熱とノイズの協調設計 ~そのプロセスの解説~(2)
皆さま、こんにちは。
IDAJの中嶋です。
前回を受けて、ここでは熱とノイズの協調設計の適用例についてご説明します。
熱とノイズの協調設計の適用例
前回、ツールについてご紹介しましたので、ここからはプリント基板の設計において、熱とEMIの問題をSimcenter Flotherm(以下Flotherm)とDEMITASNXを使用して解決する「協調設計」についてご説明します。
FlothermとDEMITASNXは、どちらも基板CADとのインターフェースがありますので、以下の図のように基板CADを中心に置いて考えていきましょう。
DEMITASNXに基板CADのデータをインポートしてEMIを検証し、その結果を基板CADにフィードバックしたり、Flothermで基板CADのデータをインポートして部品の温度を検証し、その結果を基板CADにフィードバックします。いずれもツール上で部品の位置を変更することができますので、DEMITASNXでの検討結果を踏まえて、同様の変更をFlothermで実施するというように、検討結果をお互いのモデルに反映させながら、EMIと熱を両立する仕様を検討し、結果を基板CADにフィードバックするといったことが可能です。
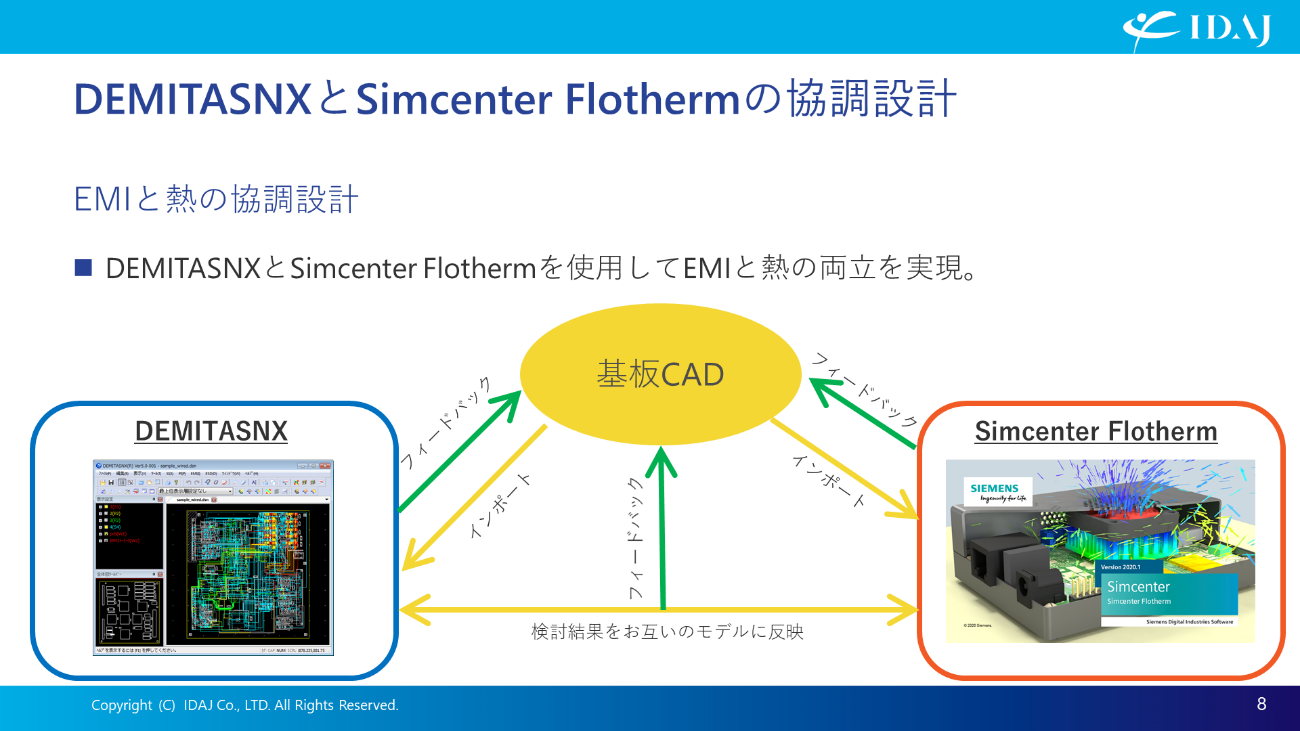
EMIと熱の協調設計
FlothermとDEMITASNXの協調設計は、基板設計フローの中の「回路設計」の後の、「部品配置設計」の段階や「配線パターン設計」の段階で行います。
「部品配置設計」段階では、DEMITASNXを使用してEMIチェックを実施することで、検討済の配置を用いて配線パターンを引くにあたって、問題が起こりそうな接続を事前に検出します。Flothermでは、その部品配置を使用した基板の熱解析を実施し、各部品の温度に問題がないかを検証します。
「配線パターン設計」段階においても、EMIチェックを実施して、実際に作成した配線パターンの形状から、「パターンの中にEMIのアンテナとなるような部分が隠れていないか?」などといったEMIが発生する危険性のある箇所を検出します。Flothermでは、配線パターンを含めて基板の熱解析を実施することで、配線パターンを作成した後の基板でも、各部品の温度に問題がないかどうかを検証します。
お分かりのように、これらの設計は試行錯誤しながら進めるため、1回の計算に時間がかかると設計に使用することは難しいのですが、計算が速いDEMITASNXとFlothermなら、短時間の評価が可能となるため、基板設計と並行してEMIと熱の評価を進めることできます。
