中北製作所 様(IDAJ news vol.112)
設計探査をベースとした流体制御装置の開発にmodeFRONTIER®・SIMULIA® Abaqus Unified FEAをご活用
株式会社 中北製作所
経営企画本部・技術本部 様
IDAJ news vol.112お客様紹介コーナーより抜粋
発行日2023年6月
解析種別:設計探査
課題等:液体水素用バタフライバルブ、シール性能向上、材料特性と機械的な特性のフィッティング、シール面構造の設計探査、チョークフロー弁、CAP機能、設計探査
省略
- ありがとうございます。早速ですが、現在ご契約いただいているSIMULIA Abaqus Unified FEA(以下 Abaqus)をご導入いただいた理由と経緯をお聞かせいただけますか。
- 液体水素用バタフライバルブの開発にあたっては、弊社には対応できる実験設備がないため、解析によって開発を進めることにしていました。しかし、いざ構造解析を始めてみると、液体水素用バタフライバルブの構造的な特徴から、接触機能を多用して物理現象を再現する必要があることがわかり、スピード感を持って開発を進めていくのに必要な解析結果を得る事を目的にAbaqusを導入させていただきました。また、今後の設計開発への展開を考えると、流体構造連成解析が視野に入っています。弊社で使っている流体解析ソフトウェアとの親和性、接触の機能を考慮するとAbaqusが良いという結論に至りました。また、個人的にIDAJさんの技術サポートを受けた経験があり、サポート力に信頼を置いていたことも選定理由の一つです。
- Abaqusをご利用いただいてご苦労されたこと、導入効果について教えていただけますか。
- これはAbaqusに限ったことではありませんが、製品の特性上接触が多用されていることと、材料非線形の問題を扱うのに苦労します。現状、バタフライバルブのシール部にはメタルシールを使っていますので、弾塑性材料となります。弾塑性材料に接触の非線形が加わり、さらに製品形状を模擬した3次元解析をしようとすると次元の問題が追加されるわけですから、Abaqusであっても収束させるのは大変です。
こういった解析では、解析コストがかなり上がりますので、3次元形状で、現象を解析する必要があるのかを慎重に見極めていかねばなりません。端的に申しますと、開発では、3次元形状を使って解析する必要はほぼありませんので、2次元に縮退させた簡易モデルでいかに設計探査するかを考えています。この現象と形状の簡略化が肝要で、Abaqusでもそういった使い方をすることで対応しています。
一番の効果は、別のツールでは解析できなかったものが、解析できたということですね。一聴すると至極当然のことのように思えるかもしれませんが、解析できない、結果が得られないなら、そもそも製品の開発が進まないのです。解析によってバタフライバブルの構造メカニズムを正しく把握することができたことと、modeFRONTIERとの組み合わせによる設計探査によって、どの設計パラメータが現象に対してどういった影響を及ぼすのか、どのような形状がより良いかというように現象ベースでの見極めができ、構造の作り込みができたことで、当初目標の口径300Aに対して、3年の期間の本プロジェクトでは、最大口径800Aという目標に挑むことができました。最終的には来週以降(註:2023年3月)に実証試験を行い、製品性能について最終的な判断を下すことになります。 - “設計探査”のお話が出ましたが、そのためにmodeFRONTIERもご利用いただいています。このmodeFRONTIERについてもご導入の経緯や成果などをお聞かせください。
