オムロン 様(IDAJ news vol.114)
modeFRONTIER®を用いた機械学習による最適化設計プロセスの実証
オムロン株式会社
技術・知財本部 様
IDAJ news vol.114お客様紹介コーナーより抜粋
発行日2023年12月
課題等:機械化、自動化、ロボティックス、センシング、パワーエレクトロニクス、AI・データ解析、設計の高効率化、電気回路最適化、回路パラメーター最適化、パワエレ、磁気特性、回路特性
省略
最適化技術が"設計現場で人と機械を融和"
- 御社の設計開発プロセスにおけるデジタル技術や最適化などのご活用状況について簡単にお聞かせください。
- 弊社ではデジタル技術の1つにCAEが位置づけられています。またCAEは、シミュレーション・最適化・データ解析の3要素で構成されると定義しています。これらを設計に活用することで、2つの価値創出を狙います。
1つ目は開発生産性の向上、2つ目は製品価値の向上です。開発生産性の向上では、設計における手戻りの防止を目指します。具体的には、手戻りの影響が大きかったパワエレを端緒としてコントローラやコンポ商品など、広く設計現場での活用が進んできています。例えば商品開発では熱が大きな課題の1つとなりますが、設計の後半で熱問題が発覚すると筐体そのものをつくりなおすことにもなりかねません。CAEの中でもシミュレーションの活用が、熱起因の手戻り撲滅に大きく貢献しています。
2つ目の製品価値の向上は、シミュレーションに加えて、最適化とデータ解析でCAEをフル活用することで実現できると考えています。最適化技術は現在、パワエレ分野や電子部品開発などで主に活用しています。先ほど創業90周年を迎えたと申しましたが、かつての日本の製造業各社がそうであったように、オムロンでも、その前身である立石電機の時代から脈々と優秀な職人の技術が設計開発、製造を支えてきました。ただ、人間の勘・コツ・経験に依存した従来の設計手法では困難な水準に技術難易度が上昇しており、かつ商品ライフサイクルの短期間化が求められています。それを解決する手段として最適化技術に期待をしています。また、先述の創業者の経営理念を設計現場で捉えると、最適化技術によって試行錯誤を繰り返す工程は「機械にできることは機械に任せ」に変換することができます。これによって設計手法が変わるだけでなく、設計者の役割も「創造的な分野」へと変化するのではないかと思います。具体的には、設計者の暗黙知だった部分を定式化し、製造性を制約条件として問題設計をする、最適化で導出された解の物理的な意味を解釈して設計指針へ落とし込む、さらに抽象化してよりよい問題設計や新規アイディアに繋げるといった内容に比重が大きくなります。
もちろんこれから適用領域の拡大を検討していきます。オムロンのコーポレートR&D部門である技術・知財本部で開発する技術は先行開発の位置づけで、社会課題を起点とした長期的な取り組みを実施します。それに加えて、事業部門で発生したニーズも、新規性があるテーマや、部門横断的な共通課題である場合は、各部門とコミュニケーションをとりながら進めています。 - ありがとうございます。それでは早速ですが、機械学習を用いた電力変換機器の最適化設計プロセス実証についてご紹介ください。
- 私が担当するのはCAEの構成要素である最適化技術開発とその設計応用です。そこで、パワエレ分野で構築した最適化技術の一つをご紹介します。
