本田技術研究所 様(IDAJ news vol.96)
歩行者保護性能評価業務の効率化とさらなる技術深耕のためにAIコンサルティング・サービスをご活用
株式会社 本田技術研究所 四輪R&Dセンター 様
IDAJ news vol.96お客様紹介コーナーより抜粋
発行日 2019年6月
解析種別:構造解析、形状最適化
課題等:歩行者保護性能、深層学習、予測精度、教師データ
省略
- 今回は、最近、世間的にも特に関心が高いAIに取り組まれた事例についてご説明いただければと思います。まずは、それに着手された動機などを簡単に教えてください。
- 我々の主な業務は、量産開発と安全性能向上のための研究開発になります。そこで、AIを使って量産開発業務にかかる工数を削減しつつ、安全技術の研究に注力できるような仕組みづくりを目指しています。また、これまでとは異なったアプローチを取ることによって新しい技術開発のための様々なヒントが得られるのではないかという期待もあります。もちろん、AIという新しい分野ですので、活用するためには様々な課題があることは承知していましたが、創出された時間を技術検討に使うためには大変有用な技術であると考え、導入の検討を決意しました。検討開始当初は、AIを使うと解が自動的に導出されるためエンジニアが考えなくなるのではないかといった懸念がありました。しかし、検討が進むにつれてAIは自動化の側面がある一方で、様々な解の可能性を提示できるようになるため、エンジニアはより深い考察ができるようになりつつあるのを感じています。
また、こうしたAIの活用にチャレンジすることは、次世代の安全技術構築のためにも大切だという上司の理解も得ることができました。もちろん、目標値が設定されていたり、何らかのアウトプットは求められますが、それは当然のことですので障害ではありません。今は、一緒にこの新しい技術を開発し、賛同してくれる仲間を増やしているところですね。
「ボンネットフードの形状最適化」は「きゅうりの選別」に通じる?!
- 早速ではございますが、AIへの取り組みについてご紹介ください。
- 2018年のESTECO社のユーザー会では、歩行者保護に適したボンネットフード構造を探索するために形状最適化に取り組んだ事例を発表しました。この発表を踏まえて、その後のGTC(註:NVIDIAユーザーイベント「GTC JAPAN 2018」)では、AIを適用した事例をご紹介しました。
通常、形状最適化の後には、応答曲面を活用して設計を効率化するステップが考えられますが、ある技術課題に直面したため応答曲面ではなくAIを用いました。 - 技術課題とはなんでしょうか。
- 意匠部品であるボンネットフードは、その構造が車のスタイリングに依存します。そのため、スタイリングが異なることでトポロジーが同一にならないことが多く、最適化計算における共通の設計変数が存在したり、無かったりすることがあります。これまでの知見では、これを応答曲面で表現することができず、どうしたものかと考えていました。そんなときに、世間で話題になってきたAI技術に興味を持ち文献を調べてみると、深層学習は特徴量(註:≒設計変数)の設定をしなくても回帰や分類などの予測ができるということを知りました。それならば一度、深層学習のアプローチを用いて応答曲面的な使い方ができないか検討してみようということになったのです。ボンネットフードに限らず、現実にはこのような設計課題は多いのが事実です。弊社は以前から、IDAJのコンサルティング・サービスを利用していますので、定期的に技術的なディスカッションの時間を設けています。その中で、IDAJのエンジニアから「きゅうりを選別するAIの開発」に関する話題を提供いただき、「勘と経験で成り立っている農家でのきゅうりの等級を選別する仕事というのは、深層学習の活用に適している」と聞いたときに、”ひっかかる”ものがありました。ボンネットフード設計は、CAEを活用して性能検証をしていますが、実は、私のように10年以上も担当していると、形状を見るだけである程度までは、なんとなく性能を目利きできるようになってくるんです。これは、まさしく「きゅうりの選別じゃないか」と(笑)。
