本田技研工業 様(IDAJ news vol.119-1)
機械学習を活用した樹脂部品の繊維配向予測・反映システム構築にAIコンサルティング・サービスをご活用
本田技研工業株式会社
BEV企画統括部 開発プロセス改革部 様
IDAJnews vol.119お客様紹介コーナーより抜粋
発行日2025年3月
解析種別:AIコンサルティング・サービス、樹脂流動解析、衝突シミュレーション
課題等:開発期間短縮、開発コスト削減、予測精度向上、サロゲートモデル、 AI、機械学習、業務効率化、繊維配向予測、繊維強化樹脂、マッピングツール、自動レポート生成、GUI開発
省略
繊維配向情報の取得作業を25時間から3分に。99.6%減という劇的に短縮に成功
- 早速ではございますが、今回のプロジェクトについてご紹介をお願いします。
- 自動車開発は“こういうクルマを作るぞ”と決めてから、図面を書いて、部品を試作し、実験するという流れを繰り返して発売までこぎつけます。こういうクルマを作ると決めるときに重要なお客様のニーズは、実に様々で、かつ刻々と変化します。このお客様のニーズに合ったクルマを、旬を逃さずにタイムリーに発売したい、そのために開発期間を短くしたいというのは、すべての自動車メーカーの願いです。
そこで、時間のかかる試作と実験をシミュレーションに置き換えることが進行しています。しかし、ただシミュレーションに置き換えるだけではダメで、実車試験と同等の結果がシミュレーションで得られなければなりません。そこで、私が取り組んでいるのが、衝突シミュレーションの技術開発と予測精度の向上です。
衝突シミュレーションにおいて、厄介なのが樹脂部品です。8年ほど前から予測精度の向上に取り組んでおり、非強化樹脂の方は解決できたのですが、強度が必要な部品に特に広く適用されているガラス繊維強化樹脂が"難敵"で、繊維配向の影響を適切に反映しないと強度特性をうまく再現することができません。
図1左下は、ガラス繊維強化樹脂の三点曲げ試験で、黒線がテスト、赤線が繊維配向の違いを考慮していないシュミュレーションの結果を示していますが、全然合っていないことがお分りいただけるかと思います。 - なぜこの繊維強化樹脂が難しいのかと言いますと、樹脂の中のガラス繊維の向きによって強度が異なる異方性があるからです。図2左上段の白い棒が繊維だとして、0°、45°、90°で引っ張った時に、このケースでは約30%の強度差が生じています。さらに、部品内で繊維配向が均一であればいいのですが、金型に樹脂を注入して成形される際の樹脂流動の影響を受け、繊維が様々な方向を向きます。実際の部品表面をCT画像で確認すると、白く見えるガラス繊維が、様々な方向を向いていることが見て取れます。この異方性と樹脂流動によって、部品の部位ごとに強度特性が異なることが繊維強化樹脂の難しさです。
- この異方性を衝突シミュレーションで再現するには、樹脂流動解析と衝突シミュレーションを連成させる手法が一般的に知られています。その方法は、繊維配向を樹脂流動解析ソフトウェアで計算し、その結果を衝突モデルにマッピングします。そして、マッピングされた繊維配向に従って異なる強度特性を出力できる材料モデルを適用することで異方性を再現します。"だったら開発車種ごとに流動解析をすればいいじゃないか"ということになりますが、この樹脂の流動解析が非常に難しいのです。
