日本精工 様(IDAJ news vol.107)
デジタルツイン推進にあたって軸受の疲労強度、剛性評価等に社内標準ツール「SIMULIA® Abaqus Unified FEA」をご活用
日本精工 株式会社
コア技術研究開発センター 様
IDAJ news vol.107お客様紹介コーナーより抜粋
発行日2022年3月
解析種別:デジタルツイン、Digital Transformation 、 DX 、軸受、ベアリング、ハブユニット
課題等:カーボンニュートラル、疲労強度、剛性評価、トポロジー最適化、耐久性、軽量化
省略
非解析専任者がデジタル技術を活用するために必要な機能と操作性を備えたAbaqus
- リアルを重視した御社独自のデジタルツインの推進が本格化しているのにはこのような背景があったのですね。
さて、日本精工様には弊社から熱流体解析ツールをご導入いただいたのをきっかけに20年以上にわたってお取引をさせていただいております。そして2年ほど前からは構造解析ツールとしてSIMULIA Abaqus Unified FEA(以下Abaqus)を弊社からご導入いただいています。Abaqusをご選択された理由をお聞かせいただけますか? - 当室に異動する前は、ハブユニット軸受の開発において構造解析ツールを使ってきました。このハブユニットは軸受に加えて、ブレーキディスクやホイールなどを取付けるためのフランジをユニット化した製品で、この性能評価を適切に行うには、ハブユニット軸受単体だけでなく、ブレーキディスクやホイールなどを含めたアセンブリ解析まで実施する必要があります。この強度や剛性などを、Abaqusを使って計算してきました。Abaqusは、CATIAと親和性が高く、モデルの入出力が比較的容易で、収束性を自動的にコントロールできるため、非解析専任者がオペレーションしたとしても結果を得ることができます。アセンブリ解析においては、多数の接触部位が生じますので、接触している部位の収束性を損なわず、精度を保持したままコントロールできるのはツールとしての強みだと思います。これは、研究だけでなく設計工程へ適用するのに有益であると考えます。またシミュレーションを高精度化していく過程においては、大規模モデルへの対応が求められます。それには並列化やGPGPUが活用できるソフトウェアであることも大切です。さらに複数部門の設計工程に組み込むために、ユーザーサブルーチンを使ったカスタマイズ、スクリプトによる作業の自動化が可能な点も大きなメリットですし、疲労寿命予測ツールfe-safe、形状・位相最適化ツールToscaなどといった周辺ツールの充実も、高度な解析には欠かせないと考えています。
- 「接触と言えばAbaqus」と言われるほど、洗練された接触アルゴリズムが特長の一つですので、複雑な解析に取り組まれている御社には最適なソリューションではないかと思います。
早速、Abaqusをご利用いただいた事例をご紹介いただきたいと思いますが、せっかくの機会ですので、ここで簡単に”ハブユニット軸受”の構造についてご紹介いただけますか? - ハブユニット軸受は、車両メーカー様が開発されてきたブレーキディスクやホイールなどを取付けるためのフランジと一体化した軸受で、自動車の車輪を支える製品です。このハブユニット軸受に求められる機能や性能は、自動車の基本機能としての過酷な環境下でも故障しない耐久性や耐水性などの信頼性です。重大な損傷が発生した場合は、大きな事故につながりかねない故障モードとなります。地球環境に対しては、燃費軽減・CO2削減、エネルギー回生の効率化、EV化に対応するための低フリクション化と軽量化、乗員や歩行者などの安全・快適性に対しては、快適な運転(註:操安性)や自動運転の支援のための応答性や剛性が求められます。
このハブユニット軸受の設計工程は、軸受内部の仕様設計とユニット構成部品設計の大きく2つにわかれます。お客様から頂戴する取り付け寸法や周辺構造などの情報、車両諸元、軸重、タイヤの大きさ、旋回条件などを元に、軸受内部の玉のPCD(註:Pitch Circle Diameter)や大きさ、溝Rなどの寸法がどうあるべきかという内部仕様設計を行います。続いて、ハブフランジ部の形状を検討し、それらを図面化、試作した後に台上評価や車両評価を行います。 - 複数の車両メーカー様の、搭載車種ごとに異なる使用条件や要求仕様がありますので、これらを試作と試験を繰り返す従来型の手法で開発していては、国際競争力の低下を招きかねないとご判断されたわけですね。デジタル技術を取り入れた設計手法にはどのような価値があるとお考えですか?