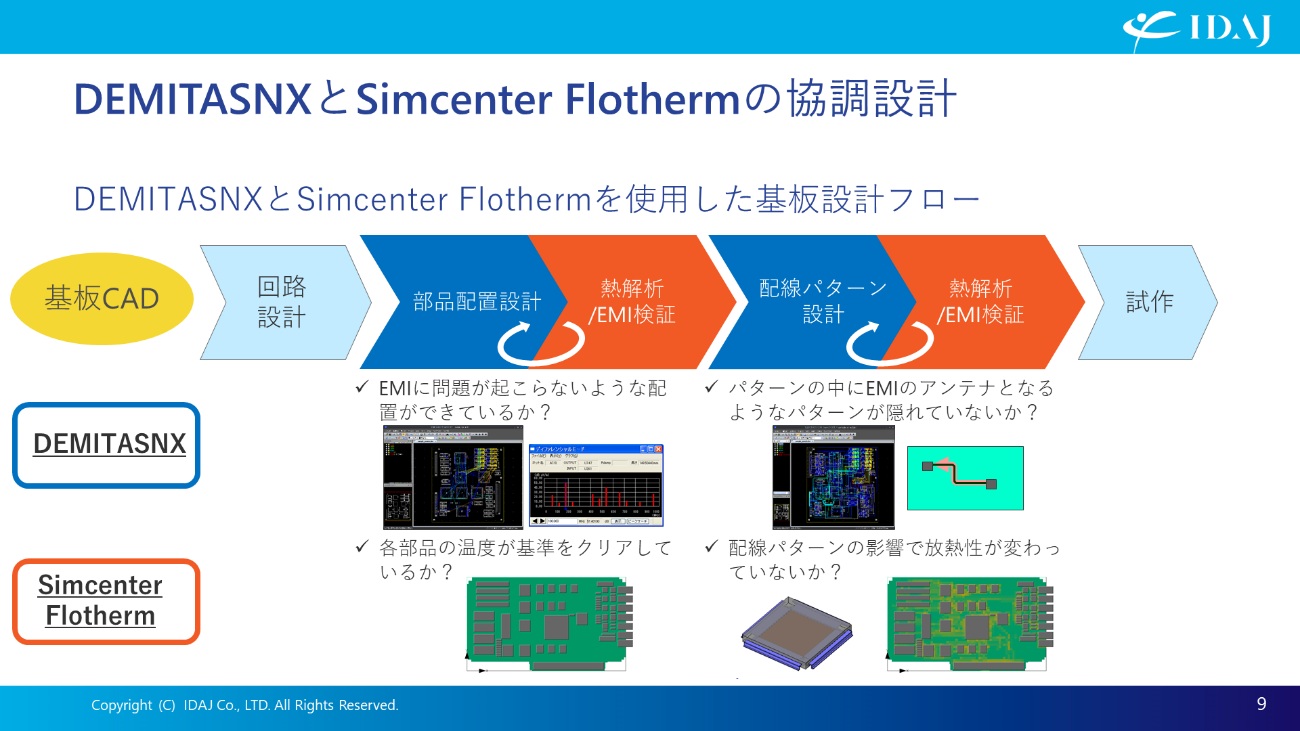
DMITASNXとSimcenter Flothermを使用した基板設計フロー
「部品配置設計」や「配線パターン設計」の中に、 DEMITASX とFlothermを使用するフローを取り入れて、試作前の早い段階でEMIと熱を平行して評価しながら基板設計を実施することで、部品追加などの暫定的な対応による製品のコストアップや設計の手戻りを減らし、極力、開発期間が延長することがないような設計を目指します。
設計の進め方の概要のご説明はここまでにして、続いて「協調設計」の適用例についてご紹介します。
回路設計が終了し、これから「部品配置設計」と「配線パターン設計」に取り掛かろうとしている状態で、DEMITASNXによるEMIチェックとFlothermによる部品温度の解析の両方をおこないながら、基板を設計する流れを想定しています。
主要部品として使用する部品はある程度絞られているため、Flothermの熱解析ではFlotherm Packで作成した詳細モデルを準備しました。こちらを使用することで、主要部品のジャンクション温度を解析で求めることができるようになります。