- これまで私が利用してきた中で一番稼働率が高いソフトウェアがmodeFRONTIERです。私自身の開発思想は、基本的に“設計探査ベースで開発する”というものです。解析に定量性を求め、実験とのバリデーションを厳密にやっていかなければ解析は使えないというご意見があることも承知していますが、それではコストと時間がかかり過ぎます。弊社のような規模の会社が、解析を活用して成果を出すには設計探査が有効だと考えています。その観点からmodeFRONTIERという最適化ソフトウェアをいかにして使い倒すかがポイントとなります。導入にあたっては、modeFRONTIER以外のツールも検討しましたが、IDAJさんの技術サポート力を重視して選択しました。
バタフライバルブのメタルシール形状、材料特性と機械的な特性のフィッティング、シール面構造の設計探査をAbaqusと modeFRONTIERを連成させて実施しました。性能に対する設計変数の寄与を把握した上で、選好解をどう選ぶかが重要ですから、定量性に拘ることなく、目的の達成に必要な粒度の解析モデルで設計探査を実施します。その後は、弊社の特長でもある現場のすり合わせ力で作り込む。これが、スピード感を持って開発するために、解析を現場に生かすことにつながるのではないかと考えています。 - ここからは具体的に適用事例をご紹介いただけますか。
- まずは、液体水素用バタフライバルブの開発に適用した事例をご紹介します。
NEDOの支援を受けて開発している液体水素用バタフライバルブの開発目標は、液体水素の極低温環境でシール面に必要なシール面圧を確保すること、メンテンス性を確保してバルブ外表面で液体酸素を生成させない真空断熱構造を実現することにあります。これまでの小規模実証等では、グローブバルブと呼ばれる弁で液体水素を制御していましたが、構造上、大型に適さないことから、大口径でもコンパクトな「バタフライバルブ」で、液体水素の荷役用バルブを開発することになりました。バタフライバルブは、弁体と呼ばれるディスクを回転させることで流体の流れを制御しますので、その設計には、弁体と接触するシール部材との接触面圧と接触幅が重要になります。現在開発しているバタフライバルブは、弁軸が二重に偏芯している二重偏芯バタフライバルブです。そのため弁を全開から全閉にする際、弁体とシール部材との接触開始点が上下対象ではあるものの、構造上は左右非対称となり、全閉までの間に徐々に接触範囲が拡大していくことになります。また、これまでの経験から流体を封止するには、弁体とシール部の接触面圧が一定以上必要であることがわかっています。極低温環境では、部品間の熱収縮差の影響を受けるため、全閉時のシール面圧を均一に制御することが求められます。 - 液体水素用バタフライバルブの開発では、液体水素による実液試験を行うにも回数が限られること、バルブが大口径であり製作には費用と時間もかかることから、可能な限り解析を活用し、事前に性能を予測したいと考えました。解析によって事前に性能を作りこんで、液体水素による実液試験時に性能を確認し、開発コストを抑えるのが狙いです。先にご紹介した2つの開発目標達成に向けて解析を活用しましたが、ここではシール性能向上のための取り組みについてご説明します。
