CAEとは?
CAE(Computer Aided
Engineering)は、工業製品の設計・開発工程においてその作業を支援するコンピュータシステム、あるいはそのツール等を指します。具体的には、製品にまつわる様々な物理現象をコンピュータ上でシミュレーションすることで、構造解析、機構解析、熱流体解析、燃焼反応解析、電磁場解析、音響解析、制御ロジック診断解析、最適化解析とそれらすべてを統合したシステムシミュレーションなどが含まれます。現在のものづくりにおいては、新製品開発、既存製品の高効率化・高信頼性化、設計の合理化、トラブルシューティングなどに広く活用されるようになりました。
シミュレーション(Simulation)は、予測・設計・計画策定などのために、現実のモデルを作り、それを使って観測または実験すること、現実に想定される条件を取り入れて、実際に近い状況を作り出すこと、模擬実験を指します。このシミュレーションには様々な種類がありますが、その中の一つにコンピュータ・シミュレーションがあります。
コンピュータ・シミュレーションは、自然や社会の現象をコンピュータの中に再現して、その仕組みを理解したり予測することができます。たとえば、天気予報。雨をもたらす雲は、大気の流れに沿って動いています。明日の天気を知るには、まず大気の流れを知らなければなりません。大気の流れや雨の降り方は、物理の法則に従って、方程式で表すことができます。これらの方程式を解くわけですが、計算には、主に四則演算しかできないコンピュータが使われるため、まずは方程式を足し算、引き算、掛け算、割り算の形にします。それから、コンピュータが計算しやすい解き方を考えて、計算スピードが上がるようにプログラミングします。
計算が終了すると、文字や数字のみで結果が出力されるため、計算結果を画像にします。画像にすると、わかりやすいからです。この画像が、私たちがよく目にする天気予報図となります。
このコンピュータ・シミュレーションの中に、CAE(Computer Aided Engineering)が含まれます。
コンピュータ・シミュレーションの価値
1.世の中のしくみがわかる
- 自然現象・社会現象のメカニズムが解明できる。
- 現象の本質が理解できる。
- 原因と結果だけでなく、途中経過がわかる。
- 自然災害や社会の安全を脅かす事象を仮想的に起こすことができる。
- 可視化できるため、情報の共有化がしやすい。
2.実験・観測、理論との知的共創により科学の進歩が加速する
- 実験や観測での抜けを埋めることができる。
- 実験・観測計画の立案、設計に利用できる。
- 自然界にない物や極端な状態を作ることができる。
- これまでにない理論・法則に気づける。新たな創造。
3.未来の予測ができる
- 定量的な予測ができる。
- 研究の確度を高め、余分な労力・時間やお金をかけずに済む。
(C)理研計算科学研究センター 2018「コンピュータ・シミュレーションでできること、わかること」
CAEが果たす役割の変遷
CAEは、ものづくりにどういった影響を与えたのでしょうか。
従来の開発プロセスは、勘・コツ・経験に大きく依存し、設計・試作・実験を繰り返していました。問題が発生した際の時間と費用のロスが多く、開発期間が長い傾向にありました。
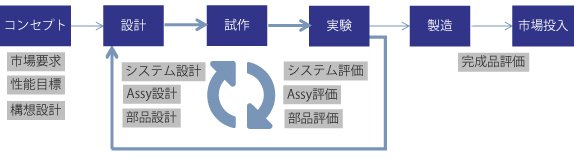
~1995年
CAEソフトウェアの販売が開始された1980年前半からは、トラブルシューティングとしてのCAEの活用が始まりました。しかし、解析は、高度な専門知識と多くの労力が必要だったので専任者のみが実施し、試作や生産準備フェーズといった設計プロセスの下流での限定的な利用にとどまり、解析にはスーパーコンピュータ(スパコン)や大型コンピュータが必要でした。
- 耐久評価不具合の際の、対策検討に活用 ⇒ 次設計の問題を未然に防ぐため
- 線形、静的強度解析