まず、流動解析ソフトウェアの操作を習得しなければなりません。流動解析ソフトウェアでは、成形後に反ったり凹んだりしないかを詳細に検討するのが主目的ですので、高機能な分、扱うのは難しいのです。また、樹脂成形そのものの知識も必要です。成形条件表を見ながら流動解析モデルを作成しますが、この領域の用語の意味がわかっていなければ設定することができません。したがって、流動解析を実施するには技術と知識が必要で、誰でもできるものではありません。そして、そこをなんとかクリアして流動解析ができるエンジニアを育てたとしても、その技術は難しいだけに属人化しがちです。さらに流動解析は、計算時間がかかることが知られています。衝突シミュレーションモデルの作成は、CADモデルを作ってから組み上げ作業までを決められた日数の中で行わなければなりません。流動解析が追加されるからといって期間を延ばすことは許されませんので、この手法では開発サイクルに乗せることができません。加えて、流動解析ソフトウェアのライセンス費用も少なからず負担となります。
そこで、今回のプロジェクトでは"誰でも簡単"に、"高速"かつ"低コスト"で繊維配向情報を衝突シミュレーションモデルに反映することができるシステムを構築しました。このシステムを使えば、モデル作成期間に影響を与えることなく、異方性を考慮したモデルを作成することができます。 - 図4に従来手法と新しく構築したシステムを示します。開発したシステムでは、問題の流動解析をサロゲートモデルに置き換え、マッピングもサロゲートモデルと連携しやすく、超高速な独自のツールとし、情報共有を簡単にするために自動レポート生成ツールを開発しました。そして、これらのツールを直感的に操作できる統合GUIで繋ぐことで、複数のソフトウェアを渡り歩く手間を排除しました。
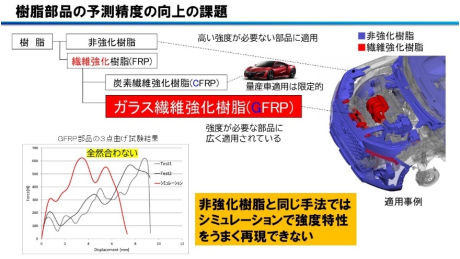
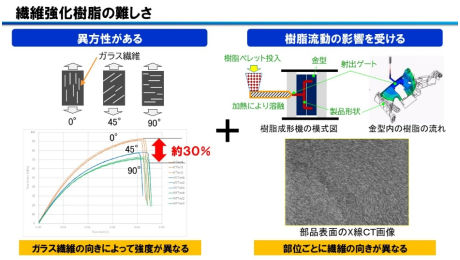
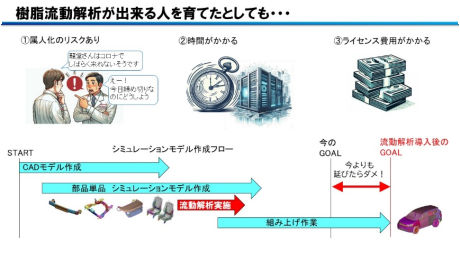
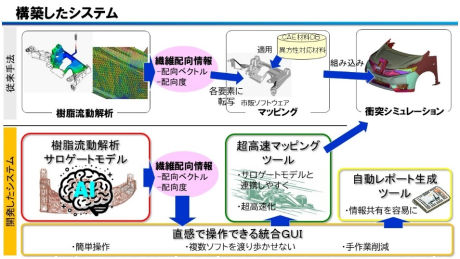
サロゲートモデルは、2D平板から実際の部品形状へと段階的に構築
- ここで、開発の歴史を簡単に振り返ります。既に機械学習で実績をあげられていたIDAJさんと2020年から研究を始めましたが、当時はまだサロゲートモデルという言葉が出始めた頃。いきなり、部品形状でサロゲートモデルができるとは到底思えませんでした。そこでまずは、2Dの平板で樹脂を射出するゲートの位置を様々に変え、機械学習で繊維配向を予測できるかどうかを事前調査したところ、良好な結果が得られました。
AI技術が浸透した今となっては信じられないことですが、さらに研究を進めようとした際には"AIは未知の部分が多い技術なので、利用は慎重になるべきだ"という消極的な意見が出ることもありました。それでもなんとか本格的に研究を始めることができ、今度はランダムに穴を開けた2D形状でもうまく予測することができました。しかし、この段階でもまだ、実用性がある技術にまで昇華できるとは認知されてはいませんでした。