まず、パワエレでの最適化の必要性からご説明します。パワエレは、今や私たちの生活において欠かせないものです。いわゆる電源と言われるもので、ご家庭ではパワーコンディショナ、工場では汎用電源などがあります。昨今、そのパワエレには、エネルギー問題に関連して低損失であることや、製品の小型化・ローコストが求められ、そのために電気やメカ、熱、ノイズなどの技術的実現性を融合させる必要があり、要求事項が複雑化しています。これら要求を満足するエリアは非常に狭く、設計難易度が高くなっていますので、設計期間が長期化する傾向があり、最適化技術を導入することで設計の高効率化を目指しました。 - 近年、最適化技術が様々な業界で活用されはじめていることを実感しています。その最大の理由は、コスト面と技術面での導入ハードルが下がってきていることだと考えています。以前は、最適化の専門家が内製したソフトを使ってスパコンなどのハイスペックな環境で計算していましたが、最近は異分野の専門家が、modeFRONTIERをはじめとする商用のソフトウェアとワークステーションを使って実行できる状況になり、最適化の適用範囲が広がってきました。もともとは自動車や航空機、建築といった部品点数が多く、1回あたりの試作が大規模な産業が、最適化が使われてきたフィールドでしたが、導入ハードルが下がることによって、コストパフォーマンスが得られる領域が拡大、すなわち中規模試作のフィールドでも使われるようになってきました。まさにパワエレが今、この段階にあるのではないかと思っています。その状況は、論文の数でも明らかです。試しに、「パワエレ」・「最適化」をキーワードとして、10年前の論文数と2019年の論文数を比較すると3倍以上になっており、回路の最適化、ヒートシンクの形状最適化、ノイズの最適化といった多岐にわたった内容が研究されています。
弊社の製品で中規模試作に相当するパワエレ領域において、最適化技術を導入することで設計の高効率化を目指しました。一般的なパワエレの設計プロセスでは、まず電気回路として理想的な観点から回路定数を決めた後、各部品に対してそれらの特性値を満足する詳細な設計値を導出します。最後にそれらの部品を統合して、望ましい部品の配置を検討します。この場合、大きく3回の試行錯誤が発生し、検討期間が長期化する要因となっていました。
そこで、これら3つの工程を最適化問題として置き換えていきます。すなわち、1つ目に回路パラメータの最適化、2つ目に部品寸法の最適化、最後が部品配置の最適化とし、この3つの最適化問題を組み合わせて、一連の設計プロセスとします。これにより試行錯誤の自動化を実現し、検討期間が短縮されます。また設計者自身も別の業務に工数を割くことが可能になります。 - 理想的には、要求仕様を入れると3つの設計プロセスが順番に実行され、製品案まで一気通貫に自動的に導出されることですが、これには大きな課題があります。それは、個別最適の組み合わせが必ずしも全体最適とはならないことです。ご経験ある方も多いと思いますが、熟練の設計者は回路の設計をするときに、製品はこの全体サイズなら各部品はおよそこれくらいで・・・と最終的な製品をイメージし、暗黙のうちに異なる事項を擦り合わせながら設計しています。しかし最適化問題の場合、定義した範囲内でしか検討できませんので全体最適のためには、最適化問題を融合したプロセスを考える必要があります。そこで、まずは1ステップ目の電気回路の最適化と2ステップ目の部品寸法の最適化の同時化に取り組みました。