- 解析(モデリング)期間が長期にわたる(1か月~3か月程度)
- 対象部品を限定
- 専任者による解析
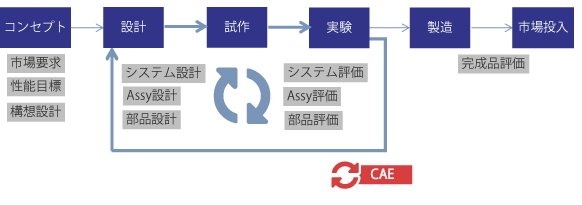
~2000年
1990年代後半には、試作回数や費用の削減を目的として、実験の置き換え(仮想実験)として利用されるようになりました。利用シーンは、詳細フェーズへと広がりましたが、依然として解析専任者による利用がメインでした。また、計算サーバーとしてUNIXマシンが広く利用されるようになってきたのもこの頃です。
- 開発プロセス・イン、フロントローディング
- 試作と解析用モデルの作成、評価とCAEによる評価を並行して実施 ⇒ CAE精度向上と次設計提案が可能にCAD(3次元ソリッド)のデータを解析モデルに直接変換できるようになった。
- 線形、静的強度解析
- 解析期間短縮(1週間~1か月)
- 部品レベルから装置レベルまで解析可能(例:エンジン本体サイズ)
- 設計者による解析
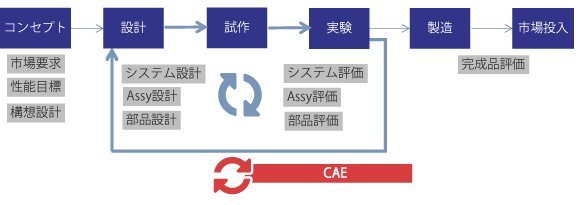
2000年代以降
2000年代に入ると、ハードウェア・ソフトウェアの発展を背景として、現在主流となっている、設計プロセス早期での課題抽出とその対応策の検討、開発期間の短縮といった目的での利用が加速しました。また、解析専任者による技術の深耕に加えて、Windowsマシンが計算サーバーにも利用できるようになったため、CAEのユーザーが設計者へと広がっていきます。企画・構想設計フェーズへの利用を背景としてCAEのフロントローディングという利用シーンと、ユーザーの拡大がさらに進みました。一方で、CAEにかかる作業自体の効率化が注目されるようになり、ルーティン作業の自動化や最適化技術が構築されています。
- ハードウェアの性能向上とも相まって、精度向上を目的にモデル規模が大規模化
- 流体解析では、OpenFOAMなどのオープンソースとFOCUSや商用クラウドの活用性の向上
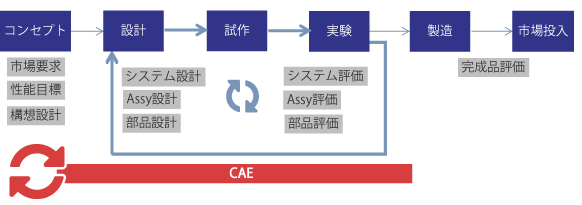
CAEが設計現場で必要とされる理由
製品に求められる性能や要件が今ほど厳しくなかった時代には、「材料力学」や「機械実用便覧」などで紹介されている簡易計算式、各社独自の経験則を含めた内製の計算式を使って、関数電卓やExcelなどを用いて強度や変形を計算し、目標への到達可否を判断していました。しかし、近年の製品に求められる複合的な性能・要件への対応においては、これまでは考えられなかった試作時の不具合や市場出荷後の問題が発生し、簡易計算式などでは求められない技術検討が設計段階において必要になってきました。
CAEを使わずに、試作品による性能検証をするならば、
- 費用がかかる
- 時間がかかる
- 不完全な情報しか得られないことがある
ということになるでしょう。
CAEを設計・開発プロセスに組み入れることで、試作検証試験を削減し、
- ローコスト
- 短期間
- 膨大な情報を得る
ことができます。
さらに、実験ではなかなか見られない物理現象、例えばエンジン内部の燃焼状態なども、シミュレーションを用いて可視化することができるため、第三者とのスムーズなコミュニケーションと情報共有が可能になります。
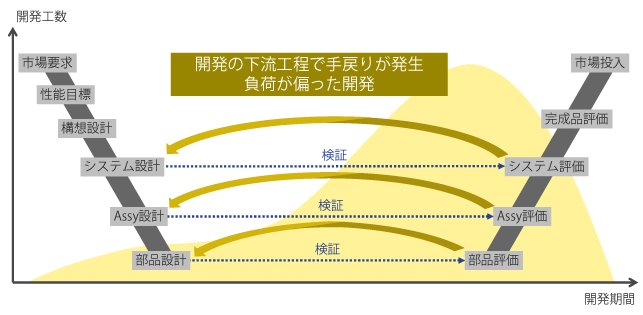
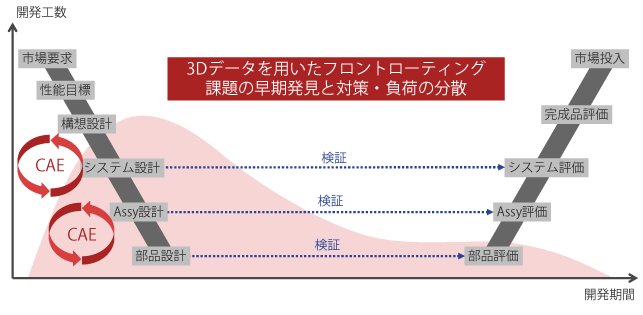
主なCAEの種類
1)CAEは、設計問題にあわせて使用する必要があります。
有限要素法(FEM)が主流の構造解析(静解析/動解析、応力解析、振動解析/衝突落下解析、固有値解析など)、有限体積法(FVM)が主流の熱解析、流体解析(空力解析、噴霧解析、燃焼解析など)、その他電磁場解析、機構解析、音響解析、樹脂流動解析、鍛造解析、鋳造解析などがあります。
単独または連成・連携による解析が可能です。