そして今度は、2D形状から簡単な3D形状に発展させて良い結果が得られ、ここまで来ると周囲からも期待が寄せられるようになり、やっと最終目標の実際の部品形状に進むことにしました。これらの過程では、まさに縁の下の力持ちとしてIDAJの技術者の皆さんにご協力いただいて、技術レベルをステップアップさせていくことができました。 - 繊維配向を予測するのは、PP-GF20という繊維強化樹脂で作られたGRILLE STAYとBUMPER UPPER BEAMという部品です。人間の脚を模したインパクターを車の前面にぶつける歩行者保護テストでは、これらの部品が割れるか割れないかが、性能に大きく影響します。
サロゲートモデルの構築手順ですが、まず学習フェーズでは流動解析を大量に実施し、学習用データセットを作成します。1つの学習モデルあたり20個の形状を用意し、部品ごとに樹脂の射出ゲート位置を100パターン変更しました。また、部品の形とゲート数によって樹脂流動の傾向が異なりましたので、繊維配向の予測精度を上げるために別々の学習モデルを作成することにしました。それが6種類ありますので、合計で12,000ケースの流動解析を実施して、繊維配向情報を取得しました。
学習データセットを作るにあたって工夫した点が2つあります。1つ目はモデルの変換です。流動解析モデルは四面体をつなぎ合わせたものですが、形状を再現するためにどうしても要素分割が細かいところと粗いところができてしまいます。このままでは要素の座標が部品ごとに不均一なので学習させにくいのです。そこで一辺が200個の均一なボクセルと呼ばれる六面体で再現することによって、要素分割に依存せずに学習させることができました。2つ目は、ゲートからの距離を入力データに加えたことです。流動解析では、樹脂がゲートから放射線状に広がります。そのため、ゲートからの距離は繊維配向への影響が大きい情報なので、ゲートから各ボクセルまでの経路の長さを入力データとして与えることで、予測精度を向上させることができました。データは色の濃淡として与えています。 - 機械学習の実行で適用したアルゴリズムはPix2Pixです。オリジナルのPix2Pixは、2D画像を対象にしたものですが、生成器と識別器で使用されているPyTorchの関数を3D用のものに差し替えることで3Dへの拡張が可能です。これは3D化されたブロックの1つが、1つのボクセルに対応しているイメージです。
学習時間は1モデルあたり500時間、6モデル分で合計3,000時間、約125日かかっています。学習結果を確認すると平均二乗誤差が小さく、精度よく学習が実行できました。
予測フェーズの検証には学習に使用していない、完全に未知の形状を用いました。前処理では学習時と同様に、ボクセルモデルへの変換と、予測するゲート位置から各ボクセルまでの経路長の計測が行われます。この処理に1分半程かかります。そこから得られたボクセルモデル自体とゲートの座標、経路長を入力として学習モデルに推論させます。推論は約1分で完了し、繊維配向情報が得られます。
