CAEからMBD、そしてDXへ向けて ~new NORMを切り拓く武器としてのMBD~(1)
皆さま、こんにちは。
IDAJの玉手です。
デジタルトランスフォーメーション(Digital Transformation:DX)とは?
経済産業省の「DX推進ガイドライン」によると、“企業がビジネス環境の激しい変化に対応し、データとデジタル技術を活用して、顧客や社会のニーズをもとに、製品やサービス、ビジネスモデルを変革するとともに、業務そのものや、組織、プロセス、企業文化・風土を変革し、競争上の優位性を確立すること“とされています。
これを要約しますと、以下通りです。
目的:ビジネス環境の激しい変化に対応し、競争上の優位性を確立すること
手段:データとデジタル技術の活用によって
・顧客ニーズに基づいて製品やサービス、ビジネスモデルを変革
・業務そのものや組織、プロセス、企業文化・風土を変革
翻って、モデルベース開発やCAEとDXとの関係性はというと、もちろんデジタル技術を使うという観点では、MBDやCAEがDXの一つの手段であることは間違いありません。しかし、MBDやCAEを活用することがDXということではないと思いますし、従来のMBDやCAEとDXのどこが違うのかといった部分についてはまだまだ議論の余地があるものと考えます。
ここでは一つの切り口として「ニューノーマルでの生き残り」という観点から、どのようにMBDやCAEを活用すべきなのか、その中で弊社が考えるデジタルトランスフォーメーションの一端をご紹介します。
CAE・MBDの取り組みのふりかえり
皆さまは、すでに普段の設計業務の中でCAEをかなり活用されているかと思います。改めて、どんなことがCAEに期待されているのでしょうか?
電動トランスアクスルの設計を例にCAEやMBDがどのように使われてきたかという変遷をご説明します。
