課題分析からわかった熱設計基盤技術力の企業間格差(その1)
皆さま、こんにちは。
IDAJの錦織です。
電子機器の熱設計において、熱シミュレーションはパソコン性能の進化に伴って活用が進み、温度予測の精度も向上しました。しかし、精度の高い解析を実施するには、詳細な入力情報が必要になるため、データを揃えるには設計が仕上がるのを待つ必要があります。しかし、そのタイミングで熱問題が発覚しても、打てる対策は限られます。このような熱問題を未然に防ぐためには、やはり製品設計の企画や構想といった設計フローの上流から熱対策を意識した熱設計を実施することが必要です。
今回は、この熱設計プロセスの構築に関するアンケートを基にした課題の分析結果から、どういった対応が必要なのか、わかりやすく解説します。
熱設計プロセスに必要な「ツール」・「スキル」・「ルール」
1.製品開発・設計プロセスにおける熱に関する悩み
上流の“企画/要件定義”(図左)から下流の“試作評価/改良”(図右)までの製品開発・設計プロセスにおいて、お客様から直接お聞きした様々な熱に関するお悩みまとめてみました。これらを大別すると、使用する解析ツールの選定や操作の習得などの「ツール」、熱設計の経験不足といった「スキル」と、得られた結果をどう使うかを判断するための「ルール」という3つになります。
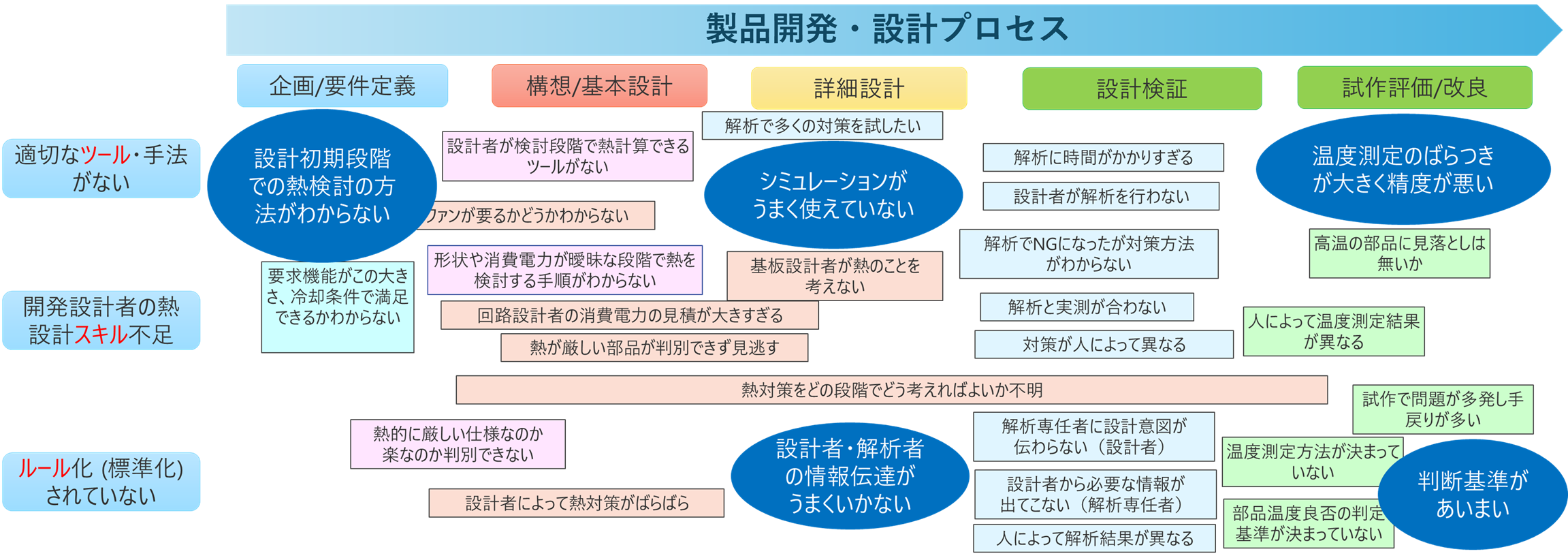
設計プロセスにおける課題
2.「ツール」・「スキル」・「ルール」の強化と連携
上流から下流まで一貫して効果的に熱設計を進めるためには、これらの「ツール」・「スキル」・「ルール」をバランスよく強化し、連携させていく必要があります。