歩行者保護の観点からベストの解であっても、剛性の観点からはベストの解ではない。だから今度は、歩行者保護、剛性の両方の観点からベストな解を探して、複合的に解を探索しようとしてみましたが、それでは限界があるように感じました。いわゆる、複合最適化も良いアプローチなのですが、すでに性能評価をクリアした既存の形状を教師データとすれば良いのではないかと。そこで、機械学習させた上で各種条件を再現するという技術にトライしはじめたわけです。
比較的早い段階からAI活用したいとは思っていましたので、エンジニアリング領域で協業させてもらった実績があるIDAJに依頼し、一緒に技術構築を進めています。
1機種あたり約40時間の性能予測を10秒に短縮
- 弊社も一緒に取り組ませていただくことでAIに対する知見を得ることができ、非常に良い経験となっています。
- 私の部署の場合、新技術構築のゴールは、常に量産開発に適用できるようになることです。その意味では、開発ツールとして問題なく適用できるよう、AIの予測精度を上げ切りたいと思っています。また、最終的にはAIが類推した結果が、なぜそうなったのかということを可視化できるようにしたい、これは今後の研究対象ですね。
量産開発に使用するツールにするまでが私ども仕事ですから、ただの研究で終わるわけにはいきません。量産開発で使えるものに仕上げて、実際に現場で使わなければ、次の研究にもつながらないと考えています。 - ここからは簡単に、歩行者保護性能予測のために構築されたサロゲートモデルについてご紹介いただけますか。
- 交通違反の罰則強化や安全装備の普及などから、交通事故における死者数は減少傾向にあることが広く知られています。一方で、近年の交通事故死者割合では歩行者が多くを占めており、さらなる交通事故死者数の低減には歩行者保護が重要になってきています。歩行者の事故は頭部の損傷が原因で死亡することが多いことから、自動車メーカー各社には、歩行者の頭部保護性能を高めた自動車の設計が求められています。
歩行者の頭部損傷の多くは、自動車のボンネットフードに衝突することで発生します。歩行者保護性能の高いボンネットは、歩行者の頭部が衝突した際の衝撃を吸収できるように柔らかければよいのですが、ボンネットの下にはエンジンがありますので、一定の空間が必要です。しかし、エンジンにぶつからないようにボンネットの下に空間を持たせようとすると、スタイリングが犠牲になります。エンジンにぶつからないよう、適度な硬さのボンネットにしなければなりません。つまり、歩行者保護性能を左右するのはこのボンネットフードなのです。 - ボンネットフードは、自動車のスタイリングによって外形形状が変わりますので、様々なボンネット裏の形状が存在します。そのため、ボンネットは設計を共通化することが難しく、モデルごとに歩行者保護性能の検証が必要です。当然、設計初期の部品への性能割付や設計ガイドなどがあるのですが、完璧なものがあるわけではないので手戻りが発生します。ベテランエンジニアであれば、過去の設計の経験や勘を生かして形状からおおよその性能を予測し、設計を進めることができるため手戻りが比較的少ない。しかし、経験の少ない新人エンジニアの場合は、CAE計算を実施しなければ構造の確からしさがわからないので、多数の対策シミュレーションを実施してようやく要求を満たす設計に到達することになります。
1つのフード構造を検証するには、CADデザインに1週間、解析メッシュ作成に1週間、境界条件の設定に2~3日、計算処理に約40時間を要します。この一連の作業に機械学習を活用した構造のあたりづけを行うツールを作成し、CAEを使わずに性能評価ができるようなエージェントを構築することにしました。 - 教師データの数はいくつ準備されたのでしょうか。
- 学習用教師データには、過去に歩行者保護試験に関わった29機種分1,977打点を準備しました。検証データには、ミニバン、SUV、セダンというボンネットの面積が異なる3機種269打点を使用しました。それぞれの打点のHIC(註:Head InjuryCriterion 頭部傷害基準)から全体の得点を算出し、歩行者保護性能をAIで予測した結果とCAEで解析した結果とを比較しました。AI精度の目標は、CAEとの得点誤差5%以下、HICカラーマップの一致度80%以上です。
