富士通研究所 様(IDAJ news vol.92)
ものづくり現場における生産性向上への取り組みに「modeFRONTIER®」をご活用
株式会社 富士通研究所 デジタル共創プロジェクト 製造グループ 様
IDAJ news vol.92お客様紹介コーナーより抜粋
発行日 2018年6月
解析種別:最適化
課題等:ポスト処理、LSI、LabVIEW、連成
省略
- それでは、ご担当されたmodeFRONTIERを適用したプロジェクトについてのご紹介をお願いします。
-
以前は計測分析を担当していたのですが、そもそも、計測分析技術の研究開発というのは、ものづくりの主役ではありません。それでも、ものづくりの現場に携わっているお客様に対して、製造されたモノの現状を理解することをサポートしたり、将来の指針につながる「気づき」をもたらす重要な役割を担っていると思っています。“いかにしてモノの性能を評価するか”という課題に対して、既存技術の高精度化や高速化はもちろんのこと、既存技術では評価できない性能の可視化やモデル化、また、新たな価値を想像する分析技術の開発を目指しています。
しかし、その評価の視点や対象は、製造条件のフィックスを目的にすることもあれば、品質保証の新たな指標づくりに取り組むこともあり、依頼者ごとに大きく異なります。これに因んでは、2つの取り組みをご紹介します。
1つめは、LSIにおけるソフトエラー評価方法の最適化です。LSIにおけるソフトエラーは、主に放射線が原因で発生し、LSIが誤動作する現象で、物理的に破損するハードエラーとは異なり、データ反転など一過性の動作不良を起こします。そのため、その品質保証には動作環境下での微量の放射線を計測する必要がありました。そこで、ガス式カウンタでは測定不能な微量の放射線を、個体検出器を用いて高精度に検出する方法を検討しました。“放射線の検出感度が低い“ということは、つまり放射線の数え漏れがあるということですので、従来の平面的な形状の固体検出器を立体化し、その形状をmodeFRONTIERで最適化することによって、平面状の固体検出器を試料に直付けした従来の条件よりも、検出効率が向上する形状が存在することがわかりました。その形状を用いて、標準放射線源で検出効率を評価した結果、検出効率がおおむね1となることを実証することができました。事前には従来の直付け方式より検出効率が高い条件が存在するとは思ってもみなかったのですが、検出効率の向上と検出器の作成コスト抑制を両立させることができる実用的な解を探索することができました。
2つめはLabVIEW( 註:National Instruments社製)との連成による、LSI特性の可視化技術の最適化です。ブラックボックス化した分析機材の性能を可視化して、機材に担わせるべき処理を適切に設定することで、測定環境やオペレータに依存せず、状況に応じて機材の性能が最大限に発揮できるようになりました。この取り組みによって、modeFRONTIERが理論計算や解析だけでなく、実機運用でも有効であることを確認することができました。 - modeFRONTIERには豊富なポスト処理機能があり、その中の多変量解析ツールを利用した解析結果の可視化という点でも成果をあげています。パソコンや分析装置の発展に伴って、膨大な情報を取得することができるようになってきたため、それらを見やすく整理することは、ものづくり支援のための必要不可欠な技術だと考えています。高度な分析技術によって得られた実験結果を解析する場合、多くの研究者は、理論計算が正確に物理現象を再現していることを前提としつつ、理論解析によって計算された結果と実験結果を比較して、実験結果を最もよく説明できる物理モデルによって実験結果を説明しています。このような用途の数値解析ソフトウェア開発においては、数値演算上に多数の近似計算が取り入れられることが少なくありません。しかし、みなさまご承知の通り、近似計算の精度は、計算時間とトレードオフ関係になることが多いのです。そこで、“この計算精度は、計算時間に対して最適化されているのだろうか”という疑問を解決するために、多目的数値最適化を使用して、計算精度と計算時間を最適化するソフトウェアの変数を決定する取り組みを行いましたが、弊社での計算例では、スパコンクラスのコンピュータを使った並列計算で約1か月かかったことがありました。これは到底、実用に耐えうるレベルではありません。そこで無駄なパタメータをそぎ落としていくと、なんと24時間程度で計算が終了し、最終的に、近似精度を保持しつつも、計算時間を110分の1程度にまで短縮することに成功しました。