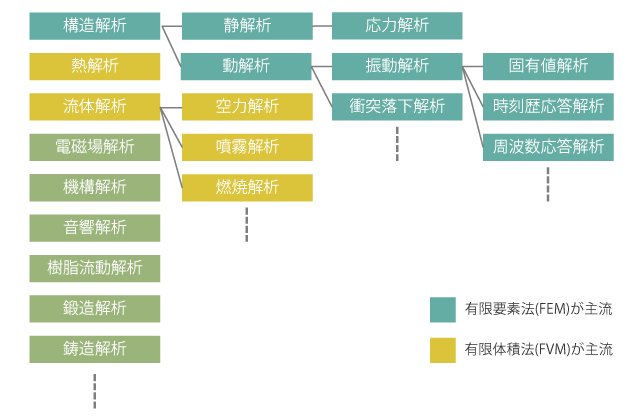
2)目的とする結果の詳細度や利用シーンによって、0次元、1次元、2次元、3次元の各解析を組み合わせます。また、それぞれをシームレスに連携させた解析が可能です。

主なCAEソフトウェアの分類
CAEソフトウェア(ツール)には、汎用ソフトウェアと専用ソフトウェアがあり、それらを連成させるためのソフトウェア、自動化・最適化のためのソフトウェア、各種シミュレーションをサポートするためのソフトウェアがあります。用途や目的にあわせて使い分けます。
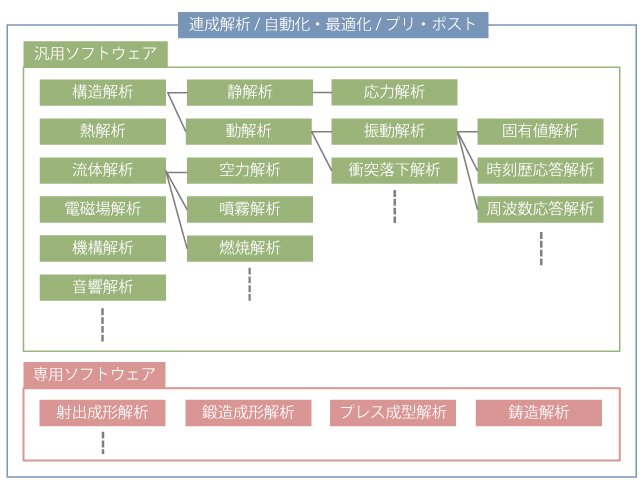
CAEは、工業製品の設計・開発工程においてその作業を支援するコンピュータシステム、あるいはそのツール等を指します。具体的には、製品にまつわる様々な物理現象をコンピュータ上でシミュレーションすることで、構造解析、機構解析、熱流体解析、燃焼反応解析、電磁場解析、音響解析、制御ロジック診断解析、最適化解析とそれらすべてを統合したシステムシミュレーションなどが含まれます。 現在のものづくりにおいては、新製品開発、既存製品の高効率化・高信頼性化、設計の合理化、トラブルシューティングなどに広く活用されるようになりました。
CAEの歴史
CAEのコンセプトは、1980年代に米国SDRC社(Structural Dynamics Research Corporation)を設立した、Jack R. Lemon博士が提唱した概念で、その後大きく発展した技術です。CAE=(イコール)「解析」・「ソフトウェア」というイメージもありますが、解析(Analysis)は、自然科学や工学の問題を数式を用いて近似的に解くこと(コンピュータを使わずに手計算でも実施可能)、また、ある物事を分解して、それらを成立している成分・要素・側面を明らかにすること(分析も含む)と言えます。ただ、CAEという言葉を利用する場面によっては同義に使うこともあります。また、CAEがそのツール(ソフトウェアまたはプログラム)として使われることもあります。
CAEソフトウェアの足跡
CAEと同義で使われることもあるソフトウェア(プログラム)の歴史を簡単にご紹介します。
主な構造解析系CAEプログラムの足跡
1950年代:米国ボーイング社で航空機翼振動特性の解析に有限要素法(FEM:Finite Element Method)を適用
1963年:MacNeal-Schwendler Corporation(現MSC Software
Corporation)設立、構造解析プログラムSADSAM(Structural Analysis by Digital Simulation
of Analog Methods)開発
当時のSADSAMは、300自由度程度(約100節点・100要素)の解析能力で、最初に適用されたのはアーチダムの強度解析
1965年:米国航空宇宙局(NASA)は、米国の基幹産業である航空宇宙産業を支援する目的で、有限要素法構造解析プログラムNASTRAN(NASA
Structural Analysis)の開発を決定。米国政府は運用版が完成するまで数社に対して5年の年月と1,000万ドルを投資
1971年:MSC.Nastranが商用FEMプログラムとしてリリース
1980年:SDRC社 J. Lemon氏がCAEのあるべき姿を提唱
1982年:SDRC社が商用CAD組み込み型FEMプログラムI-deas(Integrated Design Engineering
Analysis Software)をリリース
非線形構造解析ソフトウェアの足跡
1971年:米国ブラウン大学 P. Marcal博士らによりMarc社設立、非線形構造解析プログラムMarc(Matrix Analysis
Research Code)をリリース
1978年: D.