従来の開発プロセスにおいてはシステムである、e-Axle(イーアクスル)に求められる要求や性能目標をベースにモータやインバータ、あるいはギアボックスというeアクスルを構成するそれぞれのコンポーネントあるいはサブシステムに要求が下りていきます。各ドメインごとに設計を進めていくことになりますので、モータ設計者はトルクをどうするのか?冷却性能はどうするのか?振動はどうするのか?ということを考え、コンポーネント(=部品)単位に設計をおろします。そして設計が定まった後に評価するわけですが、ここで従来の試験に代わるバーチャル評価(CAE)を使ったデジタル評価によって、試作や試験にかかるコスト・工数を削減することが従来のCAEのねらいでした。仮に、プロセスの途中で問題が発生した場合には、設計に立ち戻り、設計を改めて検討した上で、もう一度バーチャル評価をすることになります。
つまり、不具合発生時の原因解明や、設計の妥当性確認といった製品開発の試験検証フェーズである右バンク側で活用するというのが従来の使われ方でした。
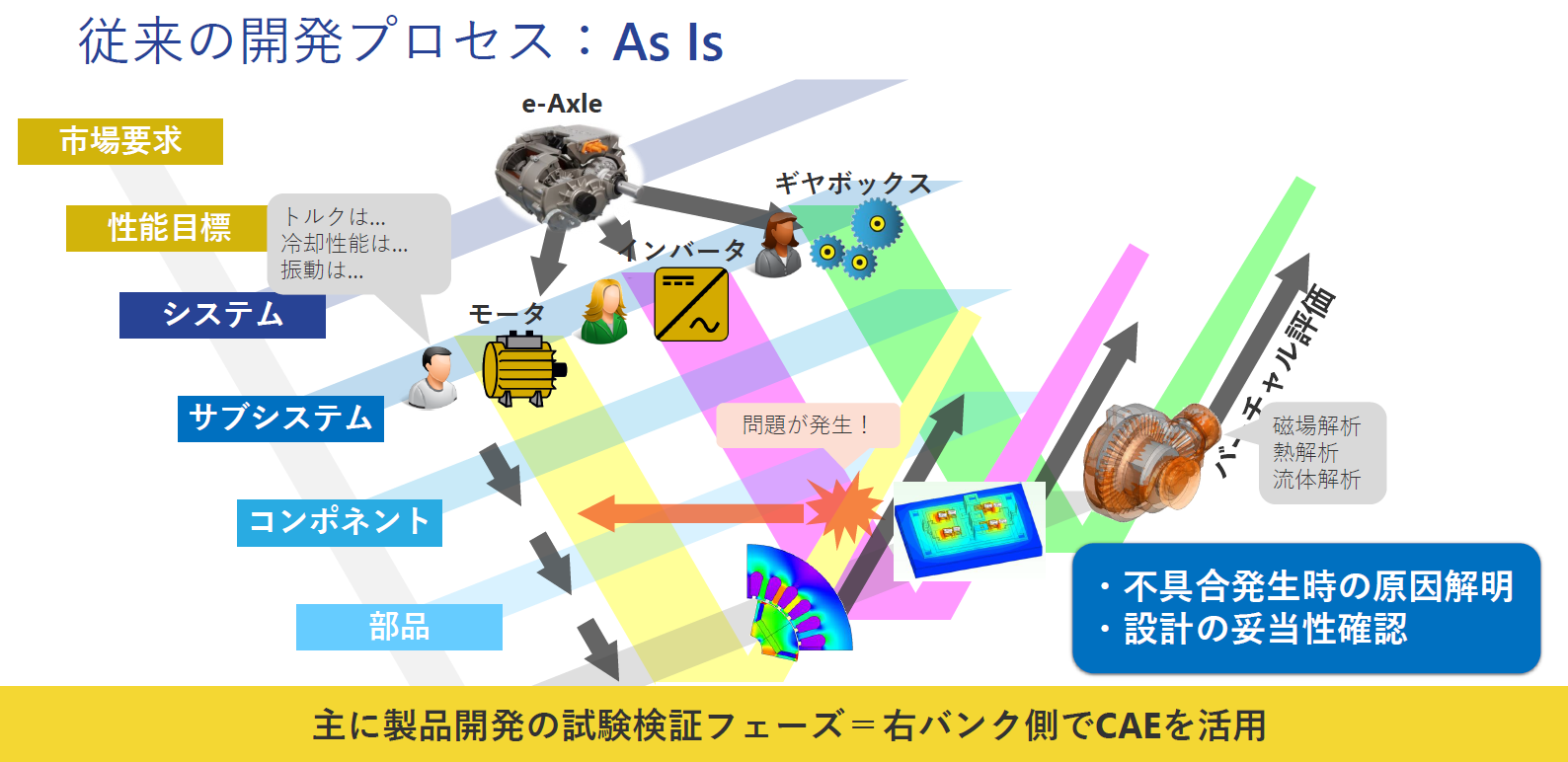
従来の開発プロセス:As Is
昨今は、シミュレーション技術の高度化やハードウェアの高速化によって、かなり複雑な物理現象をシミュレーションによってひも解くことができるようになってきました。例えば、下図に示したギアオイルのかきあげ解析のような計算負荷の高い大規模な解析や、磁場解析で得られた電磁加振力を振動解析のソースとして与えて、さらに空間への放射音を音響解析で解くといった、複数の物理現象を連携するマルチフィジックス解析も行えます。
