日立Astemo 様(IDAJ news vol.113)
インテークマニホールドの量産設計に複合最適化技術を活用した設計プロセスを構築
日立Astemo株式会社
パワートレイン&セーフティシステム事業部 ICEビジネスユニットEMS製品本部様
IDAJ news vol.113お客様紹介コーナーより抜粋
発行日2023年9月
解析種別:流量感度CAE、Adjoint法、数値最適化、板厚最適化、位相最適化
課題等:耐圧設計、量産設計、工数削減、軽量化、標準化
省略
- この度は、インマニ設計の効率化に向け、最適化技術を活用した設計プロセスの改善検討をIDAJにご用命いただいたわけですが、なぜそのようなお取り組みを始めようとなさったのか、きっかけなどをお聞かせください。
- 現在、自動車業界は電動化をはじめとするCASEシフトの加速によって、あらゆる開発リソースが再配分されていますが、現時点ではICE需要が一定数残ると予測されているため、弊社としても開発を一層効率化し、少ないリソースの中でもQCDを高度にバランスさせた提案が必要だと考えています。特に目標の一つである軽量化については、従来の設計手法では達成が困難だと考えており最適化の活用を検討していました。
また、ICE製品設計のリソース削減や技術継承も課題です。数年前から設計プロセス標準化の取り組みを開始し、試作レスを目標に実試験をCAEに置き換え、CAE標準化と自動化などを進め、設計効率は大幅に向上しました。しかし、設計者の経験依存による性能や品質、工数のバラツキという課題は残っており、新しい設計プロセスが必要だという認識を持っていました。これらの状況に対応するため、デジタルをフル活用したプロセス変革を狙いました。
暗黙知やベテランの知見を取り入れた標準化を視野に、量産設計担当自らがプロジェクトを主導
- シミュレーションの技術構築は専任部門や先行開発部門が担当されるケースが多いとお聞きしますが、なぜ量産設計担当者様が自ら主導されたのでしょうか。また新手法やプロセス変革は、実設計で適用しても効果を出すのが難しいと言われることがありますが、御社のご状況はいかがでしょうか。
- 弊社にも専任部署がありますので任せることができますが、今回は、新手法で、経験に依存しないプロセスに変革する必要があり、私が主導することで実設計の現場で直ぐに活用することができるのではないかと考えました。ただし最適化や設計効率化などの最新情報は、ベンダー知見が必要だと考え、コンペの結果IDAJさんに決めました。
今回の取り組みは、目標とする軽量化を達成するために、従来の設計手法では困難だという共通認識が設計者や上長にありプロジェクト化されたものです。この共通認識は、“設計横通し”という設計者同士のコミュニケーション活動から醸成されたものだと思います。この活動は、数年前からボトムアップで始まり、設計者が今起きている問題や課題を他の設計者と共有し、対応案を検討します。アウトプットは設計標準化に始まり、試験同定を経たCAE標準化、自分達だけでは対応が困難なCAE自動化やテンプレートの作成は専任部署と共創するなど、いくつかの設計業務を効率化してきました。もちろん失敗もありますが、複数の成功体験とその共有によって、変化を受け入れ、やってみようという風土が作られたのだと思います。