まずは、部品の配置設計から始めましょう。
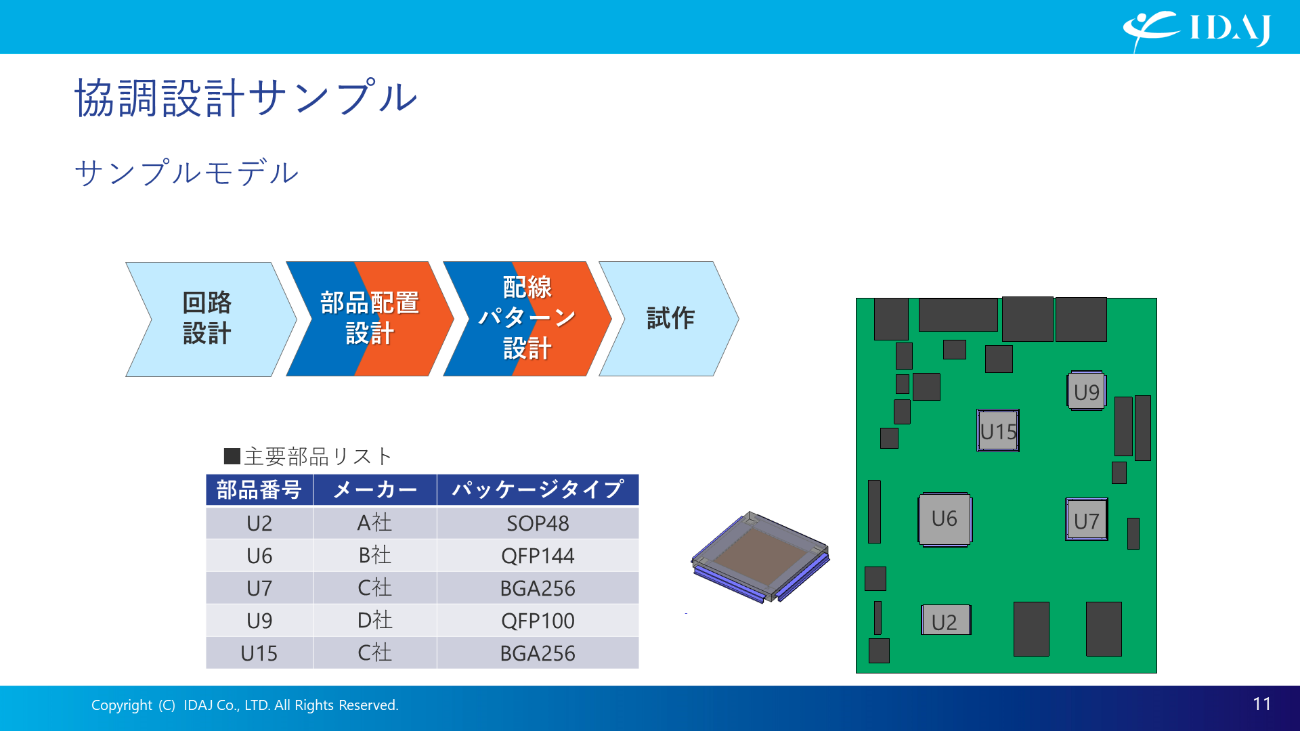
協調設計サンプル
部品の配置を検討し、候補があがってきたらDEMITASNXのEMI検証と、Flothermの熱解析を実施します。
下図は、DEMITASNXとFlothermでの計算結果です。
右はFlothermの結果で、基板全体の温度分布を表示しています。主要な部品のジャンクション温度を抽出しており、全て上限値の85℃以下に収まり設計条件をクリアしていることがわかります。
左はDEMITASNXの結果で、各部品の位置と接続情報から、EMIで問題が発生しそうな部分を検出しています。赤色のラインは検討が必要な項目が多い部分を示しており、全体的に赤色のラインが多くみられるため、EMIで問題が発生しそうな個所が多いことがわかります。また、周波数特性グラフでは周波数別にEMIの強度を表示したり、エラーになった接続については、どこが、どういう理由でエラーになったかを図解し、対策案が提示されます。
こちらの結果から、部品の温度は目標をクリアしていますが、EMIではエラーが多く、問題が発生することが予想されるため、配置を少し見直したいと思います。
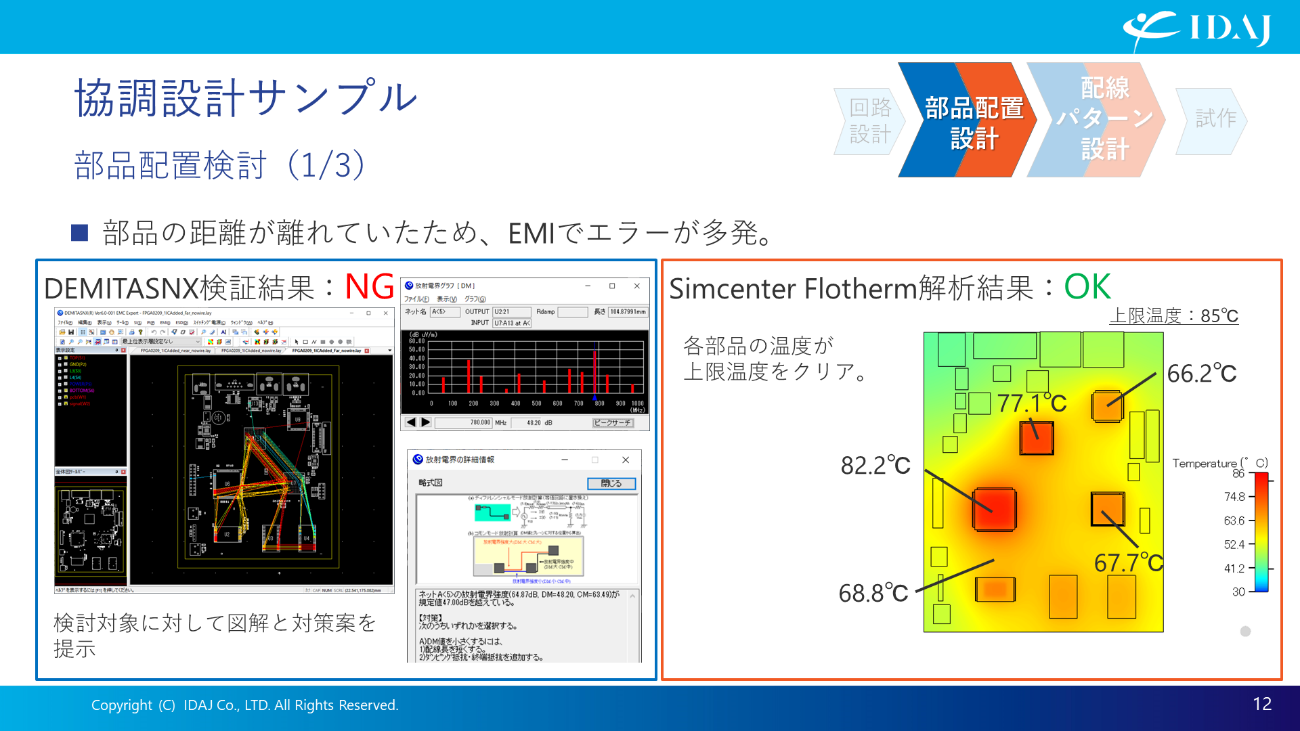