また、これまでは右バンク側で使われていたCAEを左バンク側で「バーチャル設計」として活用する動きもあります。その中でキーとなるシミュレーション技術が最適化技術です。最適化技術は、トレードオフ関係にある複数の性能を広域に探索することによって最適解を導き出すというもので、従来の試験の代用としてのCAEから、設計のためのCAEへと適用範囲が拡大していることを意味しています。
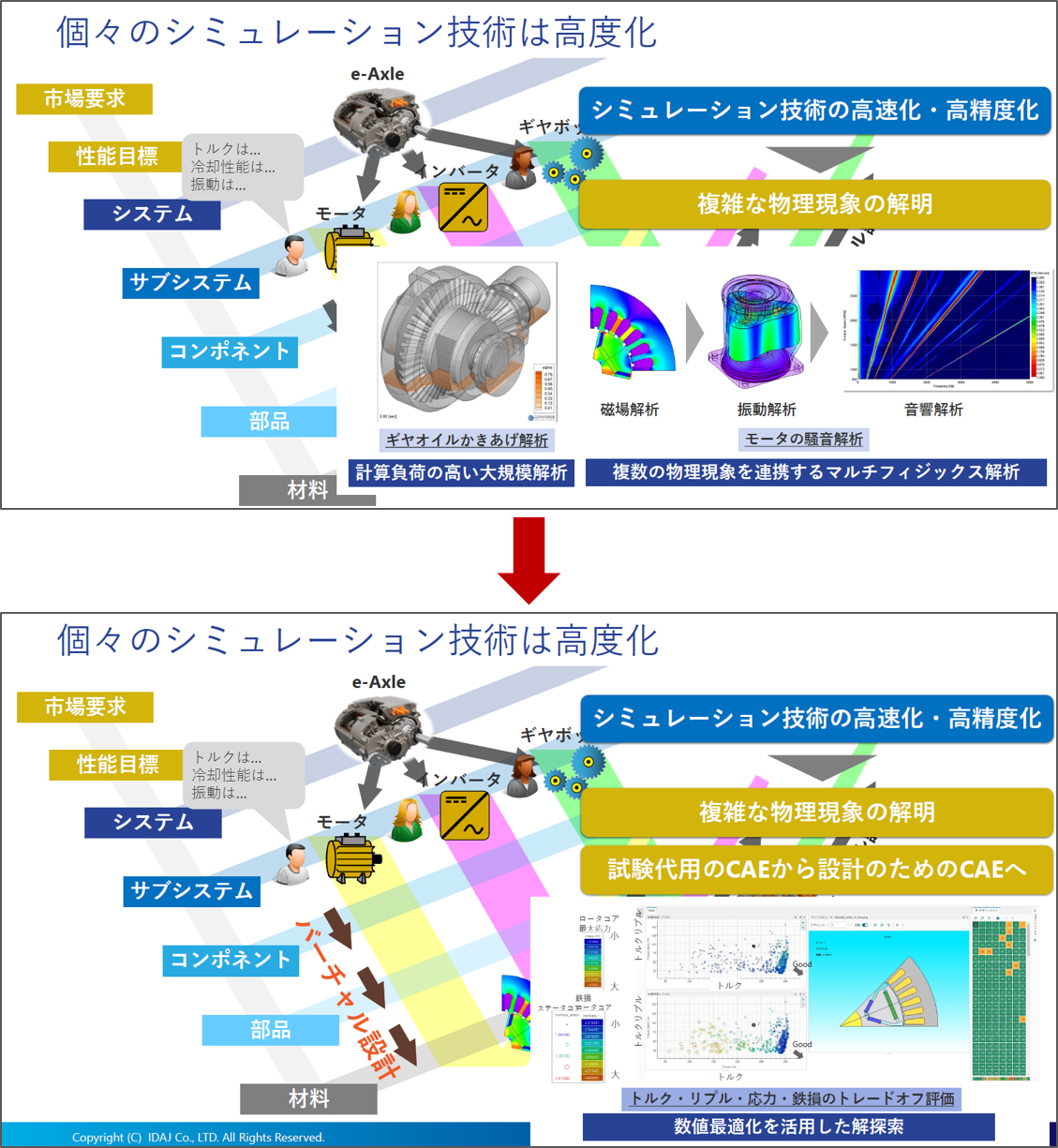
個々のシミュレーション技術は高度化
ここまで来ますと、CAEに期待されることは、コストの削減や設計品質の向上に加えて、手作業による検討を自動化することによって人的工数を削減する、作業者に依存しない標準化によって抜け漏れやミスを削減するといった業務効率と業務品質の改善であったり、先ほどご説明した最適化技術のように背反する要件に対して設計案を網羅的に検証することで製品性能の向上を図る、さらには、カンコツに基づく設計から脱却することでベテランのエンジニアでも若いエンジニアでも経験によらず同レベルでの設計ができるようになるという技術者育成の側面を持ちます。
●CAEに期待される効果(まとめ)
コストの削減 | ・試作や実験回数を減らすことにより開発コストを削減する |
設計品質の向上 | ・試験段階で発生した問題への対策案に対して根拠を明示する ・各設計行為に対して根拠を明示する |
業務効率と業務品質の改善 | ・手作業による検討を自動化することにより人的工数を削減する
・作業者に依存しない標準化により抜け漏れやミス削減を図る |
製品性能の向上 | ・背反する要件に対して設計案を網羅的に検証することで製品性能の向上を図る |
技術者の育成 | ・カンコツに基づく設計から脱却することで経験によらず同レベルでの設計が実施可能になる |
では、このようなCAEの使われ方で、果たして開発の効率化は進んだのでしょうか?