- 広く言われている通り、設計開発のVプロセスの右側、弊社では、試作後の軸受単体評価や車両評価での手戻りの発生が懸念されます。ハブユニット軸受は、鍛造などの過程を経て作られますので、手戻りが発生すると開発期間の遅延やコスト増大という非常に大きなデメリットを被ることになります。そこで、設計段階においてシミュレーション技術をフル活用し、小さなV字プロセスを机上で回すことで、最終的には一度の試作で満足する評価が得られるといった理想的な状態に近づけることができるものと思います。さらに、より良いシミュレーションを実施することで性能の定量的な評価が可能となり、より最適な仕様の製品開発につなげることができればと考えています。
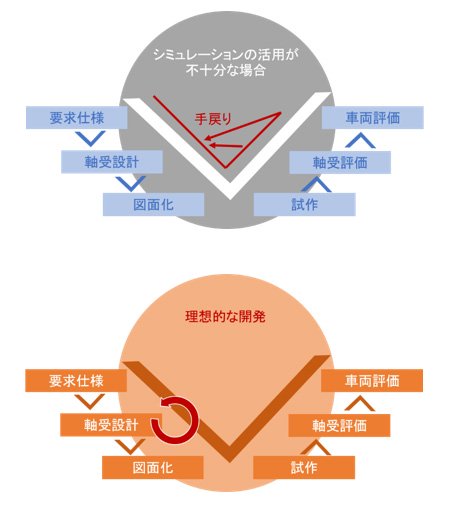
デジタルツイン推進のための標準化と設計工程への適用
~Pythonによる作業自動化で解析精度を保持しつつ、数時間の手作業を数分に短縮~
- 開発の効率化やコスト削減は企業経営に貢献し、また設計開発に対する様々な示唆を与えるという点で、ほとんどの企業においてシミュレーションが活用されている理由だと思います。特に御社のように、顧客課題に沿ったソリューションを提供する場合は、必須の技術だと認識しております。
それでは、Abaqusを適用した事例をご紹介いただけますか? - ここでは、ハブユニット軸受のフランジ部の疲労強度解析についてご紹介します。
ハブフランジには、路面からタイヤに伝達される路面の反力を伝達する過程で、ホイールの変形、ブレーキディスクの変形、フランジの変形を繰り返すことで発生する応力の負荷に対する疲労損傷を評価しなければなりません。従来は簡易的な構造解析をメインに使ってきましたが、精度の面で課題がありました。そこでAbaqusでのアセンブリ解析による応力算出からfe-safeでの破損部位と寿命を予測するというフローを構築することで、シミュレーションによる机上耐久試験が実施できる体制が構築できるのではないかと考えました。
応力解析では、軸受、ブレーキディスク、ホイールが締結された状態を表現、締結軸力や部品間の接触などを定義します。また回転しながら使われるという製品の特性上、回転荷重として境界条件を入力します。Abaqusで応力解析を行った後に、fe-safeで疲労解析を行うことで破損部位や寿命予測を行います。 - 解析モデルの作成にあたっては、軸受の転動体荷重が非線形性を持つため、前もって内製の専用ツールで荷重を計算します。求めた荷重をAbaqus CAE上で手入力すると、かなりの条件数を転記しなければならなりません。そこで内製ツールとAbaqusをPythonのスクリプトで繋いで、この作業を自動化しました。
入力条件を設計者が設定し、内製ツールのモデルを自動的に生成・計算、その計算結果を抽出してデータの集計を行った後に、Abaqusに入力できるような形に座標変換します。そのデータをAbaqus CAEのPythonインターフェースを介して自動的に入力できるようにすると、数時間の手作業を要する処理を、わずか数分で完了できるようになりました。
計算したフランジの応力解析結果を確認すると、主に転動体の反力が発生している部位である転動体負荷圏と呼ばれる場所で、転動体の荷重が回転するのに伴って、高応力部位も一緒に回転することが確認できました。この結果から、回転荷重を与えることで、最弱部位を網羅的に探索することができるようになります。算出された応力値については、実機の歪測定結果と比較することで、モデリングの範囲や方法の妥当性を検討しました。