Hibbitt博士らによりHKS社を設立、Abaqus(※)をリリース。その他Ansys、ADINA、機構解析プログラムのADAMSもこの時期に発表
※Abaqusの語源は、ギリシャ語のaboxに由来しており、「砂をかぶった板」の意味
商用流体解析ソフトウェアの足跡
1969年:英国Combustion, Heat and Mass Transfer Ltd (略称CHAM)設立
1981年:CHAM社が汎用3次元熱流体解析コードPHOENICSリリース
1984年:有限会社ソフトウェアクレイドル設立、STREAMリリース
1985年:FLOW-3D(米国Flow Science社)リリース
~1990年代:FLUENT、STAR-CD、HARWEL/FLOW3D他リリース
1990年代後半~:機能特化型ソフトウェア(FLOTHERM、ICEPAK、X-COOL、熱設計PAC、FIRE、VECTIS、POWERFLOW他)が台頭
CAEの適用分野
自動車、重工業・重電、電気・電子機器、化学・薬品・バイオ、建築、電力・環境、航空宇宙、ターボ機器、産業機械・造船など、広く産業界全体への適用が可能です。
コンピュータ上でモデルとして表現できるのであれば、小さな半導体からタービン発電機や航空機などの大きな機械、電気化学、制御・システムまでカバーします。
解析の流れ
IDAJのコア技術の一つである、熱流体解析技術を例にご説明します。
熱流体解析に関する技術全般を指す学問もある数値流体力学(Computational Fluid
Dynamics)の英語の頭文字3つをとってCFDとも呼ばれます。
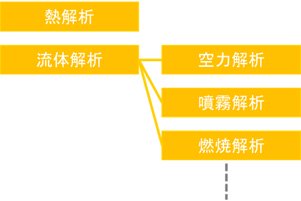
さて、熱流体解析に必要なものはなんでしょうか?
熱流体解析は、コンピュータなどのハードウェアと熱流体解析ソフトウェアを利用して、解析対象となる流体が存在する空間を定義し、その空間をメッシュ分割します。そして、境界条件を設定した上で計算を実行し、得られた結果を結果処理して流れの状況を評価します。一般的に、それぞれで必要な要素は以下の5つです。
解析する形状や計算に必要なメッシュ(メッシュレスのツールもあります)
さまざまな計算手法と計算するためのプログラム
どのような物理現象を扱うかを決める解析設定、解析領域、境界条件など
計算で得られた結果が人間で理解できるように描画する結果処理
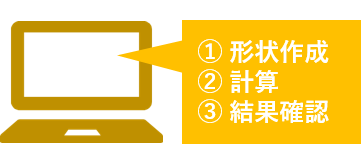
詳しくは以下をあわせてご覧ください。
IDAJ-BLOG「流体解析を構成する要素」計算するためのプログラム
コンピュータが準備できたとして、もう一つ必要なのがプログラムです。一般的に熱流体解析ソフトウェアには以下のような機能が求められます。
定義した流体空間にメッシュを生成する機能
境界条件を設定をする機能
解析を実行する機能
結果を処理する機能
なお、一般的に3次元CADデータを読み込む機能や流体空間定義機能、メッシュ生成機能、境界条件設定機能、結果処理機能などがパッケージ化されて提供されているソフトウェアをプリ・ポストソフトウェア、計算を実行するソフトウェアをソルバーと呼びます。
汎用的な熱流体解析ソフトウェアには、メッシュ生成ツール、計算のためのソルバー、結果処理ツールがパッケージ化されたものが市販されています。また、一定の利用条件や規約に従うことでフリーで利用できるオープンソースソフトウェア(Open
