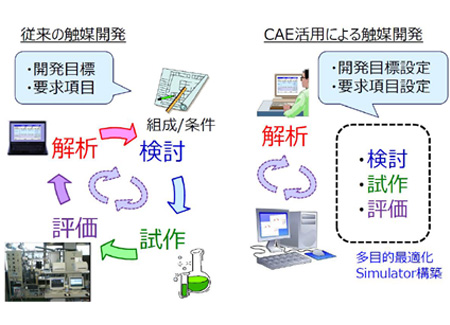
1ケースあたり5~6名で2~3週間かかる設計検討を、1名で0.5~1時間に短縮
- 触媒組成の最適化にあたって、まずは、触媒設計のためのパラメータ整理から始めました。FCC触媒は、触媒のかさ密度、対摩耗性、装置内での流動性といった物性が要求されます。また、ゼオライト、アルミナ、カオリン、バインダー、添加剤などの材料や調整条件などがあります。もちろん、一口にゼオライトと言っても、多くの種類がありますから、その中から、性能要求を満たし、コストを抑えることができる材料を選択しなければなりません。最終的には、ガソリン収率最大化、ドライガス収率、未分解油(註:ボトム)収率、コーク収率の最小化などの反応成績で評価します。
- 準備した1,000件の実験データの8割を応答曲面作成用、残りの2割を精度検証用として、様々なアルゴリズムで応答曲面を作成し、各アルゴリズムの精度を検証しました。その結果、RBF(註:動径基底関数)の精度が最も高いことが確認できましたので、これを使って、1,000件の実験データから応答曲面を再度作成し、さらに20件の追加実験データと比較しました。この検証の結果から、シミュレーションによる設計が可能だと判断しました。
- 続いてターゲットとする条件で、最適なパフォーマンスを示す触媒設計のために、5,000件の多目的最適化を実施しました。
こちらは、デザイン選定のために作成した多次元解析チャートです。仮想実験の結果から、ボトム収率が減少すると、ガソリン・コーク・ドライガスの収率が増加する、つまりボトム収率の低減と、コーク・ドライガス収率の低減がトレードオフ関係にあることがわかりました。ボトム収率が高いほど活性の高い触媒となり、転化率が上がります。しかし、ガソリン収率を上げたい場合は、転化率が高くても、ドライガスに過分解しては困ります。
この事例では、多次元解析で絞り込んだ結果から、触媒の組成を確認してより良い触媒組成を選択しましたが、このような複雑な触媒組成を、人間が微調整することは非常に困難であることがご理解いただけるかと思います。 - 最適化結果を検証したところ、従来の設計で、ボトムを極力減らし、ガソリン収率を最大化、コークとドライガスを最小化するという人間が設計した結果よりも、modeFRONTIERで解いた組成の方がガソリン収率が高くコーク収率が低いことが明らかになりました。
- お客様の中には、データがあっても数が少ない、あるいはデータが偏っていることがあるのですが、本ケースでは1,000件もの既存実験データがあり、また設計空間にまんべんなくデータをお持ちでしたので、結果として精度が良好な応答曲面が作成でき、データを有効にご活用いただくことができました。 このCAEを活用した触媒開発によって、どのような効果がございましたでしょうか?
- 開発目標や要求項目を数名がかりで解析し、組成や運転条件を検討、それを元に試作して、試作した触媒を評価するというサイクルを1回まわすのに、延べ人数5~6名で2~3週間かかっていましたので、お客様にご提案するまでに、検討できるケースはそう多くはありませんでした。一方、CAEを活用し多目的最適化シミュレーターを構築した現在は、一人で開発目標と要求項目を設定し、解析することができますし、1ケースあたりの計算時間も30分~1時間程度しかかかりませんので、時間、工数ともかなりの効率化に成功しています。また、トレードオフをピンポイントで見極めて、その周辺の解を探索するため無駄な計算がないのも大きなメリットです。
従来の手法では、経験に頼る部分が多く、最適か否かを判断するにも時間がかかっていましたが、開発目標や要求項目を設定すれば、どんな組成の触媒がふさわしいか、その触媒を使えばどれほどの転化率が得られるのかといったことが客観的なデータで示されますので、製品の質を低下させることなく、設計をスリム化することができました。また、限界性能が可視化できましたので、以前に比べると、お客様ごとにカスタマイズするための試験もずいぶん減りましたね。