続いて、fe-safeによる破損部位の予測と耐久試験結果を示します(図4)。左側が実物を使った耐久試験の結果で、耐久試験後に浸透探傷を行って、発生した疲労き裂を染色しています。この薄く赤い部分が発生した疲労き裂です。右側は、fe-safeによって得られた耐久寿命予測結果で、締結用のボルトを挿入する穴の左上に赤い表示が見えますが、ここが短寿命で、疲労損傷が予測される部位です。左右の結果を比較すると、実際に疲労き裂が発生した部位と一致することがわかり、予測に成功したものと判断しました。したがって、この一連の手法を活用することで、フランジ形状の設計検討に有効であることが確認できました。
簡易的な構造解析や過去の評価試験や経験から、高い応力が発生している部位はある程度まで絞り込むことができますが、本質的に現象を理解できていないのではないかという不安が残っていました。燃費を向上させるためには軽量化が必須の技術となっており、それを達成するには、軸受の安全率を確保しながらさらにシビアな設計をしなければならなくなっていますので、現象の適切な理解にシミュレーションを使った予測が重要なことがわかります。 - このような解析を行うには、比較的大きな計算モデルを扱う必要がありますが、それに必要な計算リソースを同時に検討しました。
8並列で行った計算時間を1とすると、今回のケースですと、16並列にすることによって約30%強の削減効果が認められました。これにGPUを追加すると、さらに30%以上の削減効果を積み増すことができ、トータルでは半減させることができるという結果が得られました。
このように、CPUやGPUを導入に対して、非常に効果が出やすいソフトウェアであるということがわかりましたし、またGPUは、使用するトークンがCPUの並列化に比べて比較的少なくて済みますので、費用対効果が特に大きいということも確認できました。今回の検討結果を踏まえて、日常的な設計業務での大規模な運用を見据えた解析インフラの増強を計画しています。 - どうもありがとうございます。設計工程へ組み込むには、機能や精度だけでなく、現実的に許容できる範囲での計算時間も重要ですね。現在は、そのための解析手法の開発も行っていらっしゃるとお聞きしております。簡単に内容をご説明いただけますか?
- いくつかの解析手法の開発と標準化に取り掛かっています。その一つが、ハブユニット軸受の剛性解析です。ハブユニット軸受は、走行中に路面から反力を受けます。それに伴ってタイヤやホイール、ブレーキ、ハブユニット軸受が変形し、車両特性に影響を与えることがあります。ハブユニット軸受の主な変形部位はフランジや転動体と軌道面の接触変形です。これらの部位の剛性値が十分最適になっていないと車両操安性が悪化しますので、足回り設計に深く関わります。そこでタイヤの荷重入力点を模擬し、治具にハブユニット軸受を取り付け、剛性評価試験を行うのですが、これらをシミュレーションで再現します。
このシミュレーションのポイントは接触解析の効率化にあります。と言いますのも、軸受の転動体と軌道輪の接触というのは、非常に小さな接触面積を持ち、高面圧であることが特徴です。乗用車サイズの軸受を例にすると、軸受の接触面は幅1mm程度、縦数mm程度で、この非常に小さな領域に数ギガパスカルもの高い面圧が発生します。これをAbaqusでシミュレーションするには、ソリッド―ソリッド接触のフルFEAを実行することになりますが、高精度な計算のためには、メッシュ数が増え、計算コストの増大は避けられません。これを避けるには、接触剛性をHertz剛性とした上で、バネを設置する方法がありますが、バネは点で接続するため、節点の変形が局所的に大きくなり、結果的に計算精度が悪化するという課題がありました。