(1)ツール
熱設計の各プロセスにおいて、その時に入手可能な情報や知りたい、判断したい情報に合わせて、適切なツールを選択します。市販ツールの設計者展開を予定している場合は、設計者が扱いやすいように、簡単に操作できるGUIを用意したり、Excelベースの簡単なマクロを作成したりするなど、設計者に使ってもらうための工夫も大切です。
(2)スキル
熱設計のためには、ある程度はご自身で温度を計算で予測することができ、放熱対策の手法なども把握しておく必要があります。この知識の有無で熱設計や対策の際の解決力に差が出ます。例えば、解析の設定を誤り、実際とはかけ離れた結果が出たときに「この条件で、この温度は明らかにおかしい」と思えることが重要です。また、導入されているツールを使いこなすスキルも必要です。こういうスキルは使っているうちに身に着きますが、ツールベンダーのトレーニングを受講することによって習得することもできます。
(3)ルール
適切なツールを準備してスキルがつけば、計算結果をどのように活用するかという方針を社内や部署内で共有します。意外に思われるかもしれませんが、計算結果は、担当者によって得られる結果がばらつくことが十分にあり得ます。属人化せず、安定した結果を得るには、スキルの向上とともに、ルールを設定することが大切です。ツールを揃え、スキルを上げても、このルール化ができていないというのは決して珍しい話ではありません。
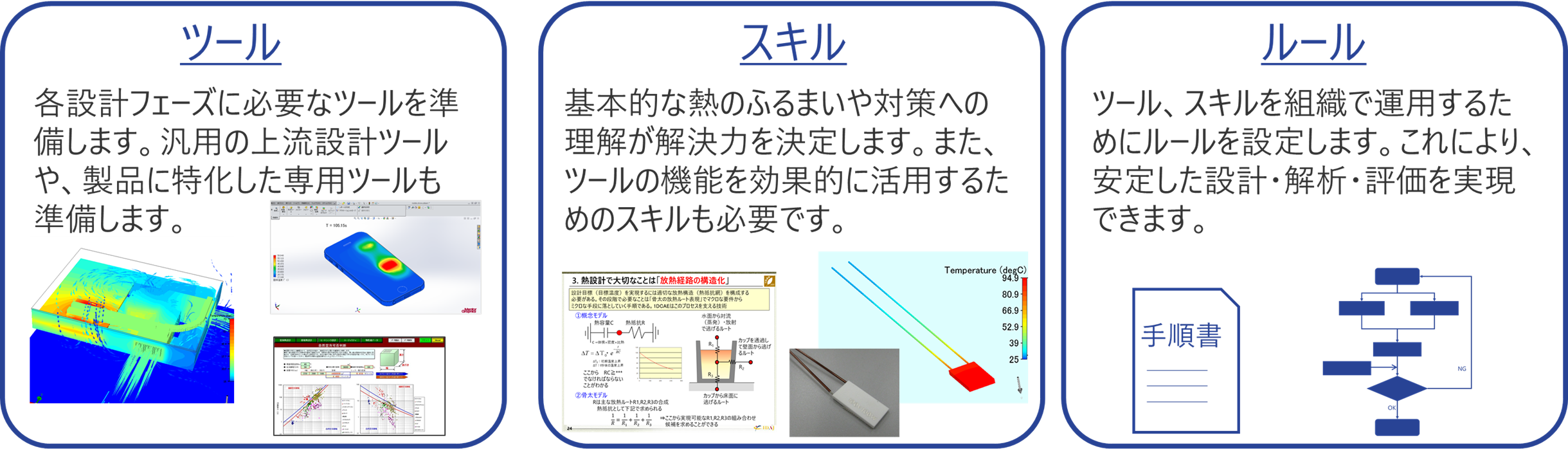
熱設計プロセスに必要な「ツール」・「スキル」・「ルール」
3.熱設計基盤技術力は企業間格差が大きい!