- その結果、得点の誤差はミニバン5%、SUV4%、セダン4%、またHICカラーマップの一致度はミニバン80%、SUV81%、セダン76%でした。一般的に学習用教師データは数多く必要だと言われていますが、本例のように使用できるデータがある程度限られていたとしても、一定の精度で予測できることがわかりました。それだけではありません。これまで1機種あたり約40時間かかっていた性能予測時間を10秒程度にまで短縮することもできました。ただし、これは開発初期段階の参考情報としています。最終的には従来通りの大規模シミュレーションやテストを実施して性能を確認します。
- 今回のお取り組みの中で、ご苦労されたことはどういったことでしょうか。
- 苦労したことといえば、何といっても教師データを集めること、いえ、”発掘したこと”と言ったほうが相応しいかもしれません。もちろん各機種の図面データは保存してありますが、CAE結果は消去したものがほとんどでした。したがって、1,977打点の6~7割は、CAEの再計算を実施したわけです。モデルを作り直したり、部分的にはデータをサルベージしたりと・・・。10年前に設計した時点で、まさか将来的に機械学習で使うとは思ってはいませんでしたから、そういう観点でデータを整理したり管理していませんでした。教師データとして使うために、まとまったデータにするまでが本当に大変でした(苦)。
当初、PoC(註:Proof of Concept)には、6機種のデータを使っていたのですが、それではやはり限界がありそうでしたので、最終的に29機種まで増やしました。この1,977打点での検証で、一定の精度が確保できましたので、この検証自体が一つの知見となりましたね。
また、新しい領域に取り組むときにつきものなのが、先が見えない、予測しきれない辛さがあります。CAEであれば、CAE結果とテスト結果が合わないなら、現象を注意深く観察することでモデルの再現性やテストの結果などに問題があるのではないかという仮説を立て、それを検証していくことで修正が可能です。しかし、AIでは精度を上げるための方法が簡単に見つからないことが多いです。これはもう、できることを一つずつ試していくしかないと地道に取り組んだのが成功の秘訣と言えるかもしれませんね。
最初はCADデータのスクリーンショットの画像を教師データとしていましたが、それでは精度が40%程度にまでしか上がりませんでした。CADデータには、CADデータ特有の陰影が描かれますので、これが適切ではないのかもしれないと考え、定量的な情報でデータを取り直すことで精度を上げることができました。図4で示したように、4枚の画像を使ったのですが、Diff画像を使うと精度が10%ほど上がりました。Diff画像は、ボンネットフードの表側と裏側の差分画像を取ったものです。確かにボンネットの奥行きは、HICに大きく寄与する部分ではありますので、この2次元画像から疑似的に距離を画像で表現し、構造の類推まで可能なのが深層学習の不思議なところでもありますね。
恐らく機械学習の精度を向上させるための方法は、様々な論文や技術資料で述べられることが決してそのすべてではなく、そこに書かれていない様々な細かいテクニックがあり、それらが積み重なって精度を上げることができる、このノウハウの構築こそが機械学習の精度向上のポイントとなるのかもしれません。
私は歩行者保護が専門ではありませんので、ボンネットの裏表の差分を取った画像が重要だという発想を聞いたときには、歩行者保護のエンジニアでないと思いつかない手法だと思いました。機械学習の教科書に書かれている通り、”特徴量は多いほど良い”ということですね。
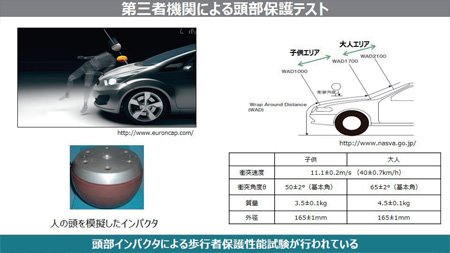
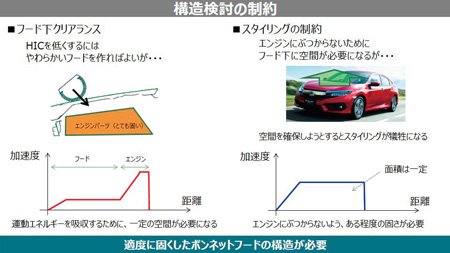
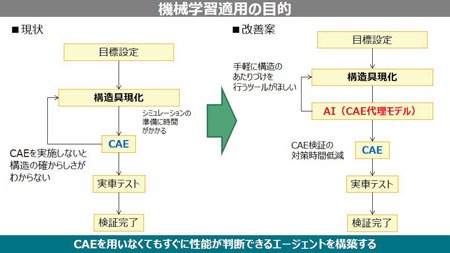
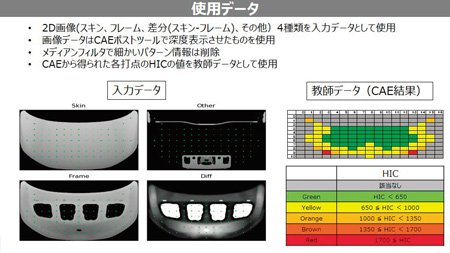
各種技術構築のゴールは、量産設計への適用
- 先ほど、精度をさらに向上させるとおっしゃっていましたが、どのような取り組みを予定されていますか。