そこで、ユーザーサブルーチンで、ユーザー定義要素(註:UEL)を適用しました。基本的な構造はユーザー定義要素そのままですが、節点変位をユーザー定義要素に入力して、内部で内製剛性解析プログラムを用いて荷重を計算し、それを剛性マトリックスの節点荷重としてフィードバックする仕組みです。これを用いて、メッシュ数の多いFull-FEAモデルとメッシュ数を抑えたUsub-FEAモデルで検証計算を実行しました。実測値とUsub-FEAモデルの計算結果、Full-FEAの計算結果を比較すると、良好な一致が見られ、高精度に計算できたことが確認できました。気になる計算時間も、Full-FEAモデルに比べるとUsub-FEAモデルの計算時間は約10%程度で、9割の削減効果を得ることができました。
このユーザーサブルーチンを応用して、圧痕解析にもトライしています。路上を走行中に車両が路上の穴や縁石、落下物などに衝突したり、高速で乗り上げることで大過重を受け、ハブユニット軸受の軌道面に圧痕と呼ばれる穴のようなものが生じることがあります。車両の走行は可能ですが転動体が周期的に衝突を繰り返すと、振動や異音が発生し、ドライバーが不快に感じる不具合モードにつながることがあります。そこで、先ほどご説明した剛性評価の手法を応用して、圧痕の発生具合を評価しようとしています。
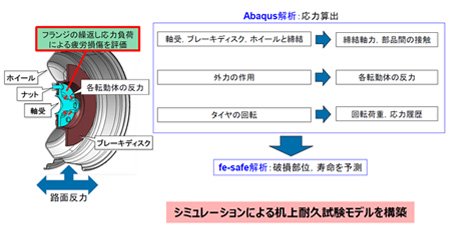
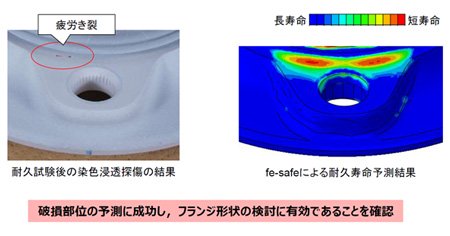
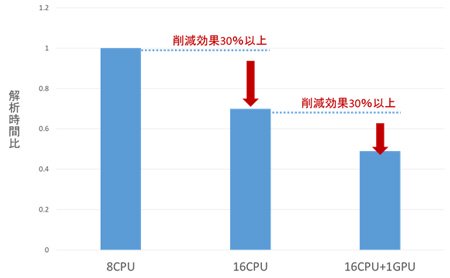
構造解析の社内標準ツールAbaqusの解析手法開発、技術蓄積、設計者展開に着手
- 日々の設計業務への適用を常に念頭におき、シミュレーションでの評価の標準化や効率化を取り組まれているご様子がよくわかりました。今後のシミュレーション技術の展開については、どのようなお考えをお持ちでしょうか?
- 弊社がデジタル技術において重要視しているのは、現象を適切に理解し、台上試験で起こっていること、マーケットで起こっていることを計測・可視化することで、その結果をモデル化や解析手法に反映させ、解析に必要なインフラを整備することによってデジタル化を推進することです。解析インフラは、GPUやストレージなど随時整備し、現状では4~5年前なら研究所でのみ行っていた大規模な計算を、設計者が通常業務で活用できる体制を構築しました。これによって、製品開発の効率化、より最適な製品開発につなげたい考えです。
数年の準備期間で、各技術部門が持つ技術課題を分析し、弊社製品群においては構造解析のニーズが一番高いことがわかりましたので、優先的に取り組んでいます。構造解析領域では、弊社の内製ツールとあわせて、Abaqusを社内標準ツールとして展開することになりました。Abaqusは、設計担当者が気軽に非線形有限要素法解析に取り組むことができ、いくつかの検証事例では、実測と解析の良い相関が得られています。Abaqusと内製ツールを連携させることで、計算コストを抑えつつ、高精度なシミュレーションを実施したいと思います。そのために、現在はAbaqusを用いた解析手法の開発、活用事例の蓄積、設計者への展開を推進しているところです。 - Abaqusを標準ツールとしてご選択くださいまして誠にありがとうございます。御社の成果につながるよう弊社もできる限りご支援させていただきます。
省略
このインタビューの詳細は季刊情報誌IDAJ news vol.107でご覧いただけます。
ユーザー登録済の方はユーザーサポートセンターからダウンロードできます。
ご活用いただいている製品
- 分野1:
- 構造解析