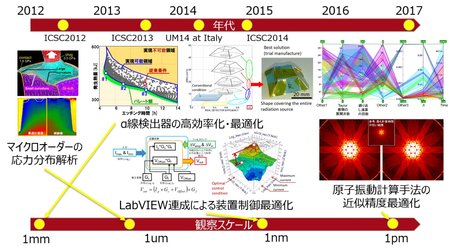
工夫次第で、多品種少量・機種混合生産ラインのリーズナブルな最適化計算が可能。
- 弊社やESTECO社のカンファレンスにおいて、これらの成果をご発表くださっており、設計を担当されるカンファレンスのご参加者様からは、ご自身の業務とは異なる分野で取り組まれたケースが参考になるというお声を頂戴しています。今回もこのようにたくさんの事例をご紹介いただき、誠にありがとうございます。
さて、続いては最近の取り組み事例についてご紹介いただけますでしょうか。 -
先にご説明した事例はものづくりに直結する事例ではありませんでしたが、ここからは工場の生産計画立案に対する事例をご紹介します。
ものづくりの現場では、これまでも生産計画や工場・設備の稼働率改善など、生産性や品質の向上に向けた様々な取り組みに最適化が利用されています。特に最近は、大量生産から多品種少量生産へと転嫁が進み、かつIoTの普及もあいまって、その対象はさらに複雑なものとなっています。新たな技術にICTによるデータ活用の機能を加え、これまでは困難だった複雑な事象の解明や生産性のさらなる向上、製造品質の予測といった、新たな価値を創出する仕組みを構築したいと考えています。
実際のものづくりの現場において、製造ラインにどのように製品を流すかを決めることは、効率化という観点から極めて重要ですが、多品種少量生産の工場では、それらの計画や判断をオペレータの経験に頼っているところが少なからずあります。果たしてその計画や判断が本当に最適であるか検討すること、さらに、現場のデータに基づいて少し先の状況を予測し、現場のオペレータや装置に対して“いま何をすべきか”という判断材料を示すことが必要です。そこで、modeFRONTIERを使って製造ラインの最適化を行ってみました。 - 今回検証する製造ラインは、実際の工場で発生しているケースを参考に、多品種少量・機種混合生産ラインのデジタル製造ラインとしました。最適化処理に用いるソルバーには、渋滞学をベースに自作したラインシミュレータを使います。デジタル製造ラインは、複数の分岐や合流を持つ3工程で、工程#1には2機、工程#2には3機、工程#3には6機の製造装置があります。各工程の製造装置には新旧織り交ぜた装置が含まれており、同じ加工でも製造時間が異なることとしました。全部で工程は3つですが、製品によっては工程#1、工程#2をスキップするものが存在すると仮定し、また、工程#3は必須工程としました。工程#1、工程#2には工程作業を必要しないときに通過するエスケープラインを設置し、このラインに入った場合には前に投入した製品を追い抜くこともできます。
-
製品固有の装置滞在時間と3つの分岐の選択可能ルートを、それぞれ製品に紐づけた情報として与え、分岐のルート選択と製品の投入順序を入力変数として最適化を実行します。仮に製品が30個とすると、すべてを組み合わせ数で最適化すると、厳密解を求める計算回数は30!で、これは2×1032回に該当します。
ラインシミュレータとmodeFRONTIERを用いて、目的関数を製造に係る総コストの最小化、生産に係るリードタイム最小化とし、入力変数は62製品の投入順番と製品の分岐情報のみとして最適化演算は実行せず、各種入力変数のみランダムに条件変更して目的関数の振る舞いを検証しました。その結果、ランダムな分岐情報の変更のみでも、1万回以上の演算を行うことによって、リードタイムに関してはそこそこ良い条件を探索できましたが、コストに対しては、投入可能な装置のうち低コストの装置を通るような条件をランダムに求めることは、条件数が多い場合には最適解に到達しづらいことがわかりました。また投入順番を変更した場合には、納期の概念が入らなくなってしまうため、納期優先の製品が後回しになることがあります。