今回は繊維配向の予測精度を確認するため、流動解析モデルを真値として比較検証を行っています。 - 図8左上段がGRILLE STAYのゲートが1個のケースの真値である流動解析、下段が推論結果です。事前の予想では部品形状は複雑なので、もっと外れた結果になってしまうのではないかと心配していましたが、ゲートから樹脂が放射線状に広がっていく様子をうまく予測することができています。
定量的に予測精度を表すために、真値と推論結果の繊維の方向を示す配向ベクトルの角度差を算出しました。角度誤差の許容値を検討する際は、推論結果が流動解析の配向ベクトルの傾向をつかめていることを表現できれば良いとし、そのためには、二つのベクトルが似ていることが示せれば良いと考えました。そこで、ベクトルの類似性を表す指標として広く知られている、コサイン類似度を用いることとしました。
コサイン類似度では、0°から90°未満までを似ている、90°が無関係、90°以上が似てないと判定します。ただし、繊維配向ベクトルには頭尾の区別がないため、最大誤差は90°です。そのため、コサイン類似度と同じく最大誤差の半分を許容領域と設定し、45°未満ならOKと言う基準を設定しました。
角度誤差を見ると全体平均は27°、局所的に誤差が大きい所がないかを確認するために、縦横5分割したエリア別で見ても最大39°ということで、設定した基準をクリアできています。 - ゲートが2個の場合でも、2つのゲートから樹脂が広がって行く様子を再現でき、流動がぶつかり合うところにできるウェルドラインという現象も再現することができました。角度誤差も許容範囲内に収まっています。
- もう一つのBUMPER UPPER BEAMについてもゲートが1個のケースでは、細長い本体だけでなく、出っ張った部分の傾向もうまく予測することができています。角度誤差は全体的に小さく予測できています。ゲートが2個の場合でもGRILLE STAYと同様にウェルドラインを予測することができ、誤差も許容範囲内です。
このように、目標誤差内で予測できる良いサロゲートモデルを作成することができました。
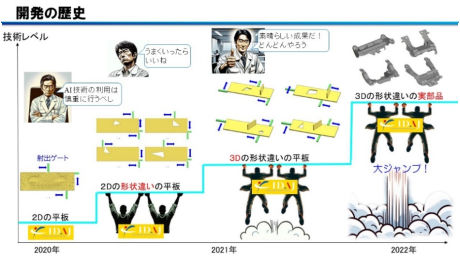
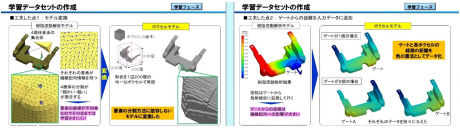
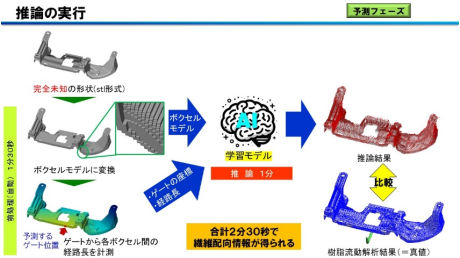
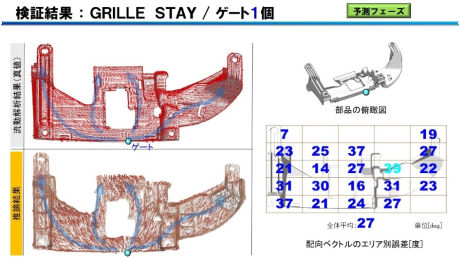
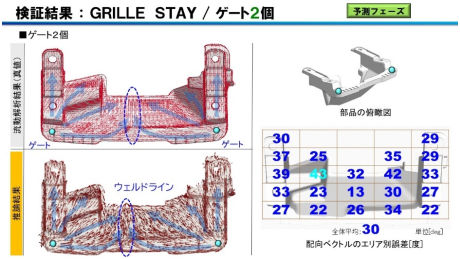
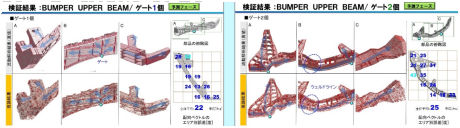
開発した独自ツールを統合GUIでつなぐことで、定常開発への適用を視野に入れた効率化を達成
- 当初は市販のマッピングツールを使う予定でしたが、その場合サロゲートモデルから出力されたデータをそのまま使えず、一旦は別のソリッドモデルにマッピングし、それをフォーマット変換してから、再度マッピングしなければなりませんでした。また他にも、手作業が多く、処理に30分もかかり、ライセンス費も高額であるという課題がありました。そこでIDAJさんに「いっそのこと独自のマッピングツールを作れないでしょうか?」と相談したところ、「むしろそのほうが、都合がいいです」と言う意外な返答をいただきました。「やってみます」でできてしまうところが、IDAJさんのすごいところだと思っています(笑)。