ドメインごとに分けて設計している場合、各設計領域に対しては性能がOKであっても、これらを組み上げたシステムとして評価したときに、初めて設計NGが出ることがあります。このような状況になると、設計を大幅にやり直すという時間的な余裕は当然ありませんので、制御の適合においてつじつまを合わせた“パッチあて”の対策で製品をローンチするということが往々にして発生します。
つまり、領域ごとに隔絶された設計であるがためにシステム性能が未達で手戻りが発生したり、手戻りを抑制するために、各コンポーネントを若干オーバースペックで設計するというように、全体最適が図れないことになります。
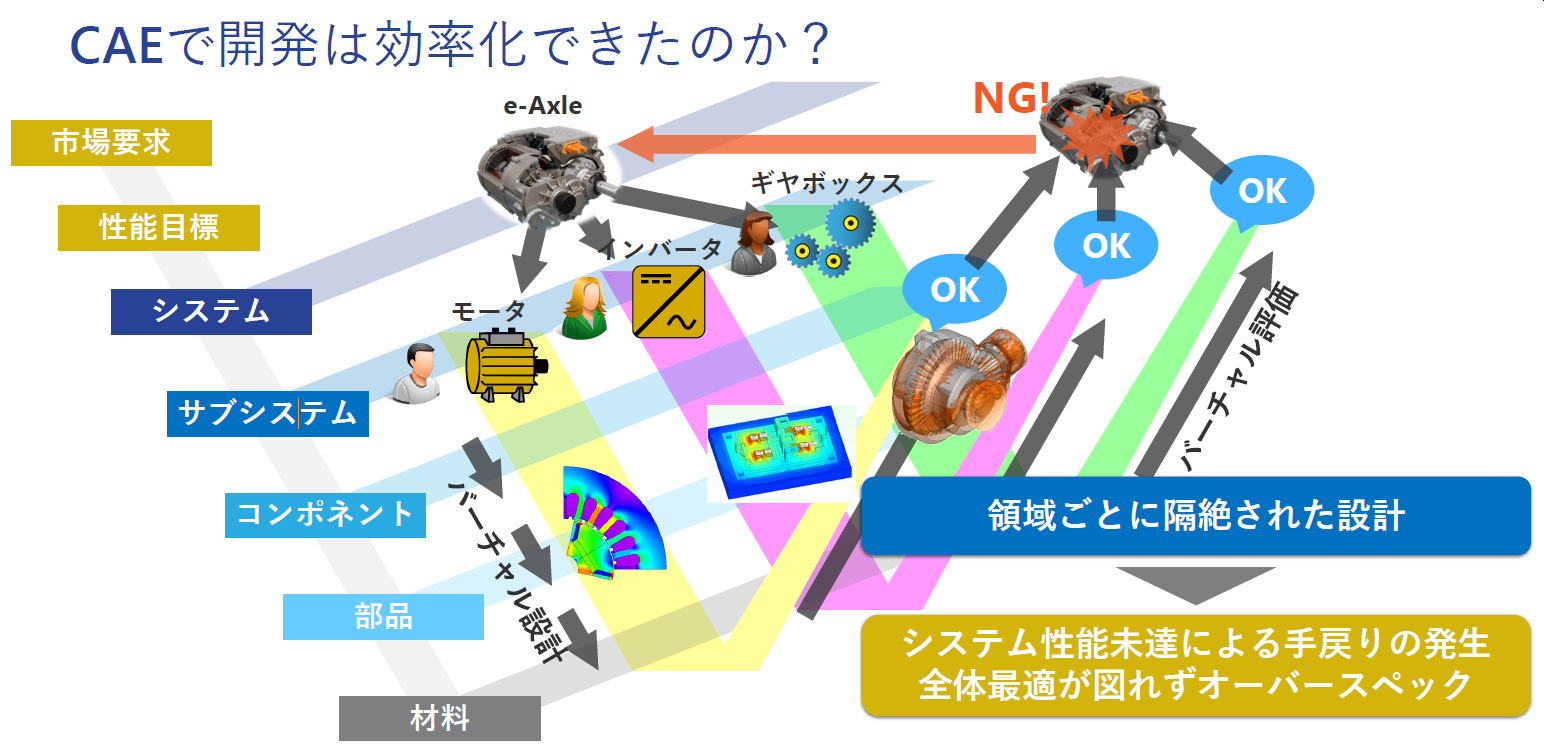
CAEで開発は効率化できたか?
電動パワートレインに求められる性能を例にご説明します。
電動パワートレインには基本性能である出力・トルク・効率、静粛性に対する機械振動・磁励振動、信頼性と耐久性に対する強度・熱・ノイズなど、様々な要件が求められます。またこれらを具現化するためにモータやインバータ、ギヤボックスという要素が存在します。これらに対して各コンポーネントが複雑に関係し合っているため、システムとしてどう全体最適を図るか?、満たさなければならない要件が互いに背反するためトレードオフをどうすり合わせるか?という課題があるため、各コンポーネントや個々の性能を評価するためのシミュレーション技術だけでなく、システムとしての性能やトレードオフを評価する手立てが求められます。