- 実は、ボンネット外周部が特に精度が低い領域であるとわかっています。この外周部は、HICの値が高いことがわかっているのですが、通常、量産車はできるだけHICが低い領域を多くとれるように設計されるため、高いHICのデータが少ない状況にあります。つまりデータ数が偏っているため精度が上がらないわけです。そこで、CAEとAIの誤差をなくし、近い将来には量産モデルへも適用できるようにしたいと考えています。
- GTCでのご発表以降、弊社主催のIDAJ CAE Solution Conferenceでも深層学習を用いた歩行者保護性能の予測についてご講演いただきましたが、こちらは、どのようなモチベーションで開発された技術でしょうか。
- GTCで発表したような開発を進める中で、構造検討をAIでサポートできるのであれば、今は当たり前にやっている別の作業も、AIでサポートすることによってプロセスを見直すことができるのではないかと考えるようになりました。そこで、設計現場と色々と話をするうちにAIの適用可能性が高い別のテーマをみつけることができました。
ボンネットフードの各打点におけるCAEと実機テストは、加速度の波形がおおむね一致します。しかし、評価指標であるHICの計算式には、2.5乗の項が存在するため、波形がほぼ一致していてもHIC値がずれることがあります。また、ガラスのように一部の打点のおいては、CAEでの再現が難しいことから波形自体の特徴が異なることがあります。こうした場合も、当然ですがHIC値とはずれてしまいます。そこで実際の開発では、CAEの動画や波形をよく観察して、過去の実験データも考慮しつつ、打点ごとにマージンをのせてHICを類推しています。しかし、こうした手法では、マージン値が人に依存しやすくなり、特にベテランエンジニアと新人エンジニアの間では差が生じやすいのです。経験の少ない新人は現実には発生しえないようなCAE結果を疑うことができないため、緩めのマージンを設定しがちですが、ベテランの場合は、波形や動画から実現性を的確に予測し、論理的に妥当なマージン値を設定できることが多いのです。ICSCでは、新人でもベテラン並みの分析ができるようにAIでサポートするためのプロセス検討について発表しました。
テストケースには、約1,000程度の実験データとCAEデータがそろっているデータセットを準備しました。車種数は同じですが、実験データとCAEデータがそろってないといけない。CAEと違って、テストはやり直しがききませんので昔のテストデータは本当に貴重です。さらに、波形が残っていたとしても、それがどのCAE結果と結びつくのかを調べることもかなり大変でした。検討においては教師用に8割を、評価用に残りの2割を使用することにしました。
設計現場では新人に対してCAE結果を鵜呑みにしないようにと伝えています。あるモードは再現性が難しいことが多いので、そこはモードを良く見て、実際にはどうなのかを過去のテスト結果を見て類推するというエンジニアリングをやっていますが、開発車種が変われば前提条件も異なるため決まった手法は存在しません。自分で良く観察し、過去の開発履歴から自分なりに現象を理解して、開発中の車ではこうなるんじゃないかと頭を絞るしかないのです。
こうした設計現場の実態の中で、AIでもっと賢く開発プロセスを変革できないか考えていました。そこで、さきほどのきゅうりの事例のように何か他業界での事例はないか探していたところ、異常検知や故障診断などで波形を用いている事例があり、それを使ってみることになりました。検討途中ではもちろん精度不足が発生しましたが、このケースと同様に教師データをスクリーニングすることで、CAE波形から実車テスト波形に近しい波形を類推することができました。また、最後に今回構築したモデルの妥当性も確認し、AIが波形形状とHICの関係性をベテランエンジニアと同様に習得できていることがわかりました。 - こちらは特に、データを生成するという新しい領域に踏み込まれており、世の中のどこでも取り組まれていない事例になるため大変難しいお取り組みであったかと思います。A Iはエンジニアリングにおいて極めて注目度の高いテーマですので、本誌で2つもの事例をご紹介でき大変ありがたく存じます。
省略
このインタビューの詳細は季刊情報誌IDAJ news vol.96でご覧いただけます。
ユーザー登録済の方はユーザーサポートセンターからダウンロードできます。
ご活用いただいている製品
- 分野1:
- 構造解析
- 分野2:
- 最適設計