部品配置検討(EMIでエラーが発生)
結果を参考に部品の配置を見直し、各部品を基板の中央付近に寄せてみました。
この配置で再度、DEMITASNXのEMI検証と、Flothermの熱解析をそれぞれ実施した結果を示します。
DEMITASNXの結果を見ると、赤色のラインがほとんどなくなり、検討が必要な項目の数が目標数を下回りましたので、EMIは問題のないレベルになったと判断することができます。
他方、Flothermの結果を見ると、主要部品の中に温度が上限の85℃を超えた部品がありますので、今回は、EMI的にはOKですが、熱的にNGという結果になってしまいました。
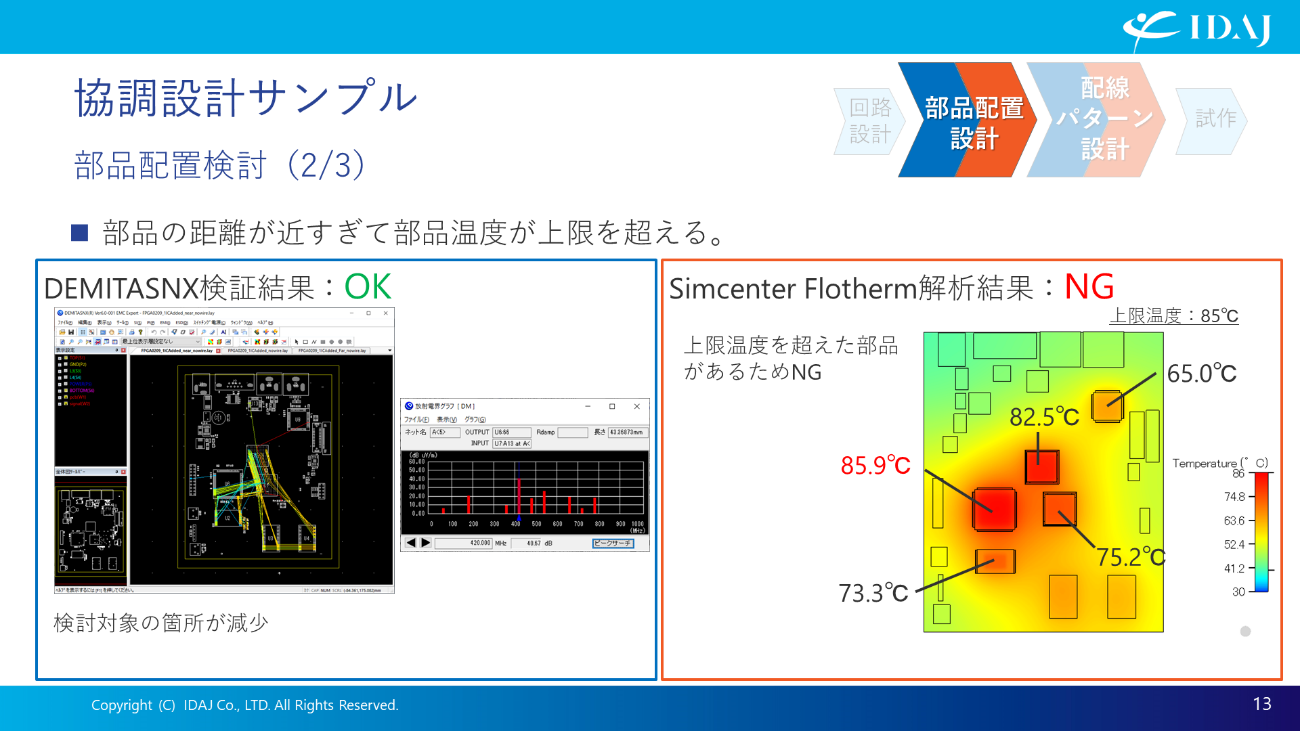
部品配置検討(温度の上限超過)
再び部品の配置を修正します。前の2回の検討結果を踏まえて、“近づけすぎず&遠ざけすぎず”のバランスをとった配置にしてみました。
DEMITASNXのEMIチェックでは、検討が必要な項目が少し増えていますが、目標数は下回っています。Flothermの結果でも、主要部品の温度は全て85℃以下に収まっており、EMIも熱も、どちらもクリアしましたので、この部品配置を採用することにします。