- 1つ目と2つ目のステップがもともと独立した最適化問題であった場合は、プロセスがループしてしまい、かえって非効率になってしまいました。その理由は、回路パラメータの最適化を実行する際の設計空間が、必ずしも製造可能な範囲で設定できていないからです。"おそらくこれくらいの部品特性値が取れるだろう"と想定して設計空間を決め、回路最適化をまず実施します。その結果、各部品に対して求められる特性値が出てきますので、それを実現する部品寸法を求めます。この場合、残念ながら製造制約といった都合により、要求された特性値から大きく乖離することがあります。製造業の方にはご理解いただけるかと思うのですが・・・。そうなると、再度1つ目の探索の設計空間を予想される範囲内で再設定して、2つ目を再実行・・・と満足するまでループしてしまい非効率です。そこで、回路定数最適化と部品寸法最適化を同時化する、つまり部品の製造性を考慮した回路パラメータの最適化を提案します。
ここで重要なコンセプトは、探索範囲を限定することです。各ステップを個別に最適化する際に経験則から設定した探索範囲には、製造可能な領域と、実は製造できない領域が含まれています。この新たに検討したプロセスでは、製造可能な範囲に限定することで、プロセスのループを抑えることが狙いです。
提案プロセスは技術要素に分解すると、実現性から3点と実行時間面から1点の計4つポイントがあります。実現性の1点目は、回路定数最適化と部品寸法最適化を融合させるフローチャート、2つ目は汎用ソフトウェア等との組み合わせによって自動実行する解析環境、3つ目は最適化問題への定式化です。実行時間の観点では、回路定数最適化と部品寸法最適化の同時化による計算時間の増加を抑制するために、シミュレーションを代理モデルに置き換え最適化の実行時間を短縮する必要があります。このプロセスをパワエレのアプリケーションの一つであるワイヤレス給電(注:Wireless Power Transfer、以下 WPT)の設計事例を通じて実証しました。
まずWPTについて簡単にご説明しておきます。WPTは、ケーブルなどを介さずに非接触で電力を授受し、送電ユニットと受電ユニットで構成される電源装置です。現段階の日常生活ではスマートフォンのWPTが身近な事例だと思いますが、オムロンでは、将来的に電気自転車やAMR(注:Autonomous Mobile Robot、自律走行搬送ロボット)、AGV(注:Automatic Guided Vehicle、無人搬送車)などに使用されるWPTの製品を想定しています。
パワエレの一種であるWPTには、パワエレの共通事項として求められることと、アプリケーション特有で求められることの2つがあります。前者はエネルギー問題の側面から低損失であること、ポータビリティや積載性の面から小型であること、そして当然ですがローコストであることです。後者はユーザーの利便性向上のため電力伝送空間の広さが製品価値となります。WPT特有の価値を向上させるため、設計技術の観点でとらえると、電気回路と磁気部品の設計が重要です。WPTは、共振現象を活用して電力授受を行うため、磁気部品の特性値が電気回路に与える影響が大きく、かつ磁気部品の設計自由度が高いため、回路と磁気の協調設計が必須です。そこで最適化を適用することによって設計の高効率化を図ります。 - 回路設計における入力変数には、スイッチング周波数、コンデンサなどの回路として独立した変数と、インダクタンス値などの磁気部品の形状に依存する磁気特性があります。一方で磁気設計における変数には、入力が各種部品の寸法、出力には磁気特性があります。両者は磁気特性を共有していますので、独立して設計することはできません。