実設計への適用は緒に就いたばかりです。初めての手法ですから、最初はやはり身構えてしまいましたが、効果があれば活用したいといった声があったため、ある製品の開発中に起きた課題対応のタイミングで実際に適用し実績を作ることができました。現在は実務担当者の教育が終了し、他の開発機種での活用が始まっています。 - 新手法の活用やプロセス変革の土壌ありきのお取り組みであったことがよくわかりました。弊社エンジニアからは、設計とCAEが標準化されておりスムーズに最適化技術を構築することができたと聞いています。また設計プロセスがDSM(註:Design Structure Matrix)手法でわかりやすく可視化されていたため、工数が掛かっている部分を集中的に改善することで定量的な成果を上げることができたことは、私どもとしても大変うれしく存じます。
プロセス改善目標の総工数は約15%減、軽量化は約28%減を達成。同時に最適化のメリットを確認することができた。
- これら背景を踏まえて、プロセス改善の目的や概要、成果などのご紹介をお願いします。
- 本プロジェクトの目的は、設計総工数の削減と軽量化の達成、暗黙知やベテランの知見を取り入れた設計プロセスを構築することとしました。改善ステップは、現状の設計プロセスにおける課題の分析、対策アイテムと改善目標の設定、対策アイテムの技術構築と実設計適用による改善効果確認という3つのステップに分割しています。
- 先に改善結果からご紹介しますと、総工数は目標には未達でしたが約15%の削減、軽量化は約28%の削減を達成することができました。暗黙知やベテランの知見も設計プロセスに落し込むことができ、最終的にこちらの図に示す設計プロセスを構築することができました。また最適化技術を構築していく中で、これまでのプロセスでは考え付かなかったような形状で改善効果が得られることがわかりました。これは経験の豊富なベテラン技術者ほど試すことがない形状であったため、驚きとともに最適化のメリットを実感したという意味で一つ効果だと言えるものと思います。
- ここからは各ステップについてご説明します。
ステップ1では、設計メンバーへのヒアリングから始め、現行プロセスを細分化し、各プロセスにかかっている時間の算出と試行錯誤の内容分析を工程表で実施しました。手戻りについてはDSM手法で可視化し、手戻りの少ないプロセスを検討、弊社とIDAJさんで課題を抽出しました。 - ステップ2では、抽出した課題に対して、適切なソフトウェアと最適化手法による想定効果をIDAJさんに算出していただき、運用可否の判断を弊社が判断し、ステップ3では、対策アイテムの技術構築とその改善効果を確認します。
- まずは、ラフ流体設計プロセスにおける簡易耐圧CAE(図5<A>)です。従来はインナーの流路要件がOKとなってからアウターの樹脂部モデルを作成して解析するというウォーターフォール設計としていましたが、これを上流設計においてアジャイル的な設計にできないものかと考えました。これはステップ1の現状分析で、ベテランの知見や暗黙知を把握し、DSM手法で流体と耐圧の因果関係の強さを可視化することで課題が確認できたからです。
ベテランの技術者であれば、上流工程において流体設計と同時に耐圧要件を考慮した形状を検討・作成し、後工程の試行錯誤が極力発生しないように頭の中で自然とアジャイル設計を行っていますが、経験の少ないメンバーに同じような設計を求めることはできません。かといって、従来の耐圧CAEを単純に上流に移動させるだけでは、CADモデルの作成工数と解析に時間がかかりますので、同時並行で設計を進めることが難しくなります。