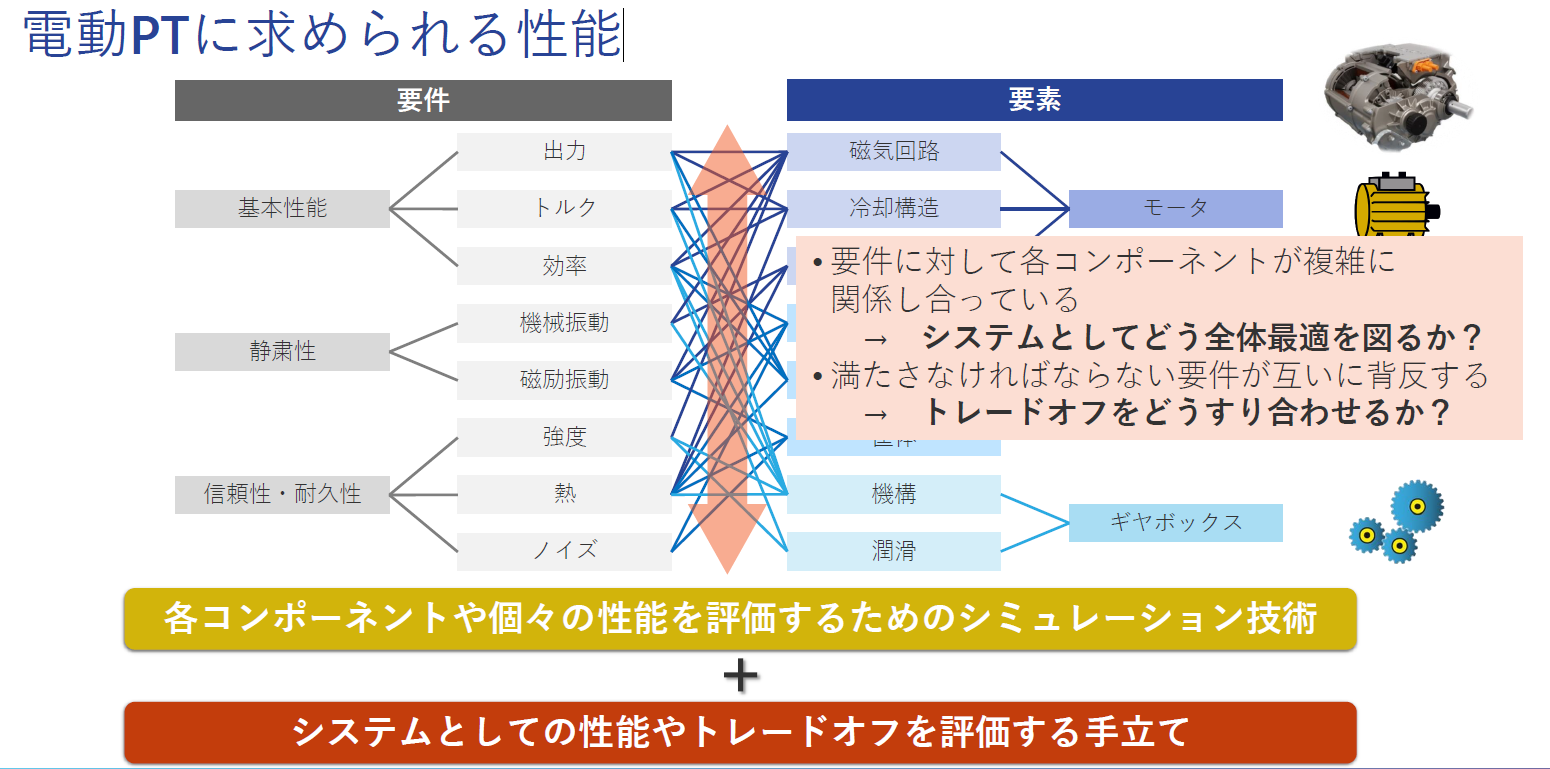
電動パワートレインに求められる性能
先述の課題を解決するソリューションがモデルベース開発(MBD:Model Based Development)です。
設計の上流側のできるだけ早い段階で1Dシミュレーションなどを用いてシステム全体のふるまいを把握し、相互に連携した状態で各コンポーネントがどういった諸元あるいは目標値を請け負うべきなのかという共通認識を持った上で、各ドメインの設計を行います。
これによって最終的にシステムを組み上げた状態でも性能が満たされた状態を目指す、つまり、下流工程における手戻りの抑制とシステムとしての最適化を実現することがモデルベース開発のねらいです。
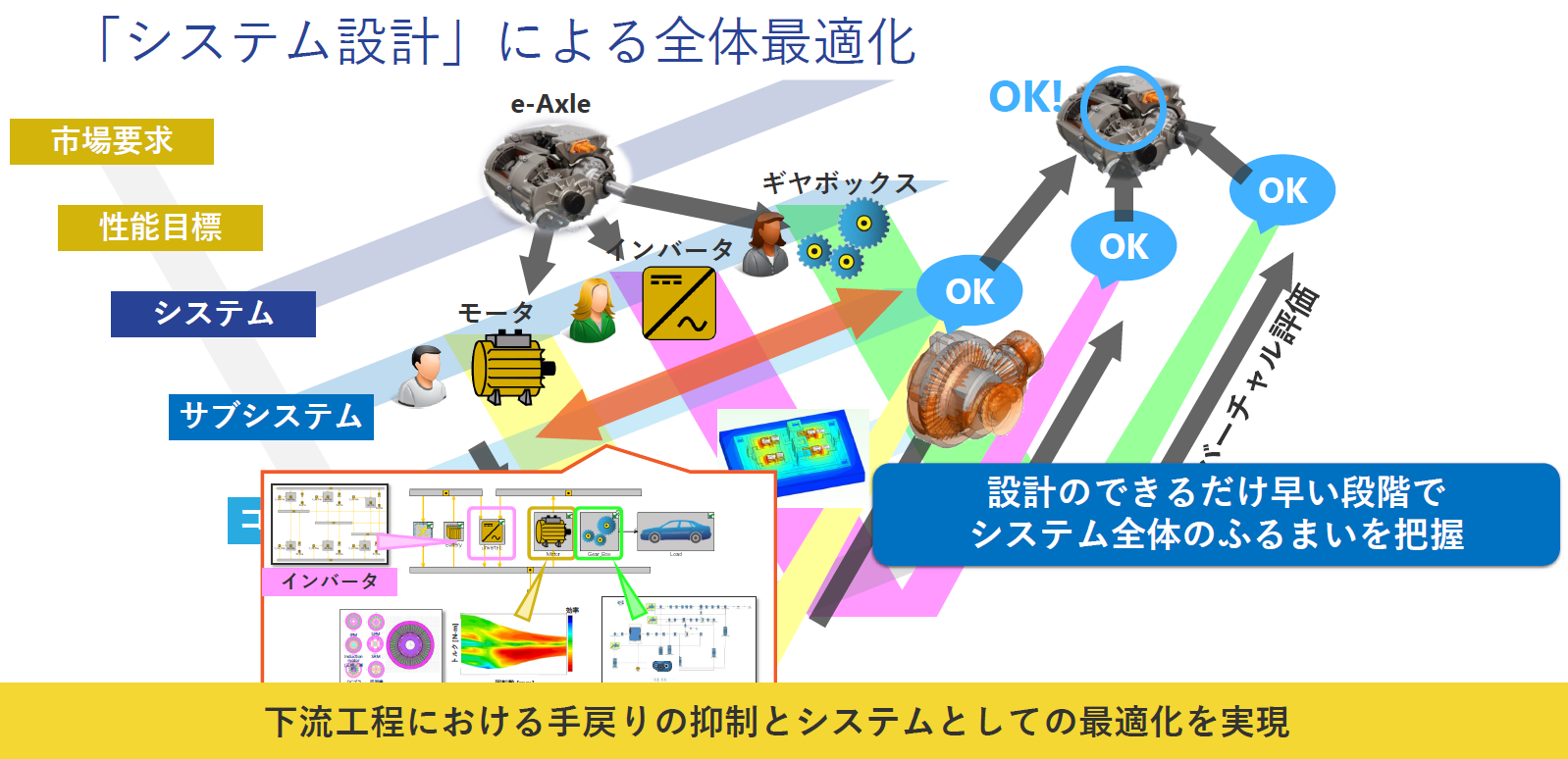
システム設計による全体最適化
●MBDに期待される効果(まとめ)
高いレベルでの協調設計の実現 | ・設計フェーズ/開発ドメイン間の認識の共有 ・コンカレントエンジニアリングの実現による開発期間の短縮 ・パッチあて設計から脱却し本質に基づく設計へ |
|
コストの削減 | ・試作や実験回数を減らすことにより開発コストを削減する | |