Source Software:OSS)や、自作されたプログラムなどを使用することができます。
IDAJで取り扱っている熱流体解析ソフトウェア
【汎用型】
- CFDに必要な機能が全て詰まったデファクトスタンダード、高性能・高機能CFDを実現「Ansys Fluids」
- 最新のメッシングテクノロジーと先進的な機能でこれまでのCFDの常識の壁を突破「CONVERGE」
【オープンソースベース汎用型】
【機能特化型】
熱流体解析は、保存則から得られた流体の基礎方程式を数値的に解くものです。この方程式をどのように解くかという計算手法にも、様々なものがあります。
![]() |
|
解析設定
解きたい実際の流れ場をどのように仮定して計算するかが、“解析手法の選択=解析設定”です。
まず物理現象として、時間経過を考えるか(定常・非定常)、流体の性質をどう扱うか(圧縮・非圧縮性、ニュートン流体・非ニュートン流体など)、流れをどう扱うか(層流・乱流、亜音速・超音速など)、固体の熱・音響・気液混合まで扱うかなどといった選択を行ったのち、CFDプログラムに該当する入力を行います。
また、計算する領域の周囲には境界条件を設定する必要があります。F1カーの空力解析を例にとると、空気の入口には車速相当の速度を、出口には大気圧相当の圧力を与え、タイヤには回転速度を与えるという設定です。これもCFDプログラムへの入力となり、CFDで解く方程式の境界条件となります。
定常 | 時間が無限に経過したあとの流れ場が落ち着いた状態 |
---|---|
非定常 |
時々刻々と変わる、過渡状態 |
圧縮性 | 外部からの力や圧力、温度の変化によって圧縮もしくは膨張することで体積が変化する性質 |
---|---|
非圧縮性 | 圧縮性を考慮しない(圧縮も膨張もせずに、常に体積が一定) |
層流・乱流 | 様々な仮定の元で乱流現象をモデル化した“乱流モデル” |
---|---|
非ニュートン流体 | 溶けたガラスや血液など、ニュートンの粘性法則に従わない流体 ビンガム流体(塑性流体 そせいりゅうたい)【例:ケチャップ、塗料など】、擬塑性流体(ぎそせいりゅうたい)【例:塗料、濃縮ジュース、マヨネーズなど】、ダイラタント流体【例:ミルクチョコレート、片栗粉水、波打ち際の砂など】 |
流体内熱伝導 | 熱伝達 | 燃焼・化学反応 |
|
|
||||
---|---|---|---|---|---|---|---|---|
固体内熱伝導 | 流体騒音 | 回転・移動 |
解析事例
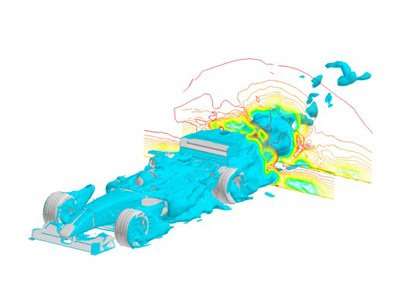
F1カー空力解析
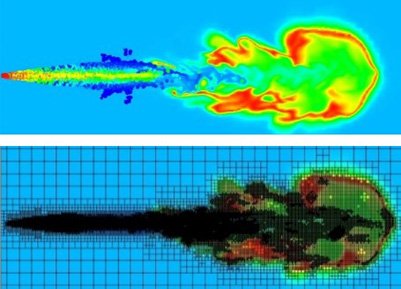
ディーゼル燃料噴霧解析
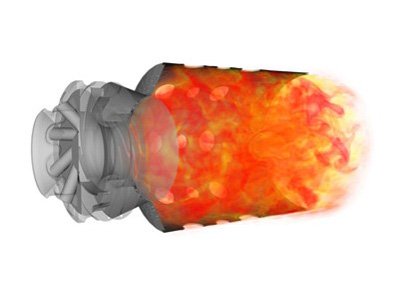
ガスタービン燃焼器内噴霧燃焼解析
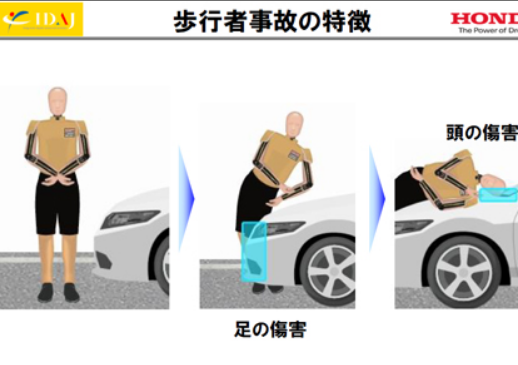
本田技術研究所 様
歩行者保護のための技術開発に「modeFRONTIER®」をご活用
解析種別:構造、荷重最適化、傷害値、強度
課題等:歩行者保護技術、POLAR、歩行者全身モデル、傷害値評価
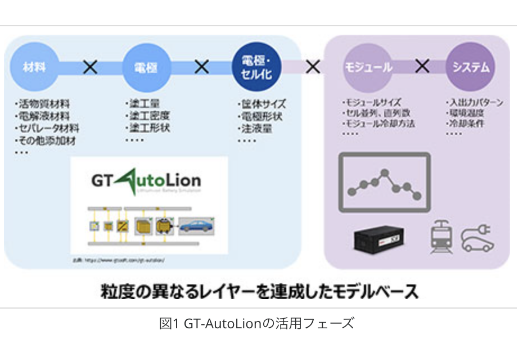
東芝 様
二次電池「SCiB™」セル開発における
電気化学シミュレーションにGT-AutoLionをご活用
解析種別:劣化予測、システムシミュレーション、電気化学シミュレータ