これでは、「最適解ではなくてもよいから、早くて、納期に遅れない計画を立てたい」という現場の声にこたえることができません。 - そこで生産計画の最適化法を検討することにしました。似た仕様をグルーピングして目的関数を定め、相関のある少量の製品を仮想的に投入し、最適な1個目の投入製品を決定します。次の製品では、機器投入品の位置やルート、装置故障や特急品などの現状を把握したうえで、再度仮想的に製品を流し、最適な2個目の投入製品を決定します。この作業を全ステップで繰り返し、最後の製品まで選択を続けます。この方法では、特急品や装置故障、エラー品発生などの外乱に対してフレキシブルに投入計画を変更することができ、製品投入や装置滞留時間が比較的長い場合に、実時間最適化を必要としなくなり、多目的最適化を実行できるというメリットがあります。
-
次に、各ステップでmodeFRONTIERによる多目的最適化を実施し、リードタイムとコストに対して最適化を実行しました。投入順番を決定する投入製品数を62個とし、優先納期順に並べた6個の製品をラインシミュレータに投入、投入順番と分岐情報を変数として、リードタイムとコストに対する多目的最適化によってパレート解を抽出します。
1個の製品情報を決定するためには意思決定が必要なため、優先指標を決定して、1番目の投入製品の条件を固定します。次に1番目の投入条件を固定して、1+6個の製品を投入し、投入条件が決定していない6個の製品に対して、投入順番と分岐情報を変数としてリードタイムとコストに対して最適化します。1番目の製品の投入決定方法と同様に2番目の投入製品の条件を決定し、順次62個の製品が決定するまで演算を繰り返して計画を策定します。このような実時間制御の概念を導入した最適化演算によって、リードタイムとコストに対して最適化を実行、62個の製品を順次決定した結果、特にコストに対しては製品稼働コストが安い装置に優先配置されるため、ランダムに探索した結果に比べて、コストをかなり優先する計画を策定することができました。また、リードタイムにおいても約7%の改善が見込める計画となっています。62製品の投入順番は大きく変更されることはないため、納期順守の計画も同時に策定することができ、また複数の条件を提示することによって現場で意思決定を行いつつ運用することが可能になりました。 - 各条件を詳細に見ると、リードタイム優先の条件においては追い抜きする製品の投入タイミングがポイントになることがわかります。リードタイムが少なくなればストア製品は減少し、コスト優先の条件においては、装置稼働コストが低い装置に投入すれば良いのですが、その分ストア製品が増加します。結果として、現場オペレーションのルールを確認することになり、次なる改善につなげることもできました。
- これまで多くのケースにmodeFRONTIERを適用いただいていますが、modeFRONTIERを活用するメリットはなんでしょうか。
-
直接的なメリットとしては、検証の時間が短くなったことです。modeFRONTIERは、ワークフローのビューイングで最適化計算の過程を確認することができるため、これ以上計算しても仕方ない場合には途中で計算を終了させられますので、無駄な計算をしないで済むようになっています。また、ポスト処理機能が優れているので、計算後すぐに多変量解析や応答曲面を作成できるため効率的でもあります。
さらに、手作業では時間がかかりすぎる計算をmodeFRONTIER任せにできること、人間の頭では把握しきれないことを示してもらえることですね。CAP(註:Computer Aided Principle)も利用しており、まだ事例としてご紹介することはできませんが、生産性の向上に貢献する、面白そうな結果が出始めています。
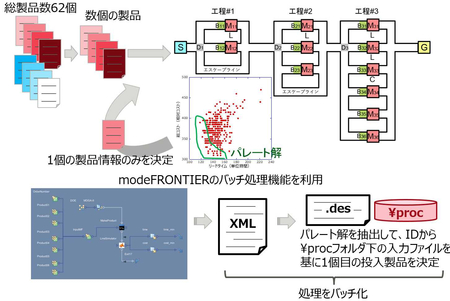
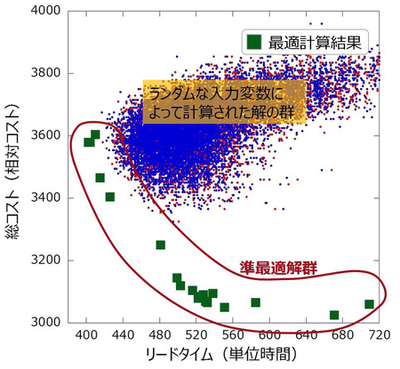
省略
このインタビューの詳細は季刊情報誌IDAJ news vol.92でご覧いただけます。
ユーザー登録済の方はユーザーサポートセンターからダウンロードできます。
ご活用いただいている製品
- 分野2:
- 最適設計