効率化によっていわゆるルーチンワークから解放され、検討や試作、試験などに割いていた工数を、新しい材料を作るという研究開発に注力するための工数にシフトすることができることも、数値化はできませんが大きな効果だと感じています。
2014年という段階でmodeFRONTIERに出会い、“データ”があれば最適化技術だけでなく、新しい技術の効率的な開発ができそうだということに気づくことができました。これも広い意味で成果と言えるのではないかと思います。
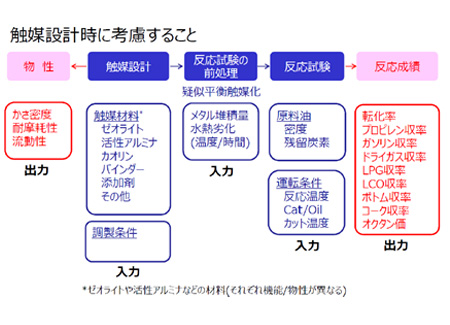
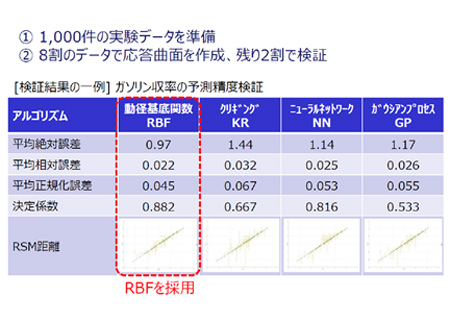
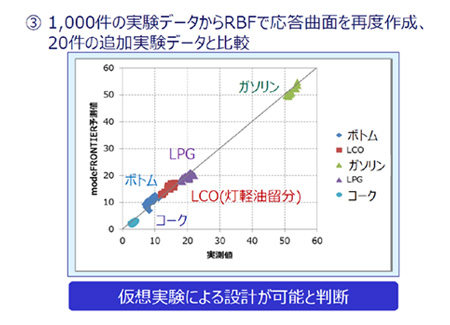
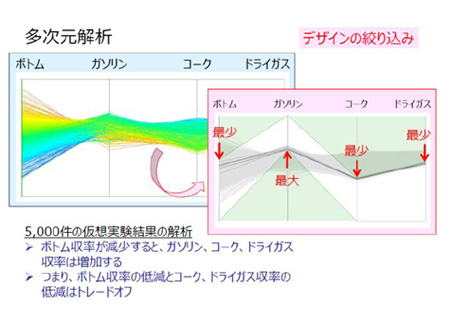
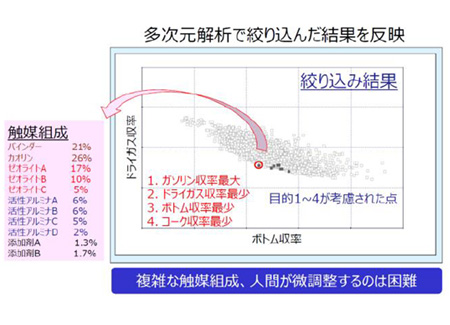

社内に点在するデータを集約しマテリアルズ・インフォマティクスの活用を推進中
- modeFRONTIERによる最適化フローを新たなルーチンワークとして御社の業務フローに組み込んでいただき、成果も上がっているとお聞きして非常に嬉しく存じます。“データが多くあればあとは分析するだけだから、modeFRONTIERは不要だ”と言われることもあるのですが、今回のケースのように複雑なトレードオフが存在する場合は、人間が調整するには限界があるのではないかと思います。その点で、最適化技術をうまくご活用いただいた好例だと考えております。
さて、こちらの最適化技術は、2019年の弊社カンファレンスでもご紹介いただきましたが、その後のご状況について開示可能な範囲でご説明いただけますか? - 私どもが構築した応答曲面を活用して評価結果を最適化する技術のほかに、複数の部署でもこの自動化・最適化技術が広がっています。よりお客様に近い部門では、熱バランスや圧力バランス、原料油、反応条件などの必要な情報を使って実装置の性能を予測する市販シミュレーターを使っていますが、それとmodeFRONTIERを連成させて作業を自動化しています。この作業も、運転条件を変える、温度を変える、触媒の循環量を変えるといった試行錯誤しながら行っていましたが、自動化によって条件さえ与えれば最適解が得られるため作業の効率化に貢献しています。
データの重要性をことのほか強く意識したことで、開発効率化を目的としたマテリアルズ・インフォマティクスの活用も順調に進んでいます。モノづくりDX推進にあたって欠かせないのがデータ収集であることは皆様ご承知のことと思います。弊社が今回ご紹介した最適化技術について学会等で発表すると決まって「データをどうやって集めたのですか?」というご質問を受けます。弊社の場合は、従前の業務フローの中で多くのデータを収集しており、データそのものが弊社のノウハウであると言っても過言ではない状況にはありました。したがって“データ”には困りませんでしたが、それらを“収集・集約・整理”して“誰もが使えるようにする”というフェーズではかなり苦労しました。
現在はこの蓄積したデータからシミュレーションモデルを構築し、仮想実験による材料種・量の最適化を計算で求め、触媒物性などの制約を加味した最適化によって触媒設計を行えるようになりました。また、石油精製ではLPGやガソリン収率の最適化だけでなく、LPG中のプロピレン収率やガソリン中のBTX収率に着目する技術の深耕に取り組むとともに、ケミカル触媒、環境保全触媒などへの展開や生産設備の運転条件最適化への活用も開始しています。
2014年の導入からチームが成果を上げてくれたおかげで、弊社の経営層にも理解が浸透していることが、他部署への広がりを促進していると考えています。
省略
このインタビューの詳細は季刊情報誌IDAJ news vol.109でご覧いただけます。
ユーザー登録済の方はユーザーサポートセンターからダウンロードできます。
ご活用いただいている製品
- 分野1:
- 化学反応解析
- 分野2:
- 最適設計