課題等:リチウムイオン電池、2次電池、安全性、長寿命、低温性能、急速充電、高入出力、試作レス、バッテリー、安全性、耐用年数の向上、設計検討、モデルベース開発
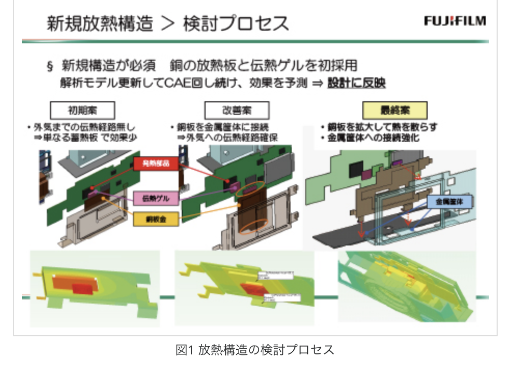
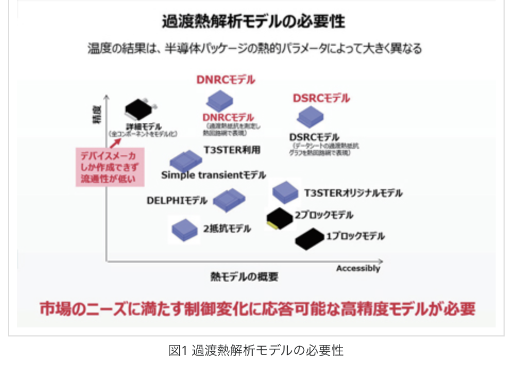
デンソー 様
Simcenter Flotherm™を活用して
モデルベース開発(MBD)による熱設計のフロントローディングを実現
解析種別:過渡解析
課題等:ECU回路、モデルベース開発、MBD、熱回路抵抗値、素子温度変化
その他事例は、以下のページをご覧ください。
実績・お客様事例CAEの課題
デジタル・エンジニアリングの中で、もっとも重要な役割を果たしている技術は、CAE(Computer Aided
Engineering)による性能・信頼性解析です。空力性能や強度・破壊検証、電磁場や音響ノイズ、燃焼効率や電子機器の熱設計対策、相反する要求性能を同時に満たす最適形状の探索など、あらゆる物理現象をバーチャル・プロダクトで解析する技術が開発され、すでに様々な製造分野で適用されています。
この技術を設計者が使う目的は、できるだけ短い時間で適切な結果を得ることにありますので、簡単かつスピーディーにCAEを実施する自動化システムや、より効率的で低コストなCAE環境が求められています。また、CAE技術をサポートし、またはその役割の一部をとって代わるであろうAI技術の構築も忘れてはなりません。CAEがAIに必要な学習データを提供することで、AIを高速なCAEモデルとして適用する試みが始まっており、革新的な技術となりえる可能性を大いに示唆しています。
シミュレーションの宿命として、計算結果と実験値などの実現象との差分は常に存在します。実現象に近しい計算結果と、それを得るための入力条件の収集にかける工数や、計算分解能の粗密による計算時間などは常にトレードオフ関係になっており、その利用目的によって、シミュレーションの活用シーンは細かく分かれます。様々な区分があるかと思いますが、例えば、以下のようなイメージです。
- 絶対評価:実験と十分に合わせ込んだ信頼性の高いモデルを実験の代わりに使う
- 相対評価:実験と傾向が合う程度のモデルを大まかな条件の比較に使う
- メカニズム解明:実験や測定が困難な現象を把握するため、シミュレーションを使う など
また、経済的(費用)・人的(時間)コストや導入後のROI(Return On Investment)に関する不安もあるかと思います。CAEの導入にあたって、一定のコストが発生することは事実です。シミュレーションはコンピュータ上で行いますので、シミュレーションを実行するための計算機が必要です。計算機は自社内に計算環境を構築したり、最近ではクラウド環境を利用することもありますが、いずれにしても想定する計算規模や計算速度を確保するためにはある程度の増強が必要になるかもしれません。もちろんシミュレーションの規模や種類によっては、普段使っているパソコンで十分なことも多々あります。