- さらにWPTでは、磁気部品の磁気特性の予測が困難であるという理由から、磁気設計が難しいという課題があります。その理由は、送受電ユニットの位置関係が変わるからです。送受電ユニットが正面から向かい合っている状態と、ずれた状態では、磁気特性(注:相互インダクタンス)が変化します。この場合、1セットの部品寸法から複数の位置関係における磁気特性を予測する必要が生じ、経験則から探索範囲の予測を立てることが難しくなります。言い換えると、製造可能な範囲も狭まりますので、プロセスがループする可能性が高まります。そこで事前に、部品寸法から製造可能な範囲の磁気特性を導出し、導出された範囲内で回路パラメータの探索を行うのが提案プロセスのコンセプトです。
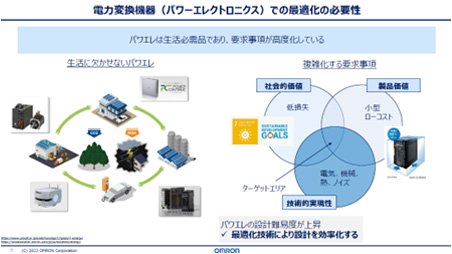
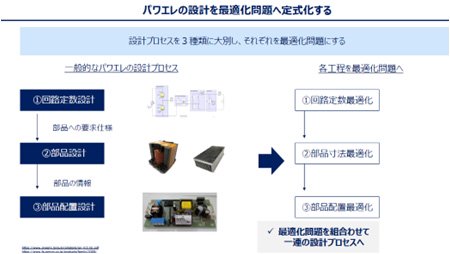
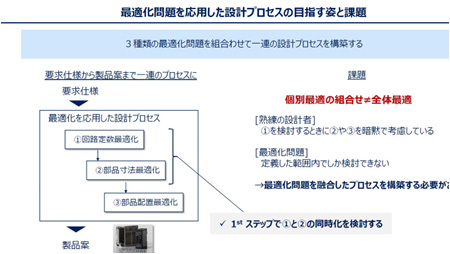
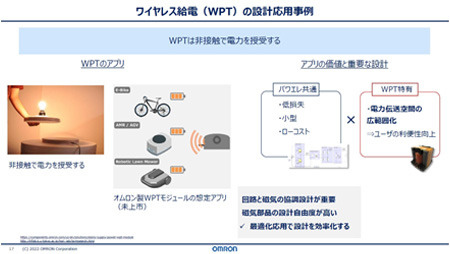
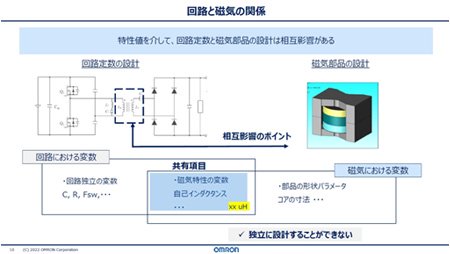
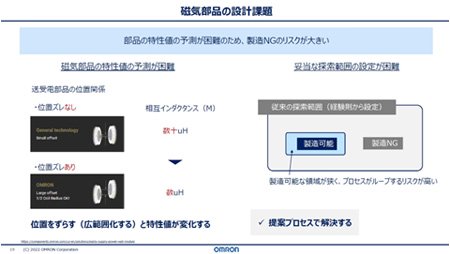
計算時間が課題であった一気通貫の最適化プロセスに代理モデルを適用
- 入力変数は、磁気部品の寸法(図7 X)と独立した回路パラメータ(図7 Y)です。電磁界解析ソフトウェアのJMAG等を使って部品寸法から磁気特性に変換する(図7 X’)と、全て回路パラメータが揃いますので、これらX’とYを用いて、回路シミュレーションから回路特性を導出します。その後、評価値を計算し、modeFRONTIERの最適化アルゴリズムを使って変数を更新します。この計算を繰り返すことによって良好な解が得られ、さらにそれを実現するための部品の寸法が同時に求まります。これが提案プロセスのポイントです。
ただしこのプロセスには一つ問題があります。それは磁気と回路の2つの解析を行うため、最適化の実行時間が長いということです。そこで、磁気特性の導出のためのシミュレーションを、代理モデルを使うことで実行時間の高速化を目指しました。代理モデルを使えば、解析時間はほぼ"0(ゼロ)"。1デザインあたり2分かかっていたとして、最適化計算のために10,000デザイン程度の計算を実行していたとすると、13日という大幅な時間短縮につながります。 - 代理モデルは、機械学習の3層MLPを使って作成しました。モデルの入力はコイルやコアなどの部品寸法、出力は自己インダクタンスや相互インダクタンスといった磁気特性です。教師あり学習になりますので、教師データの作成には、事前に磁気解析シミュレーションを実施し、モデルの学習と精度検証にはmodeFRONTIERを使いました。ユーザーとして便利だなと思うのは、学習したモデルを応答局面ノードとしてそのままワークフローに挿入できることです。