設計品質の向上 | ・試験段階で発生した問題への対策案に対して根拠を明示する ・各設計行為に対して根拠を明示する |
|
業務効率と業務品質の改善 | ・手作業による検討を自動化することにより人的工数を削減する
・作業者に依存しない標準化により抜け漏れやミス削減を図る |
|
製品性能の向上 | ・背反する要件に対して設計案を網羅的に検証することで製品性能の向上を図る | |
技術者の育成 | ・カンコツに基づく設計から脱却することで経験によらず同レベルでの設計が実施可能になる |
ものづくりを取り巻く環境
2021年版ものづくり白書では、サプライチェーンの強靭化(レジリエンス)があげられています。
昨今のコロナ禍や半導体不足など、突然、材料や部品が調達できないリスクに対応するには、サプライチェーンの強化が必要です。
また、カーボンニュ―トラルへの対応(グリーン)も求められています。例えば、アップル社は製品の製造から廃棄、リサイクルに至るまでのライフサイクル全体でCO2の排出量を削減するために、サプライヤーに対してもカーボンフットプリントを提供することを課しています。ご承知の通りヨーロッパでは、2035年にはガソリン車の販売を事実上禁止するといったルールや規格が変更されることが決まっていますので、このようなリスクにも対応しなければなりません。
では、これらの要請に対してどのように対応すれば良いのでしょうか?