そこで、“ラフ”耐圧CAEを取り入れることにしました。流体CAEで使う流体部のCADモデルを流用し、シェルモデルに内圧を掛けて応力分布を評価します。最小限の耐圧CAEではありますが、基本骨格の良し悪しの検証や、応力の高い部分を後の数値最適化のパラメータとすることができますので、最小限の工数で誰もがベテラン並みのアジャイル設計が可能になるというわけです。 - 続いて流量感度CAE(図5<B>)のご説明の前に、簡単に設計の流れをご説明しておきます。
お客様からいただいた吸気諸元や設計空間制約等の情報をもとに、各ポートやチャンバーなどのCADモデルを作成し、ポート毎に定常流体解析を実施します。3気筒であれば3回、4気筒であれば4回解析し、平均流量と各気筒間の流量バラツキを評価します。ここでは金型の分割等が無い簡易モデルでラフ流体CAEを実施し、要件がOKであれば次のステップへと進み、金型の分割や抜き勾配を反映した詳細CADモデルで詳細流体CAEの評価に移ることになります。
さて、流量感度CAEに話を戻します。現状では、流体CAEは条件設定から結果処理までを自動化していますのでCAE工数は最小です。しかし流体要件がOKになるまでCAD修正とCFDを繰返すことになるため、製品や人によって異なりますが、数回~数十回の地道な試行錯誤が必要でした。さらに複数ポートの解析結果の分析とその改善検討、CADモデル修正にも工数がかかりますし、直列3・4気筒、V型6気筒などエンジン形式毎の知見が求められます。
これらの問題を改善するためにAdjoint法を適用しました。Adjoint法ではまず感度を解析し、その感度に基づいて形状最適化を行います。そこでラフ流体CAEでは、各ポートに対して流量最大化を目的関数とした形状最適化を実施して要件をクリアする算段でしたが、実際には、平均流量は上がったものの、バラツキが大きかったため、次の工程に“ひと手間”加える必要がでてきました。ここは、今回苦労した部分の一つです。 - この“ひと手間”の解消に、数値最適化(図5<C>)を適用することにしました。前工程で、Adjoint法によってポート毎に流量に対して感度の高い部位を抽出し(図7・8)、数値最適化の設計変数に設定、目的関数は平均流量の最大化と気筒間バラツキの最小化とした結果、現行量産に対して、わずかですが流量アップとバラツキを低減させることができました。ここが苦労ポイントその2です。
数値最適化は、自動でCAD形状を変更して解析を実行してくれるのですが、CADモデルのエラーが出て、すんなりとは自動化できませんでした。この問題のクリアにあたっては、IDAJさんにCAD設定などについてもフォローしていただきました。
次の詳細流体CAEでは金型の型割り等を反映した流路を評価しましたが、Adjoint法で感度が高い部位を把握した上で流量特性に影響をしないようにCADモデルを作成し、従来の流体CAEの自動化ツールで検証した結果、問題が無いことも確認できました。 - 続いては樹脂部の耐圧設計です。
これまでの耐圧設計では、先程の流路CADモデルをベースに樹脂部を設計し、基本の肉厚で耐圧CAEを実施して素性を確認していました。ここまでがラフ耐圧CAE(図5<D>)です。次にリブなどを追加し重量と耐圧要件をバランスさせていきます。この工程が詳細耐圧CAE(図5<E>)にあたります。耐圧CAEもテンプレートで半自動化されていましたが、属人的な作業であり、<D>と<E>を行ったり来たりするなど数十回の試行錯誤を繰り返していました。また最終形状が最適という根拠が弱く検討に時間がかかるため、期限をフルに使いがちです。