計算のためのソフトウェアも不可欠です。ソフトウェアを内製できない場合は、購入費用やソフトウェアの使い方を覚えるための教育・トレーニング費用がかかります。使い方を覚えた後は、「そのソフトウェアで何を解析したいのか」、「何の現象を解析したいのか」等といった、実対象を計算モデルとして構築する技術を習得しなければなりません。この習得にはどうしても時間と経験が必要です。さらに、計算実行時に計算エラーが発生した時の対処方法に詳しく知っていることも大切です。このように、CAE技術を活用するには、様々な作業が発生することがあり、この時、対応を誤るとしばしば想定以上の時間が生じてしまい、技術者の貴重な工数を奪うという残念な結果にならないとも言い切れません。
シミュレーションでは、正しくシミュレーションが実行できたかどうかを判断しなければなりません。これまで専任者が担当してきたことからもわかるように、結果を判断するには専門的な知識が必要です。また、設計者が最も不安に感じるのは上述したような、シミュレーションの“確からしさ”です。実測や実験結果との乖離が著しい場合は、シミュレーション結果を設計業務に適用することはできないこともあります。
ここまでご説明したように、CAEを設計業務に適用するということは、計算環境を準備して、ソフトウェアを導入するだけではコストばかりがかかり狙った成果を得ることは難しく、技術構築を前提とした、設計プロセスの変革をも視野に入れておくのが良いでしょう。
CAEが運用に乗り、適用領域が拡大するにつれ、今度は、CAE業務そのものを効率化したり、さらに利用者を拡大させてCAEの効果を上げるためには“設計者CAE”の考え方を取り入れて、シミュレーション作業の自動化、解析専任者のノウハウの共有と再利用、最適化技術の適用など、新しい仕組みや技術を積極的に取り入れてCAEをさらに発展させていくことも大切です。 そして、CAEが設計開発プロセスに組み込まれると、そこで生成される大量のシミュレーション結果や、プロセスそのものを適切に管理・活用するための仕組みづくりやプラットフォームが必要になるかもしれません。
初めてCAEの導入・運用し、さらに管理・活用する場合には、IDAJをはじめとするCAEツールの販売・技術コンサルティングを提供するベンダーにご相談いただくのも一つの解決方法です。各社からは、様々なCAEの活用事例がWebサイト等を通して情報提供されていますし、操作トレーニングやセミナーなどではCAEに関するナレッジやノウハウを提供しているところがほとんどです。
IDAJは、CAEツールや最適化技術、SPDM(Simulation Process and Data Management)等のプラットフォームをご提供し、それらにツールに関する技術サポートを実施し、また、エンジニアリングコンサルティングによる技術構築と技術移管、CAEを利用しやすくまたは効率的な活用のためのシステム構築と開発を手掛けています。
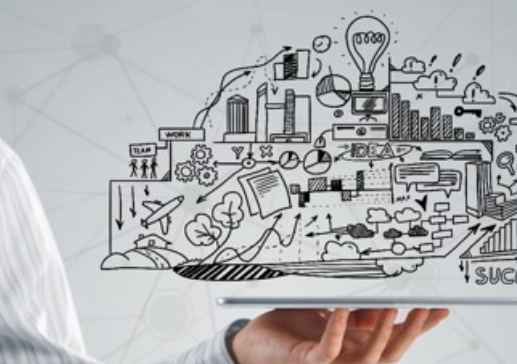
IDAJが提案するCAE分野トータルソリューション
IDAJは、CAE分野において単なるソフトウェア販売・サポートサービスのみならず、数多くのコンサルティング・エンジニアリングサービスやシステム開発、SPDM環境構築サービス等の経験を経て、高い技術力と幅広い提案力を有しています。
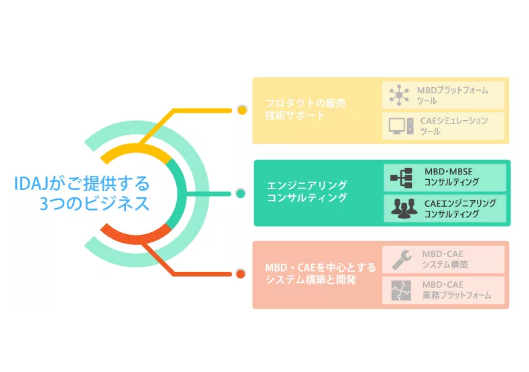
CAEコンサルティング
IDAJのコンサルティング事業は、MBD・CAE技術へフォーカスするとともに、お客様の製品開発プロセスと技術に対する深い理解に基づいたトータル・ソリューションを通じて、お客様の問題を解決することに唯一の価値を見出しています。
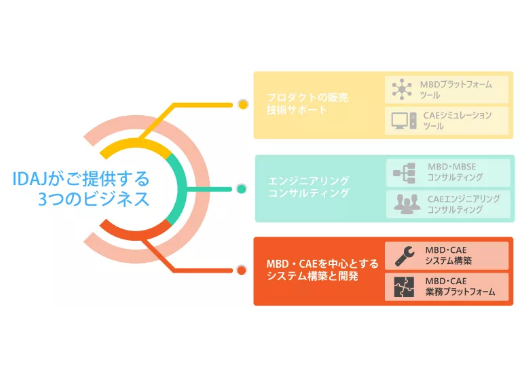