図9の結果から作成した学習モデルの予測精度は、非常に高いことが確認できていましたので、シミュレーションの代理として置き換え、高速化を実現しました。 - 最適化問題は、入力変数は独立の回路定数と磁気部品の寸法、目的関数は回路効率を最大化、制約条件は電気仕様、部品定格、ZVS(注:Zero Voltage Switching)などの回路特性を満足させることで定式化しました。図10は、解探索の結果です。今回の最適化で評価値が高くなるのは、回路効率が高く、かつ制約条件を満足したデザインです。グラフは、縦軸が評価値で横軸が計算回数、コンターは制約条件の充足度を示しており、青いほど不満足、赤くなるほど満足を意味しています。評価値が最大の単目的最適化ですので、右上に行くほど望ましいということになります。探索初期では制約不満足の青い解が多いのですが、探索の後半になるにつれて制約満足の赤い解が導出されています。このことから、解探索が期待通りに進み、適正解を導出できた、つまり最適化問題として正しく解を導出できたことがわかります。
繰り返しになりますが、このとき回路効率が高いだけではなく同時に特性を満足させる部品寸法も求まっていますので、実機試作から性能を確認しました。その結果、プロセスから導出された部品寸法で実機を試作することができ、提案プロセスで見積もられていた内容と同等の回路特性と磁気特性が出ることも確認することができました。
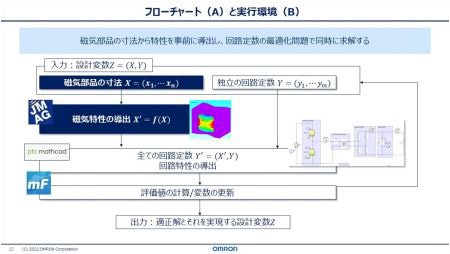
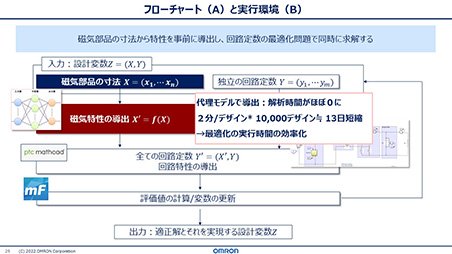
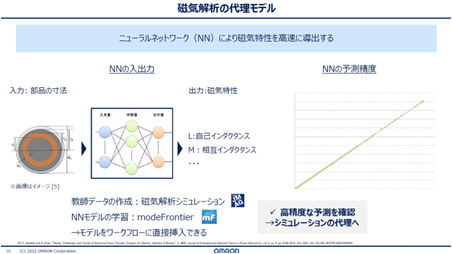
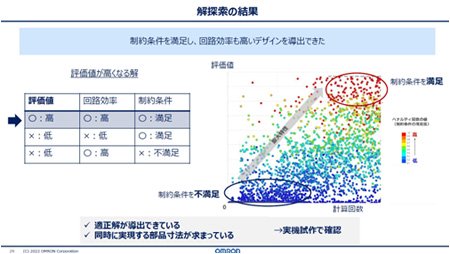
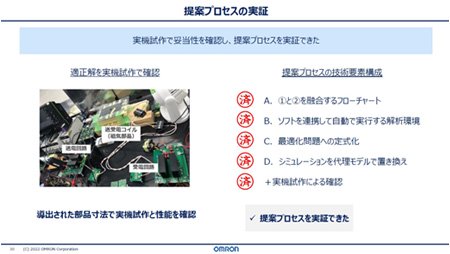
実証レベルで、最適化技術導入後の生産性向上は75%を実現
- 図12は提案プロセスによる生産性向上の効果を試算したものです。最適化技術導入前は、設計して試作・評価することを繰り返すことで徐々にすり合わせていましたが、最適化技術導入により、すり合わせをシミュレーションで行うことができましたので、試作回数が減りました。ただしこの段階では、最適化自体を何度か繰り返している状態です。そこで、回路定数最適化と部品寸法最適化を同時化することで最適化の実行回数を1回に減らすことができました。さらに、代理モデルを用いることで最適化の実行時間を削減できましたので、最適化技術導入前に比べると、75%という非常に高い生産性の向上を実現することができました。
WPTの設計に携わっているメンバーは、この結果を見てとても驚いており、ぜひ今後も積極的にこのプロセスを使っていくとともに発展させていきたいと考えています。
今回は教師あり学習を使ったため、数千個程度のデータを事前に準備する必要があり、データの収集コストがかなりかかりました。データ収集も含めて全体で見ると時間短縮に繋がりましたが、今後は収集コストの削減が技術課題だと捉えています。また今回の提案プロセスで、回路定数最適化と部品寸法最適化の同時化は実現できましたので、部品配置最適化の実現方法と、それを含んだ一連のプロセスの技術開発を引き続き検討していきたいと考えています。 - ご説明したこの最適化プロセスはさらに進化しており、複雑なプロセスが構築できつつあります。今後、パワエレだけでなく別の用途にも広げていくことをイメージしており、継続した取り組みを進めていきます。