数値解析のアプローチとして、シール部材の物性がわからないと解析できないことから、まずはシール部の物性値フィッティングを行い、バルブを含めたシール部の設計探査の後に、バルブの開閉解析を行いました。
シール部の構造を、簡易的なモデルを使ってご説明します。シール部は主に、弁体、シール部、バックアップリング、バックアップリングを支えるためのバネで構成され、弁体とバックアップリングは弾性体、シール部は弾塑性体の三層構造になっています。流体は弁体とシール部の間を流れ、弁体が回転しながらシール部と接触することで接触圧を確保し、流体を封止します。シール部には異なる材料を使用していますので、これらの物性を推定するために実験と解析を行いました。
シール部材は、外被、内被、スプリングで、スプリングをトーラス状にしたものに、板材の外被・内被を巻き付けたような構造をしています。実験ではシール部のパラメータが異なる三水準を用意してデータを取得し、この荷重変位曲線から、modeFRONTIERを用いてシール部材の物性をフィッティングしました。 - 合わせ込む物性値は、ヤング率、降伏応力、応力-ひずみ曲線です。実験では、パラメータが異なる三水準のデータを取得しましたので、解析でも三水準で計算し荷重変位曲線のカーブフィットを行いました。材料物性値は三水準で共通とし荷重変位曲線は載荷・除荷を2回繰り返しました。modeFRONTIERでは、一つの材料物性値の組み合わせに対して3つの解析を行い、1つの解析あたり4本のカーブを取得しました。そのためmodeFRONTIERの一デザインあたり12本のカーブフィットの結果から誤差の最小化を目的関数としました。また制約条件として載荷時の荷重値の上限、除荷時のシール部材の戻り変位量の下限値を設定しました。最適化アルゴリズムはpilOPT、初期値はオートノマスとして解析が終了するまで実行しました。1デザインあたりの解析時間は3分。実際には、解析終了するまで探査させてもすべての制約条件を満たす最適解は探査できませんでしたので、ポスト処理で制約条件を緩和しながら選好解として初期載荷と最大荷重値がおおよそフィッティングできたデザインを採用しました。理由は、この次のシール部の設計探査を行う際に、定量的な値は不要で、初期載荷の履歴でおおむねシール反力の傾向がつかめるだろうと考えたためです。
- 合わせこんだシール部の物性値を使い、弁体とシール接触部の設計探査を実施しました。設計変数では、シール部の構造に関わる設計変更可能な箇所を設計パラメータとしました。構造解析では2次元軸対称モデルとし、バルブを開から閉にした後、バルブ性能を測るための試験を模擬して内圧を与えました。
本来であれば漏れがないバルブを開発するために、解析によって漏れ量を直接求めることができるのが理想です。しかし、そのためには流体構造連成解析などを考慮した複雑な解析が必要であり、解析コストが高くなるため設計探査には向きません。また仮に漏れ量を直接解析すると定量的な議論になってしまうことから、漏れ量を代替可能な性能の評価として考えることが重要だと考えています。そこで制約条件としては、閉切時のシール反力が初期設計シール反力より大きいこと、正圧時と逆圧時のシール反力が閉切時のシール反力よりも大きいこととしました。 - こちらは、modeFRONTIERで設計探査した結果です。散布図マトリクスの黄色が制約条件を満たしていない条件、黄緑色がパレート解です。これら分布からバックアップリング体積はほぼ影響せず、閉切時のシール反力と正圧時・逆圧時のシール反力差がパレート解となっていることがわかります。また、制約条件を加えることで右下方向の選好解を選ぶことが可能となりました。実際にはここから設計限界を考慮して設計変数を決定しました。もちろんこれ以外にいくつもの設計探査を実施しましたが、ここでの説明は省略させていただきます。