ツール、ルール、スキルの何が不足しているのかは、企業ごとに異なります。
こちらの図は、これまでIDAJの熱設計ステーション「CAE推進担当者向けワークショップ」にご参加いただいた、電機・自動車メーカーを中心とした75部門(複数社)の熱設計への取り組み状況をヒアリングし、それらを集計した結果です。最低点は0点、平均点は青の点線、最高点はグレーの塗りつぶしで表示しています。
レーダーチャートには、ツールに関する項目や、技術開発や教育プログラムといったスキルに関する項目、評価や熱設計のルールに関する項目がありますが、平均を見ると、スキルに関する項目や、熱設計のルールに関する項目が相対的に低いことがわかります。
図の右は企業ごとのレーダーチャートですが、各企業のレーダーチャートの形は大きく違うことが確認できます。実際にアンケートを取ってみて、私たちもここまで差があるとは予想していませんでしたので、驚きました。
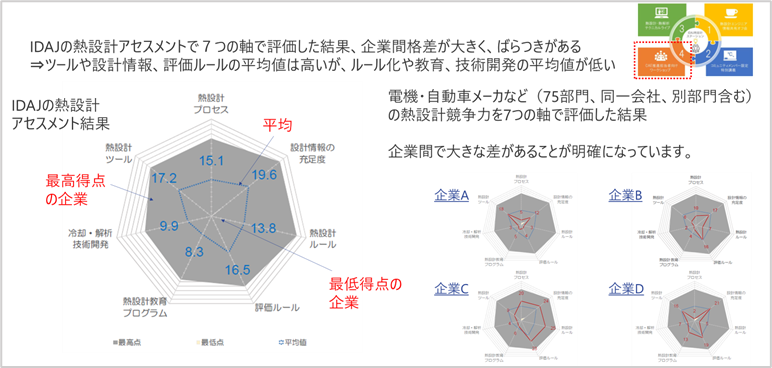
熱設計に対する取り組み状況
熱設計プロセスの構築、実測との乖離検証、解析ツールの活用方法
ここからはご相談やアンケートによって明らかになった課題を解決し、熱設計プロセスを構築するめのソリューションをご紹介します。
こちらは、製品設計のプロセスにおけるお悩みに対して、IDAJのソリューションをマッピングしたものです。「ツール・スキル・ルール」の各ポイントにおいて設計プロセスの上流から下流までをカバーしています。
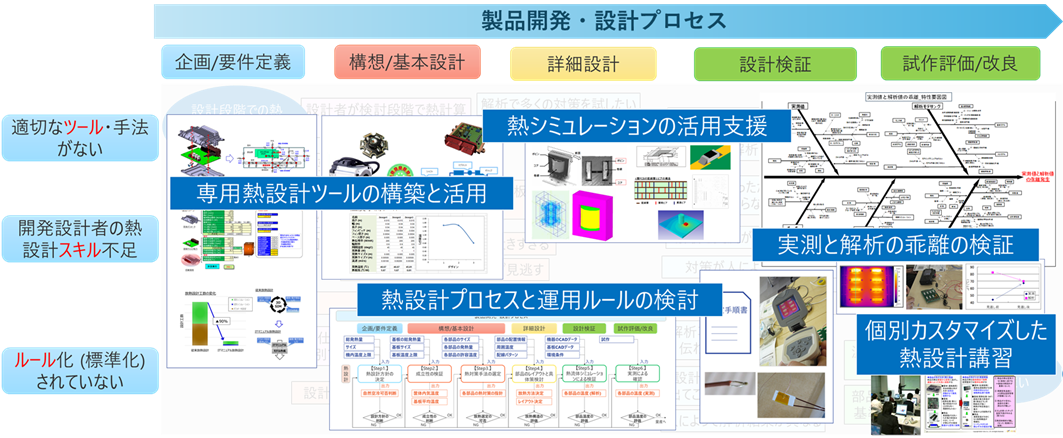
熱設計プロセスのソリューションマップ
1.熱設計プロセスと運用ルールの検討
自然空冷機器の製品開発・設計プロセスにおける“熱設計”のプロセスの例を下記に示します。企画/要件定義から試作評価/改良までの流れを5つのStepに分割します。
Step1:熱設計方針の決定
製品の動作条件を決めます。必要な動作条件から自然空冷で問題がないかどうかを確認します。
Step2:成立性の検証