CAEツールを利用した
設計システム開発
設計・開発現場におけるデジタル・エンジニアリングの活用は、製品の競争力強化において欠かすことのできないアプローチの一つです。弊社は、会社設立以来、様々な分野においてCAEツールを利用した設計システムの構築に取り組んできました。
製品開発に貢献するこれからのCAE
─ Digital Engineering Solution by Products, Technologies and Services
ソフトウェアやハードウェアが目覚ましい発展を遂げた今、「CAE」は、従来の「解析」や「シミュレーション」という範疇を超えて、「バーチャル・エンジニアリング」としての役割を求められています。そこでIDAJでは、CAE技術の究極形は、コンピュータ上でバーチャルプロダクトを構築することであることを踏まえて、「製品開発に貢献するこれからのCAE」のために、3つのキーワードで「CAE」を再定義したいと考えています。
CAE for Virtual Product
従来のCAEが、製品の簡易化された形や特定の条件下で解析を行っていたのに対して、これからのCAEは、製品全体や製品が使われる実際の使用状況を想定した解析、すなわち「バーチャル・プロダクト」を解析対象とすることが求められています。そのためには、構造解析、熱流体解析、電磁場解析、音響解析などを融合させたMulti-Physics、0次元、1次元、3次元、リアルタイムなどを融合させたMulti-Scale、Co-Simulationなどの広範囲をカバーするソフトウェアと解析技術が必要です。同時に、お客様の製品開発に精通し、様々なCAE技術を複合的に利用する最適なソリューションをご提供しなければなりません。IDAJは、様々なソフトウェアと解析、お客様の製品開発に関連する知識と経験が豊富なエンジニアを抱えており、お客様の将来的な要求にお応えする体制を確立しています。
CAE for Innovation
CAEは、単に解析をして結果を評価するだけの技術にとどまらず、イノベーションに欠かせない戦略的な技術となりつつあります。厳しい競争環境で勝ち抜くには、今までとは異なる発想で、イノベーションを起こすための製品開発が求められています。そのためCAEには、最適化やデータマイニング、ビッグデータ、AIなどの様々な新しい技術と組み合わせてお客様のイノベーションをサポートするソリューションが必要です。IDAJは、CAE技術に対して積極的に最適化やデータマイニングを取り入れ、今後はAIなどにも取り組みます。
CAE for Process Transformation
CAEは、製品開発プロセスに深く浸透し、開発の上流工程から生産技術を含む下流工程にまで適用されており、近い将来、「バーチャル・プロダクト」が主導の開発プロセスが確立されるだろうと予想されます。そのためにCAEには、PLMやPDMなどの設計基幹データベースと連携してシームレスにデータをやり取りすることや、「バーチャル・プロダクト・ライフサイクル」の管理が求められます。また、設計者がCAEを使えるように自動化や専用システムの構築も重要です。IDAJは、CAE分野における自動化やPLM・PDMとの連携、専用システムの開発を専門的に担うチームがあり、今後のCAE環境の大きな発展に対応できるよう準備を整えています。
本ページでご紹介した内容の中には、弊社の経験・知見に基づいた主観的な記述を含んでおります。