独自マッピングツールを採用することで変化した作業フローを図11に示します。市販ツールのフローでごちゃごちゃしていた工程が消え、手作業が不要で、直接衝突モデルにマッピングできるようになりました。課題の一つだった処理速度は、当初は市販ツールと同等の30分だったものが、こちらから要望せずともIDAJさんが改良してくださって、たったの15秒と初回版に比べて120倍速の超高速マッピングツールが完成しました。 - 自動レポート生成ツールの開発目的は、円滑に情報を共有するためです。先ほど申し上げたウェルドライン部は割れやすく、どこにできるのかを把握しておきたいというニーズがありますが、配向予測システムを起動していないと繊維配向の状況が確認できないのは不便、かと言って、手作業でスクリーンショットを撮るのも非効率なので、パワーポイントのレポートを自動生成できるようにしました。このレポートよって、ゲートからの距離情報と繊維配向の状況からウェルドラインが発生するおおよその位置の見当をつけることができます。
最後に、直感的に操作できる統合GUIについてご紹介します。
このGUIではstl形式のモデルを読み込み、図12の青枠のところで視点などを好みの表示状態にしながら、赤枠の部分で推論の実行、緑枠の部分でマッピングと、一連の作業を1つの画面で処理することが可能になっています。また、ファイルメニュー内にある、レポート生成機能や、推論条件を保存・呼び出しする機能も備えています。 - 冒頭で申し上げた様に、繊維配向情報を得るには、流動解析ソフトウェアの操作と樹脂成形の知識を習得したエンジニアでしか対応できませんでした。それに対してこのシステムを使えば、サロゲートモデル化と簡単なGUIで誰でも繊維配向情報を得ることができます。繊維配向の取得作業も、流動解析はモデル作成も含めて25時間ほどかかっていましたが、このシステムを使えば約3分と劇的に短縮することができました。
- 詳細なご説明をありがとうございます。本日ご紹介いただいたこのシステムは、量産機種などほかの機種へも適用するといったご予定はおありですか?
- 今、トライアルを行っているところなので、ここでしっかりと成果を出せば、定常開発の中に取り込み、当たり前の技術になっていくと考えています。継続して研究と検証を進めていきます。
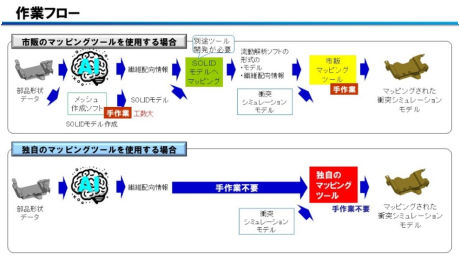
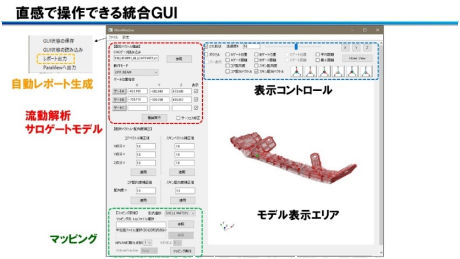
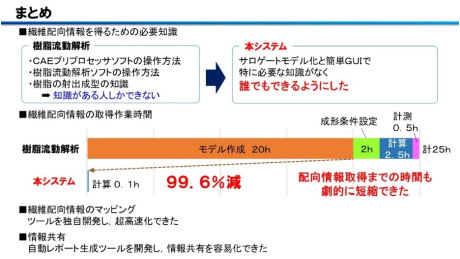
省略
このインタビューの詳細は季刊情報誌IDAJ news vol.119でご覧いただけます。
ユーザー登録済の方はユーザーサポートセンターからダウンロードできます。
- 分野1:
- 構造解析
- 分野2:
- 機械学習・ディープラーニング(AI)