解析と設計探査によって最大口径を約2.6倍にした目標値を達成見込み
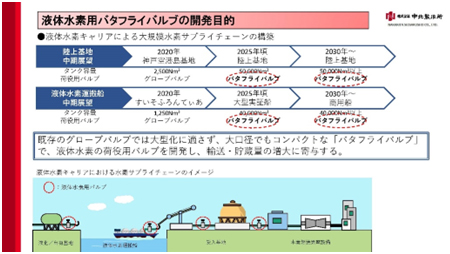
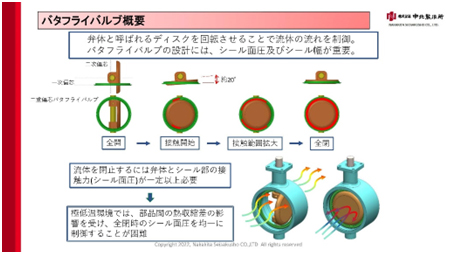
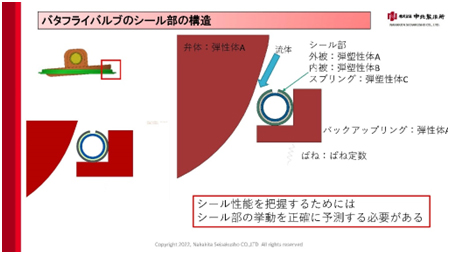
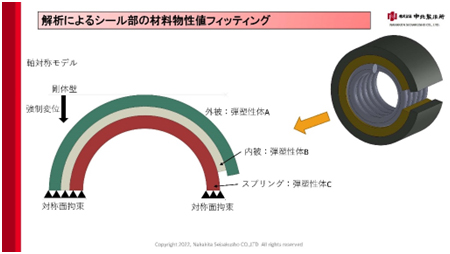
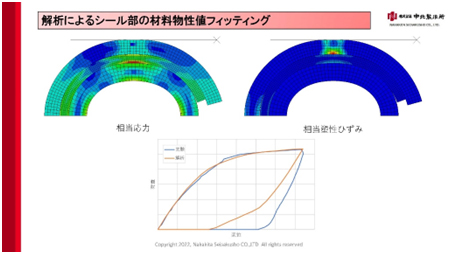
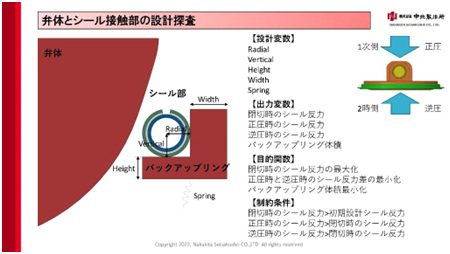
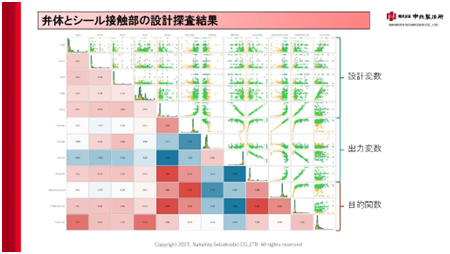
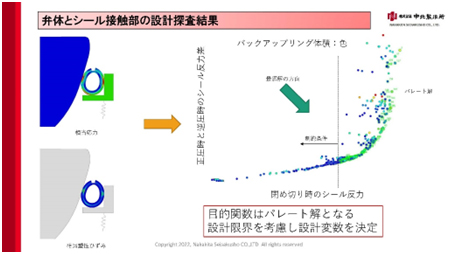
設計開発の膠着を設計探査ベースのアプローチで打破。 設計空間における最大性能到達に目途が立った。
- 詳細なご説明をありがとうございます。その他のご業務おいてどのようにmodeFRONTIERをご活用いただいていますか。
- チョークフロー弁は、私が入社する以前から開発プロジェクトが始まり、弊社の既存製品のいずれとも形状が異なるため、形状候補を漏れなく抽出するのに時間を要し、これら作業がプロジェクトの大半の工数を占めていました。この状況から改めてプロジェクトを推進するために、流体解析ツールとmodeFRONTIERで設計探査をベースに性能に対する設計変数の寄与を把握することで、今期中には形状と性能到達にめどが立ち、製品化にまで持っていけそうだと思っています。
- チョークフロー弁の開発におけるCAE活用のポイントを教えていただけますか。
- 一般的な調節弁は弁体を動かして、その流路面積を増やしたり減らしたりすることで、流量を増減させます。その流量は面積によって変化しますが、圧力によっても変化します。この一般的な調節弁では、圧力と弁体を動かしている位置での差圧の監視が必要です。
差圧が大きければ大きいほど流量は増えるのですが、流体が音速に達するとそれ以上流量が増えなくなる、つまり“チョーク”した状態になります。この特性を利用して、差圧を監視せずとも流路面積だけで流量を変えることができるのがチョークフロー弁です。チョークフロー弁のメリットは、チョークフロー弁単体の開度制御のみで流体を制御できるところにあります。一方で、チョークしていなければ本製品の前提が崩れてしまいますので、流体を効率的に流し、いかにしてチョークさせるかというところに、設計上の難しさがあります。
流量は流路面積を大きくすれば増えますが、チョークしているかどうかを実験で確認するとなると、バルブの中は見えませんから複数回の実験を通して流量を比較することで確認します。解析であれば、バルブの中を可視化でき、チョーク状態と非チョーク状態を再現することで、形状の変更による影響を探索することができます。実験できるのは、1回あたり約半日かかるケースをせいぜい数十ケース程度ですが、解析なら1日で数百ケースの計算ができます。これこそが解析の大きな強みです。