そこでまずはラフ耐圧CAEで、板厚最適化(注:サイジング最適化)を適用しました。前工程の流体CAEの流路CADモデルをベースに初期形状に対して、体積1.5倍の制約条件下で、最適な板厚分布を算出して弱部を把握します。この結果を元に生技要件を反映させながら詳細モデルを作成していきます。
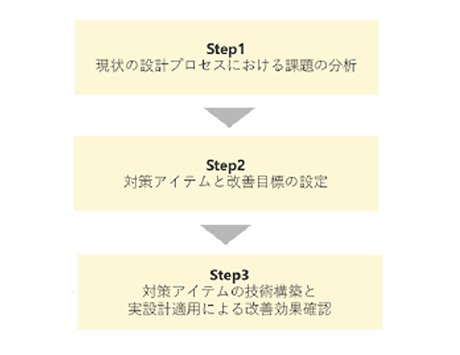
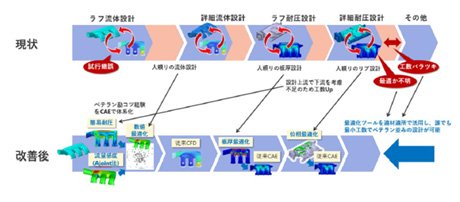
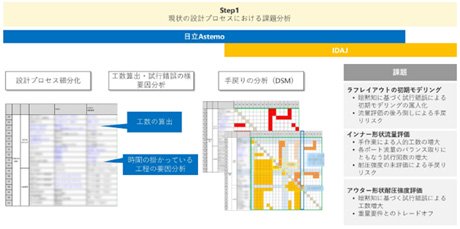
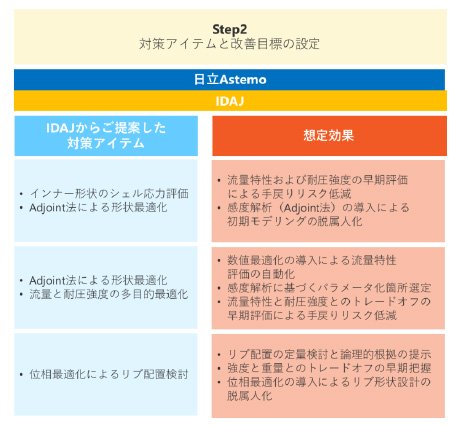
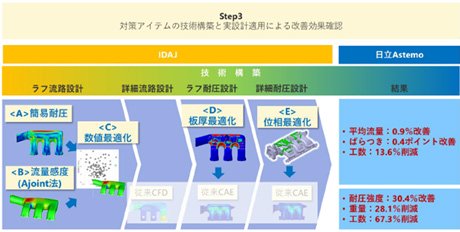
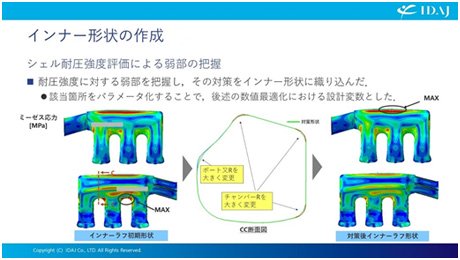
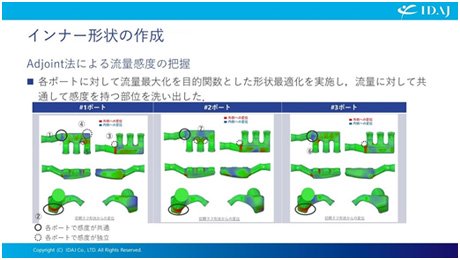

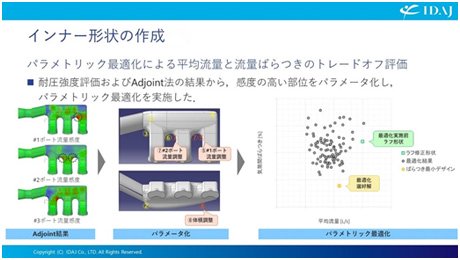
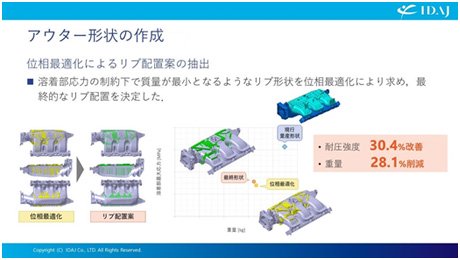
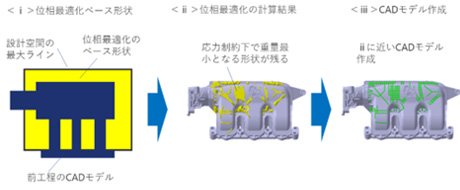
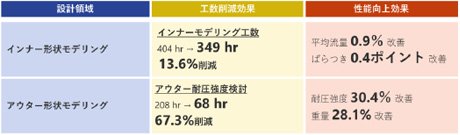
1年のプロジェクトで、設計に対して各種最適化技術を“適材適所”に活用できるようになった
- 詳細にご説明いただき、誠にありがとうございます。最初にお話いただいたように一部の目標はクリアできませんでしたが、全体としての成果はご期待に沿えるものでしたでしょうか。
- はい、そうですね。プロジェクト開始当初は、各プロセスへの最適化適用の具体的なイメージができませんでしたが、IDAJさんからAdjoint法などの様々な最適化手法をご提案いただき、一緒に取り組むことができたので、本プロジェクトを完遂できたのだと思っています。最適化技術の適材適所での活用や、CADのパラメータ設定などにはノウハウも必要だったため、自分達だけで進めていたら実運用にのせるまでにもっと時間がかかったんじゃないかとも思います。
この約1年間のプロジェクトの中で、各種最適化手法を活用できるようになったことは大きな成果の一つです。数値最適化の自動化によって計算数を圧倒的に増やすことで設計のキワ(注:限界)を説明することができますし、今までは過去の経験の延長線上にある格子状、少し冒険してハニカムのリブで試してみるのみでしたが、感度分析の結果から必要最小限の幾何学的な形状に対する説明など、関係者への仕様説明が可能になります。最適化技術には、個々の経験に依存しない設計への期待感を持っています。
[補足] 本稿でご紹介いただいた各種最適化技術と使用されたツールについて解説します。ご不明な点がございましたら、IDAJまでお問い合わせください。
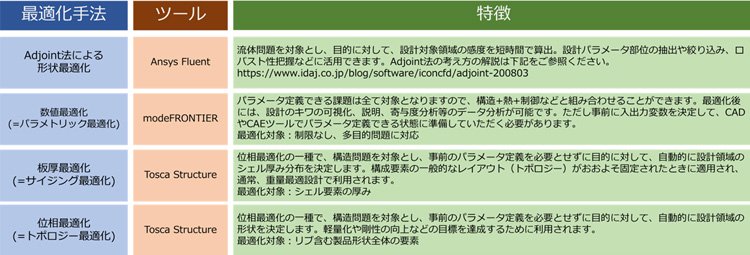
省略
このインタビューの詳細は季刊情報誌IDAJ news vol.113でご覧いただけます。
ユーザー登録済の方はユーザーサポートセンターからダウンロードできます。
ご活用いただいているサービス
ご活用いただいている製品
- 分野1:
- 熱流体解析、構造解析
- 分野2:
- 最適設計