基板やデバイスの温度を予測し、温度を目標温度以内に収めることができるか否か、成立性を確認します。基板やデバイスの温度が一様に分布した場合を想定して計算し、この時点で上限温度を超えている場合は、そのまま設計を続けても成立しない可能性が高いため、仕様の見直しが必要だと判断します。
Step3:部品の熱対策手法の選定
基板実装の各部品に対しては、基板に実装するだけで問題がないか、またはより高度な熱対策を施す必要があるかといった放熱手法を選定します。ここまでは、エクセルをベースとした上流熱設計のための簡易シートを使用して、短時間で繰り返し計算します。
Step4:部品レイアウトと具体策検討
Step3の結果を基に、部品の配置やヒートシンクのサイズ、フィンの枚数などの形状を決めます。ここからは物理的な形状検討になるため、主に3次元の熱シミュレーションを使用します。
Step5:熱流体シミュレーションによる検証
Step4で仕様が決まれば、製品全体の詳細な熱シミュレーションを実施します。ここで各部品の温度が設計仕様を満たすかどうかを確認し、問題が無ければ試作に入ります。
Step6:実測による確認
試作品の温度を測定し、熱的に問題がないことを確認します。ここでも問題が無ければ量産に移ります。
各Stepの終わりにはデザインレビューを設け、各Stepで得られた結果を判断するためのルールを決めておきます。各Stepで得られたデータを次のStepに受け渡す流れを明確にしておくことで、効率的な熱設計プロセス構築を目指します。
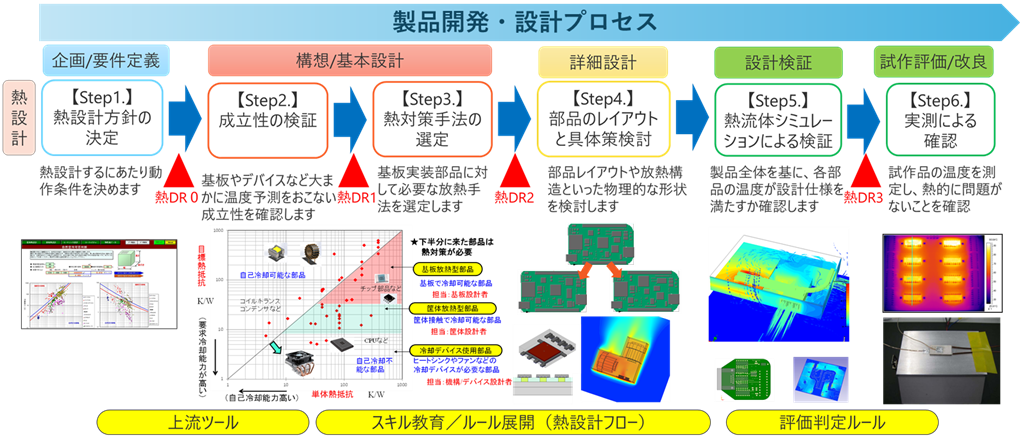
熱設計プロセス例
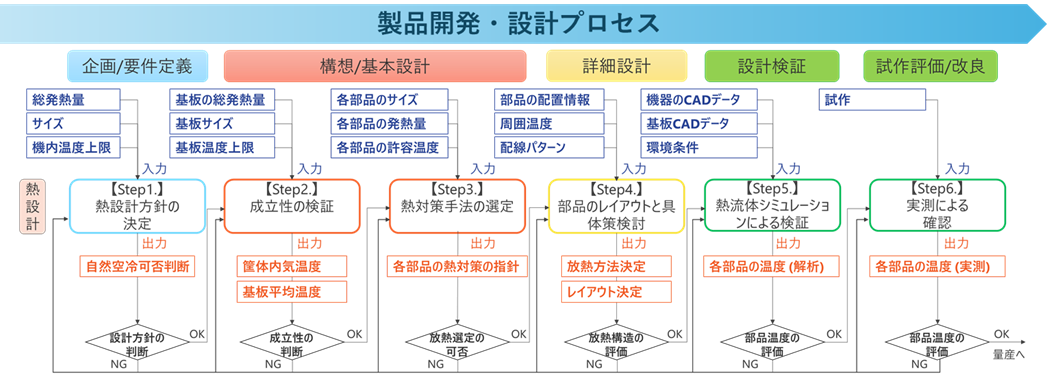
データ受け渡しのイメージ
次回は、「実測と解析の乖離検証」についてご説明します。
■オンラインでの技術相談、お打合せ、技術サポートなどを承っています。下記までお気軽にお問い合わせください。ご連絡をお待ちしています。
株式会社 IDAJ 営業部
Webからのお問い合わせはこちら
E-mail:info@idaj.co.jp
TEL: 045-683-1990