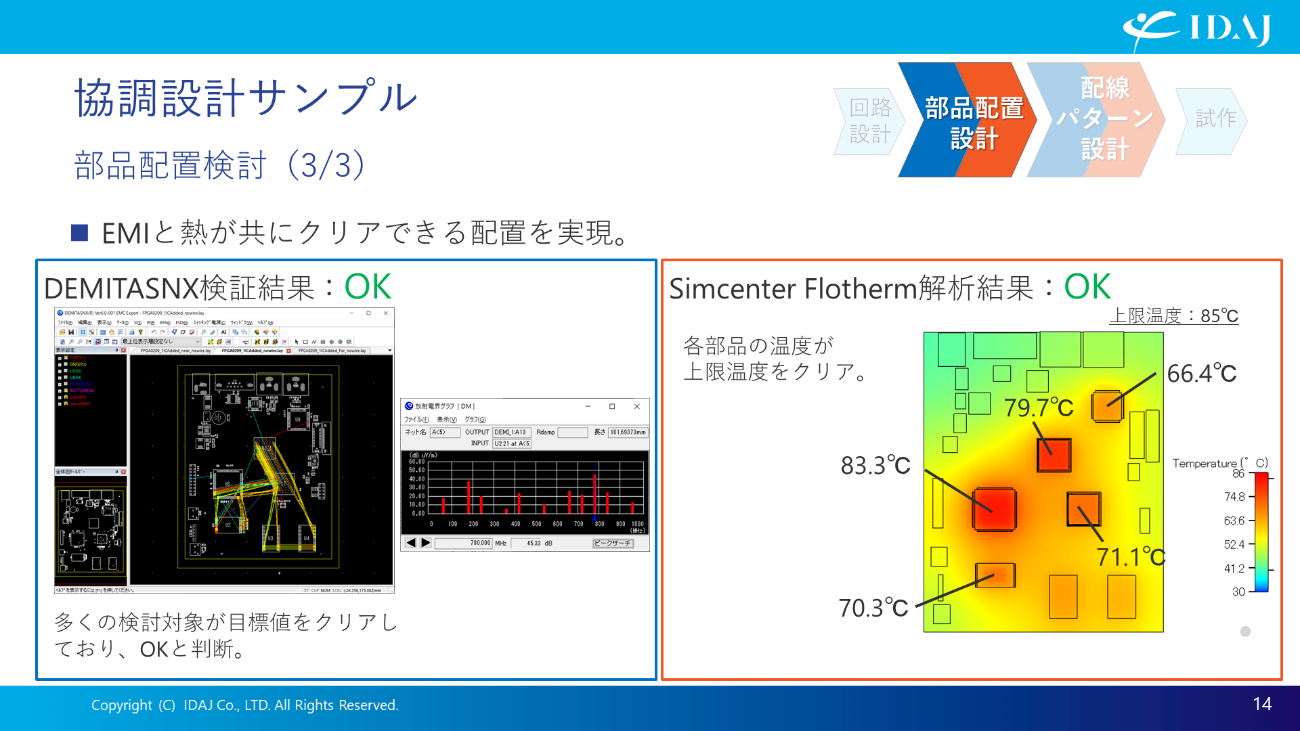
部品配置検討(EMIと熱の条件をクリア)
「部品配置設計」が完了したら、次は 「配線パターン設計」に移りましょう。
「部品配置設計」で採用した配置に対して、配線パターンの形状を設計します。配線パターンを作成ができたら、DEMITASNXとFlothermで配線パターンの形状を含めた解析を実施します。
DEMITASNXのEMIチェックは、作成した配線パターンの形状を確認して、EMIが発生するような危険なパターンが見つかればその場所を検出します。今回の結果は、検討が必要な箇所はさほど多くはなく、目標数を下回っていました。
他方、Flothermでは、配線パターンの形状を考慮することで、部品からパターンへの放熱をより詳細に解析できるようになります。配線パターンの引き方によっては放熱性が大きく変わり、その影響で温度が高くなっていないかを確認します。今回は、各主要部品の温度が上限温度以下に収まっていることがわかります。
以上の結果から、配線パターンを作成した基板でも、EMIチェックと部品温度のどちらも問題ないと判断することができます。
このように、試作前にEMIと熱をしっかり検証することで、試作後にEMIと熱の問題が発生しづらい基板を作成できるようになります。