答えのヒントが2020年版ものづくり白書に書かれています。ここでは、Ordinary CapabilityとDynamic Capabilityが取り上げられています。聞きなれない言葉かもしれませんが、Ordinary Capabilityは、技能的な効率性を図る目的で“Do the Things Right”(=正しい順番でものごとを実行する)、その結果、業務改善や開発の効率化を図ることです。前述したCAEやMBDの取り組みで取り上げた、コスト削減、業務効率と業務品質の改善、設計品質の向上、製品性能の向上が、このOrdinary Capabilityに該当します。
ただ、環境に対する対応や部品が手に入らなくなるといったことに対応するには、Dynamic Capabilityが必要だと書かれています。ここでは“Do the Right Things”(=正しいことを実行する)という視点で、それを実現するための3つの能力が、脅威と機会の感知(Sensing)、機会を補足して資源を再構築・再結合し競争優位性を獲得(Seizing)、競争優位性を持続可能なものにするために組織全体を変容させる(Transforming)です。これらを支えるための一つの手段として、デジタルトランスフォーメーション(DX:Digital Transformation)の強化があげられているのです。
つまりDynamic Capabilityは、事業環境や顧客要求の変化に対して”柔軟”かつ”迅速”に対応する力をつけていこうという考え方です。
話が矮小化することを恐れずに、先ほどの電動パワートレインの要件と要素を例に、変化への柔軟かつ迅速な対応とはどういうものか具体的にお話してみたいと思います。
まず、ルールや規格が変わるリスクという観点から、要件にある“静粛性”の規制が厳しくなったと仮定します。では顧客の要求が変更になった場合、設計はどう変更すれば良いのでしょうか?
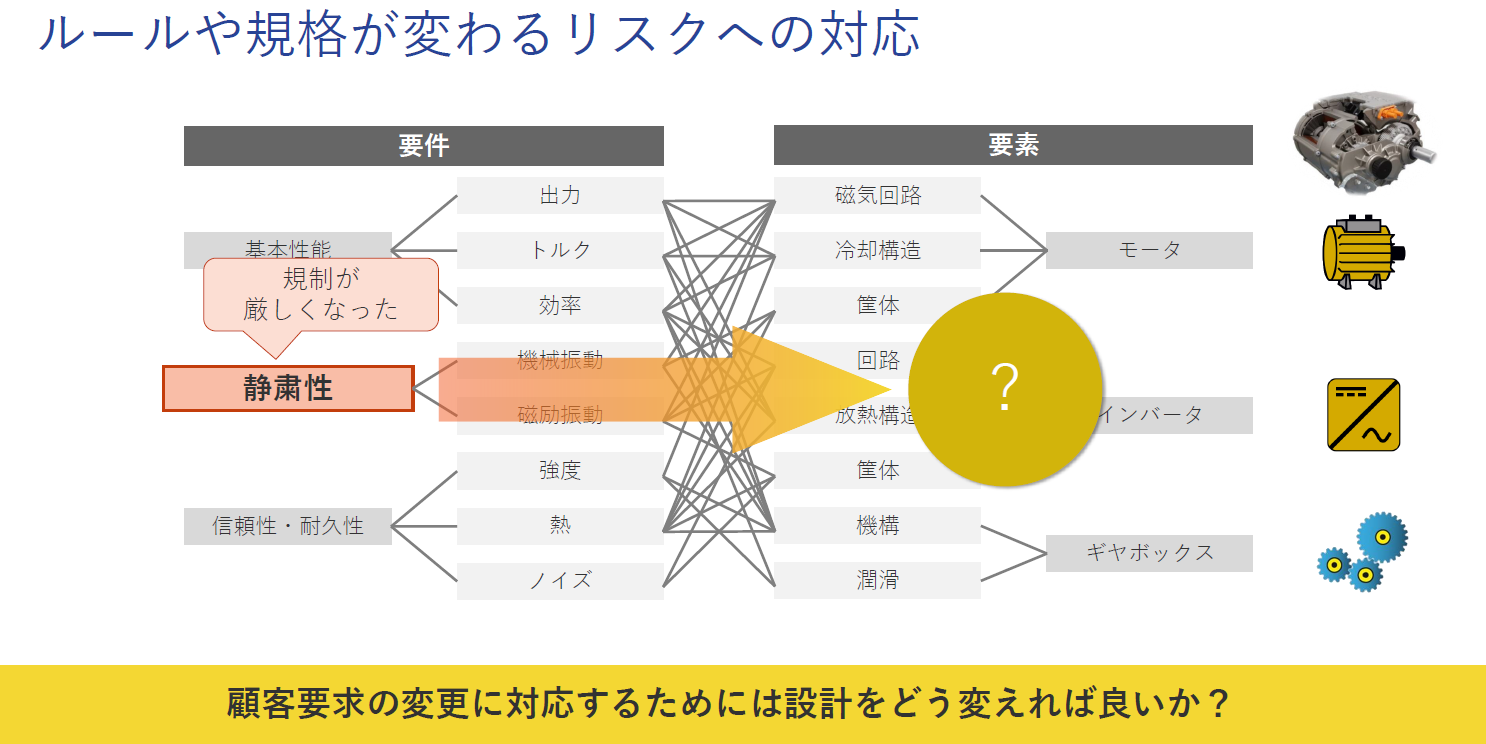
ルールや規格が変わるリスクへの対応
右側で、仮に半導体素子を検討しなければならないという設計変更が性能に対してどのような影響があるのか、また、その代替案はあるのかどうかを考えなければなりません。
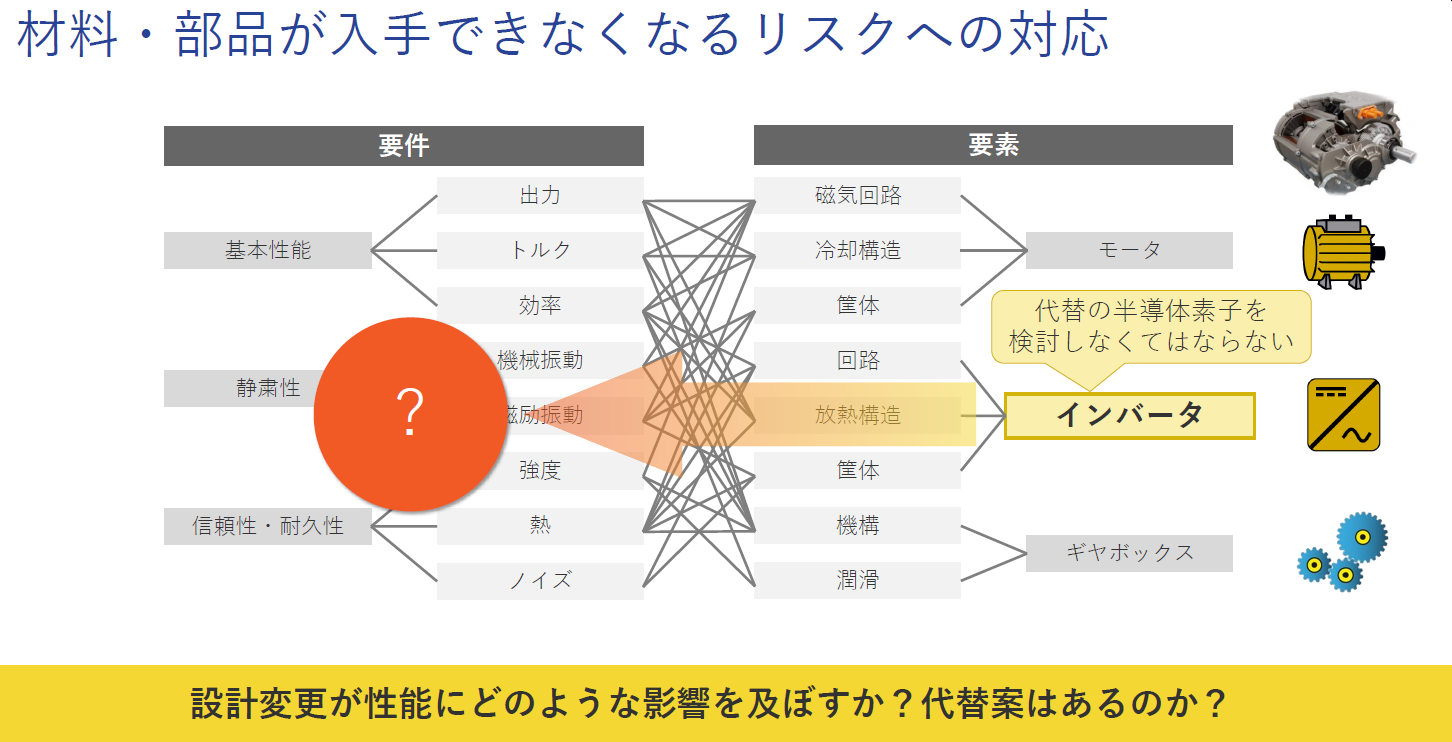
材料・部品が入手できなくなるリスクへの対応
次回は、DXに向けたモデル活用のあり方を具体的にご説明します。
■オンラインでの技術相談、お打合せ、技術サポートなどを承っています。下記までお気軽にお問い合わせください。ご連絡をお待ちしています。
株式会社 IDAJ 営業部
Webからのお問い合わせはこちら
E-mail:info@idaj.co.jp
TEL: 045-683-1990