- 最適化技術導入のビフォー・アフターというのは、読者の皆様にとってご興味のある点だと思います。もちろん対象にもよるのですが、今回のケースでは、回路設計と磁気部品設計のループはどれくらい繰り返すことがあったのでしょうか。
- 私が磁気部品設計の観点からのみで最適化を実施していましたが、結局は形状が見つかりませんでした。回路設計側の要求値を受け取るのですが、どうしても実現することができませんでした。
- そういったご経験を踏まえて、一気通貫で最適化技術を導入しようというお考えをお持ちになったのでしょうか。また、どういったことでご苦労されましたか。
- もともと、個人的にデータサイエンスに興味があり、いつか、何らかの形で業務上携わってみたいと、漠然と思っていました。ここでご紹介したフローを思いつくことができたのは、私がやりたいと思っていたことがmodeFRONTIERで容易に実行できたことが1つの要因だと考えています。
苦労したのはデータ取りですね。当時は全く知見がなく、教師データに必要なデータ数の見当がつきませんでした。そこで、データ数はとりあえず多い方が高精度だろうと思い、学習データ数をmodeFRONTIERで上限の5000個集めました。WPT自体の入出力仕様は1つでしたが、高性能化を目指して複数の回路トポロジーで検討する可能性がありましたので、時間をかけてでもここでデータを取った方が、トータルで効率的だと判断したからです。
実は、このフローを完成させるまでには2~3年かかっています。今、ご説明したように教師データを集めるのに時間はかかりましたが、それ以前に最適化をゼロからスタートさせたので、まずフローに関するアイディアにたどり着くまでに時間を要しました。つまり"設計で実際に役に立つフロー"を考えることが最も苦労した点の一つです。フローが決まってからは、スムーズに進めることができましたね。
ともするとCAEは机上の空論になるリスクがあるので、何を目的として実施し、シミュレーションの誤差を考慮しつつ、どうすれば現実的に使えるか、これにこだわって技術開発を進めたいと思います。 - ご説明の通りで、普通なら、回路定数設計から部品設計というステップを踏むことが、シンプルでわかりやすいので、よく試されるアプローチです。ただそれだと、回路特性値は出ても、それを部品形状に落とし込むところでご苦労されることが多いようです。そのハードルを越えるために、一気通貫でフローを構築するアプローチは読者の皆様にもご参考にしていただけるのではないかと思います。
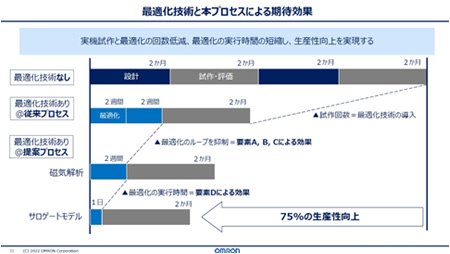
本インタビューに関連する情報が、オムロン様のWebページでもご紹介されています。
オムロンのデジタルデザイン・DX技術にせまる 後編
~ 高度なシミュレーション技術で未来社会を創る ~
省略
このインタビューの詳細は季刊情報誌IDAJ news vol.114でご覧いただけます。
ユーザー登録済の方はユーザーサポートセンターからダウンロードできます。
ご活用いただいている製品
- 分野1:
- 電磁場解析
- 分野2:
- 最適設計