このチョークフロー弁の開発プロジェクトは、設計変数がどう効くのかわからずに、一から開発・設計がスタートしていますので、設計変数が非常に多いのです。弁の外部・内部の形状だけでなく、内部のパーツの形状とその角度など、それらを3通りずつ組み合わせるだけでも数千ケースに達します。もちろんそれらすべてを網羅する必要はありませんが、設計空間全体で傾向を見るには、数百から数千ケースの探査は必要になってきますね。
もちろん私が入社する以前からこの開発プロジェクトではCAEを利用していました。しかし、設計探査ベースの開発方法ではなかったため、一品一葉に、一度計算しては結果を確認し、また少しパラメータを変更して計算するということを手作業で繰り返してきました。これでは自ずと計算数が限られてしまう上に、有効な設計変数の特定や内部現象の考察が不十分なまま、計算結果だけを見て、モデル同士の評価にとどまっていました。つまり性能目標を達成するための性能設計が不十分な中でプロジェクトが進行していきました。 - 今回、modeFRONTIERを活用し、1年をかけて数十万通りもの計算をしました。また、modeFRONTIERの設計探査により有効にデジタルツールを活用して開発してきたため、このプロジェクトの一旦の区切りとなるような結果に到達できる見込みが立ちました。
設計の変数は十数通りありましたが、設計探査にあたっては、単純モデルから複雑モデルへ推移させるため、数個の設計パラメータで探査し、そこから寄与のある設計パラメータを抽出して、すこしずつ形状の複雑さを増していきました。設計探査ベースで開発するには闇雲に計算して最適解だけを追うのではなく、設計原理を考えて分析し、プロセスに着目し、なぜこのような現象になるのか、それにはどのパラメータが効くのか、効く理由は何かという、現象の本質を思考できる能力が必要です。実はこの設計を担当したのは、新卒入社2年目の技術者ですので、読者のみなさんも設計探査の観点を持って設計に臨むことの重要性をご理解いただけるのではないかと思います。
このように我々エンジニアの思考をサポートしてくれるmodeFROTIERの機能の中で、個人的に気に入っているのがCAP機能で、よく使っています。まずは漠然と解空間を眺めて、それのどこが変化するかを気づくために動的に見るようにします。
ハイエンドのソフトウェアは、機能面ではもう大抵自分が思い描いたことができますので、解析専任者であれば機能を理解して自分の手足のごとく使えることが前提です。その上で、設計探査ベースで開発するのですから、私の経験においても、弊社においてもCAE関連のソフトウェアの中でmodeFRONTIERの稼働率が一番高くなります。設計探査ベースで開発するために設計探査を使いこなそうとすると必然的にそうなります。 - 新卒入社2年目でここまでの成果をあげられたことには感心するばかりなのですが、CAE技術を活用できる人材育成という観点から何かアドバイスいただけますでしょうか。
- もともと彼は学生時代に流体解析を経験してはいましたが、商用のCFDツールやmodeFRONTIERの利用経験はありませんでした。CAEの教育というと、解析作業やソフトウェア操作を教育として与えがちですが、実は私がソフトウェアの操作を教えたことはほとんどありません。彼は自分で調べるのがとても速いんです。私なら技術サポートに問い合わせするようなことも自分で調べています。