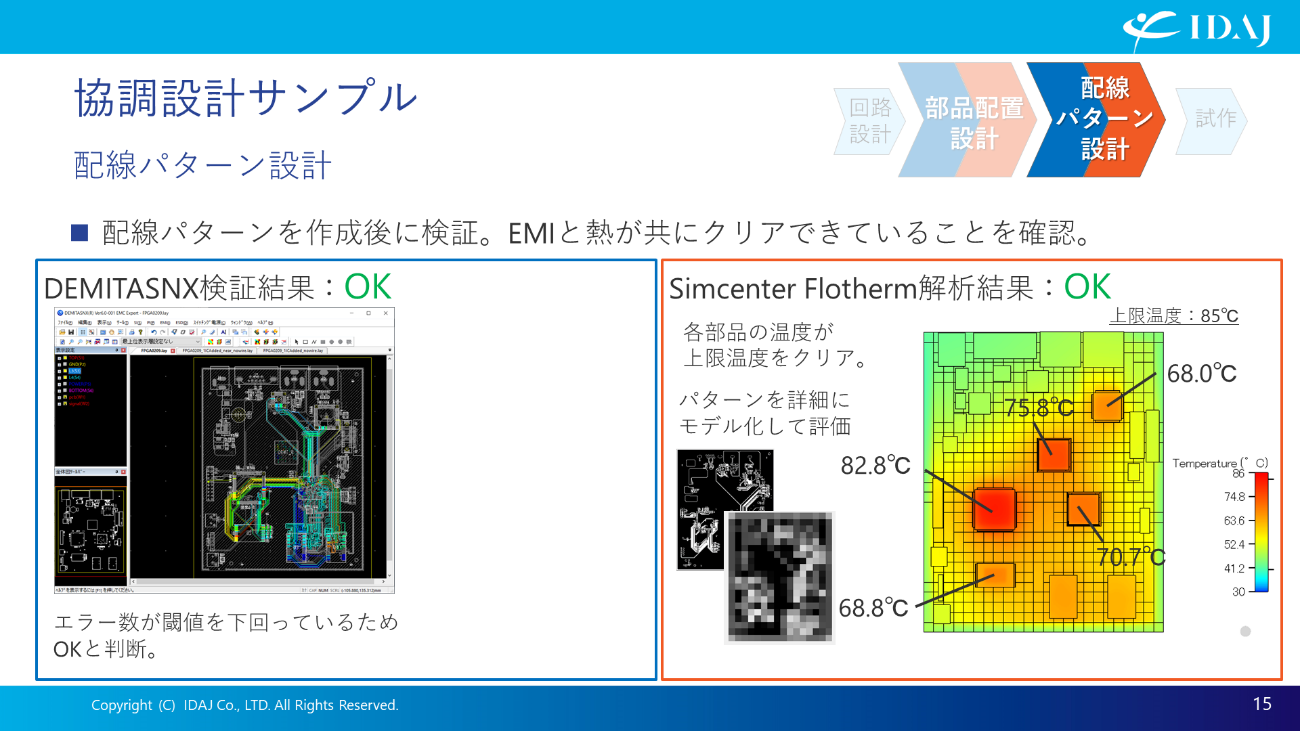
配線パターン設計
まとめ
プリント基板のEMI検証ツールであるDEMITASNXと、電子機器の熱設計支援ツールであるSimcenter Flothermを使用した協調設計の例を紹介させていただきました。これら2つのツールを一緒に使用することで、基板設計の初期段階からEMIと熱を両立した設計を実現し、設計を効率化することができます。
試作後の暫定的な対策によるコストアップや、設計の出戻りによる設計期間が延長を避けながら、品質の高い製品開発に向けて、DEMITASNXとSimcenter Flothermをご活用いただき、EMIと熱の協調設計にお取組み頂けると幸いです。
DEMITASNXやSimcenter Flothermといったツールだけでなく、開発プロセスの効率化といったご相談なども承りますのでお気軽にお問い合わせください。
■オンラインでの技術相談、お打合せ、技術サポートなどを承っています。下記までお気軽にお問い合わせください。ご連絡をお待ちしています。
株式会社 IDAJ 営業部
Webからのお問い合わせはこちら
E-mail:info@idaj.co.jp
TEL: 045-683-1990