したがって私は専ら、現場で起こっている状況をどう解析に結び付けるか、解析モデルに置き換えるか、計算結果をどう分析するか、現象と解析結果をどうつなげるか、解析結果をものづくり現場にどう返すか、現象論との関連性、設計パラメータの設定、モデルの単純化など、教えたというよりは、私も一緒に考えながら進めてきました。私も当然チョークフロー弁の開発経験はありませんので、その点では私と彼のスタートは同じです。しかし設計探査の解釈には、技術者各人の価値観や力量が現れます。恐らく唯一の解って無いだろうと思っていますので、その考え方や解釈の違いを確認しながらケースバイケースで、解析結果と開発とをどう結びつけていくかを様々な角度から議論する、それを通して教育していくことを心がけました。
- 少し視点を変えまして、CAEツールの導入効果を社内に示すために、どのような活動をされているか教えていただけますか。
- そうですね、各部署とのコミュニケーションを図ることに尽きるのではないでしょうか。メーカーの解析技術者は、計算だけをしていれば成果が出せるかというと残念ながらそうではなく、解析結果をものづくりの現場が活用でき、ものづくりのQCDが改善できて初めて効果を発揮します。ものづくり現場に対しては、解析結果をただ単に伝えるのではなく、どこをどのように加工すると良くなるのかを具体的に説明し、指示を出しています。経営者や管理者に対しては、会社が投資したツールや解析技術者の工数などの投資に対して、解析が直接利益を生まなくとも、解析によってどれほど開発が加速したか、なんらか製品が良くなっていることに対して、解析がどのように寄与して、いかほどの改善や目標アップにつながったかを説明する責任があると思っています。
解析で定量性を求めることはもちろん可能ですが、その定量性を追い求めて厳密に何回もの実験をして、バリデーションを繰り返してというように、それらにコストをかけるよりは、設計探査で80%まで完成度を引き上げ、残りの20%を現場技能者に補ってもらうというところまで、緊密なコミュニケーションを解析担当者自身が取れるかどうか。つまり、優秀な現場の技能者が持つ経験や勘が十分に発揮されるところまで設計探査の技術を高めることが、解析が効果を発揮する最良で最短の方法だと考えています。 - 社内の別の立場の方々に伝えるのではなく“伝わる”ようにコミュニケーションを図ることが重要なのですね。
今後のデジタライゼーションに関してお考えがあれば簡単にお聞かせいただけますか。 - 設計探査をベースに開発を進めるという方針に沿って、この技術を横展開し、来期以降は次の製品開発に取り組むことになります。またデジタイゼーションからデジタライゼーションへと移行させるべく、設計の自動化にも着手していますし、設計仕様を入力しボタンを押せば最適形状を作ってくれる設計者向けシステムの構築も十分に実現可能だと考えています。
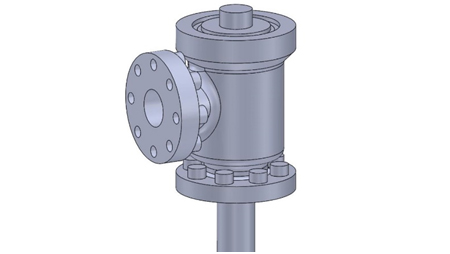
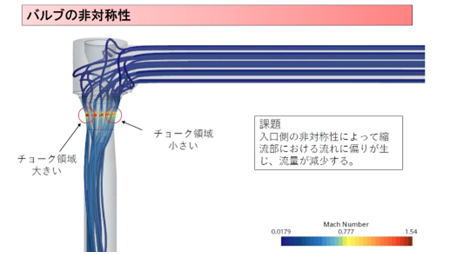
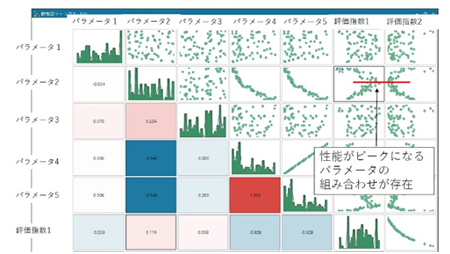
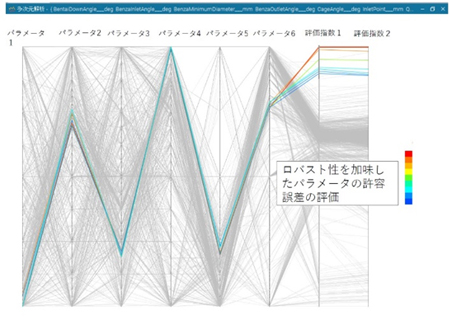
省略
このインタビューの詳細は季刊情報誌IDAJ news vol.112でご覧いただけます。
ユーザー登録済の方はユーザーサポートセンターからダウンロードできます。
ご活用いただいている製品
- 分野1:
- 熱流体解析、構造解析
- 分野2:
- 最適設計